Objectives of This Article
Objective | Description |
---|---|
Clarify Definitions | Define CPE and CPP in industrial contexts |
Compare Properties | Highlight mechanical, thermal, chemical differences |
Guide Selection | Offer criteria for choosing between CPE and CPP |
Showcase Uses | Present real‐world case studies across industries |
Answer FAQs | Resolve common queries on resin performance and sourcing |
CPE material incorporate chlorine into a polyethylene backbone, delivering exceptional flexibility, weather and chemical resistance, and inherent flame retardance—ideal for outdoor jacketing, seals, and hoses—while CPP material remain pure propylene polymers processed via cast extrusion to achieve outstanding clarity, tensile strength, and reliable low‑temperature heat sealing for high‑definition packaging films.
What is CPE resin?
CPE CPE resin, short for Chlorinated Polyethylene resin stands apart as a modified polyethylene bearing chlorine atoms along it s backbone. But here’s the kicker… this simple substitution transforms a commodity polymer into one offering remarkable weather and chemical resistance plus improved flame retardance. CPE grades vary in chlorine content—typically 25–42%—so performance scales with specification. In cable jacketing CPE prevents ozone cracking and UV damage. In automotive seals it endures oil contact and wide temperature swings. In roofing membranes it resists acid rain and oxidation far longer than plain polyethylene.
CPE processing mirrors that of common PE: extrusion, injection molding and calendaring; yet its polarity requires careful drying and screw design. Moisture can hydrolyze chlorinated chains causing defects. Ready for the good part? CPE remains compatible with PVC blends, yielding flexible, flame‐resistant compounds used in wire insulation. The compounder adjusts stabilizers to prevent dehydrochlorination when heated. Typical additive packages include metal soaps, antioxidants and UV absorbers.
Case study A: A European cable maker replaced EPDM jacketing with CPE grade exhibiting 1000‑hour weathering resistance—cutting warranty claims by 40%. Case study B: An agricultural film producer adopted CPE‑PVC blends, achieving cost savings versus ethylene‐vinyl acetate while maintaining tensile strength. Case study C: A seal manufacturer formulated CPE with 35% chlorine content for automotive door seals, meeting OEM longevity tests. This is where it gets interesting… CPE’s chlorine also enhances flame retardance, enabling UL 94 V‑0 ratings without halogenated additives in some cases.
Key CPE Properties
Property | Value / Range |
---|---|
Chlorine Content | 25–42 % |
Tensile Strength | 10–25 MPa |
Elongation at Break | 200–600 % |
Weathering Resistance | > 1000 h (Xenon arc) |
Flame Retardance Rating | UL 94 V‑2 to V‑0 |
Operating Temperature | –40 °C to +120 °C |
What is CPP resin?
Cast polypropylene (CPP) presents as a high‐clarity polymer prized in film and packaging sectors. What’s the real story? A simple shift from biaxial orientation yields a resin offering superior stiffness and heat seal strength versus conventional PP. CPP grades boast melting points around 160–170 °C and tensile strengths near 30 MPa, delivering robustness in high‐speed packaging lines. Its low moisture uptake preserves film integrity under humid conditions. CPP’s clarity rivals BOPP films while its seal initiation temperature remains lower, cutting energy costs on sealing jaws.
In food pouches, CPP layers provide heat seal reliability at temperatures as low as 120 °C. In lamination structures, CPP bonds effortlessly with PE or PET, enhancing package rigidity without sacrificing appearance. CPP films resist tearing and exhibit good barrier properties against oils and greases. But here’s the kicker… CPP handles printing inks superbly, ensuring sharp graphics on snack and confection packages. Processing involves cast extrusion onto chilled rolls, demanding precise nip controls and chill temperatures. Too cold and films crack; too hot and clarity fades.
Case study A: A Japanese snack producer switched from BOPP to CPP, halving cycle times and trimming seal failures by 65%. Case study B: A European pharmaceutical packager layered CPP with aluminum foil for blister backing, achieving enhanced puncture resistance. Case study C: An electronics firm adopted CPP‐based static‐dissipative films to protect sensitive components during transit. Ready for the good part? CPP’s recyclability under PP streams simplifies end‐of‐life handling compared with multi‐polymer laminates.
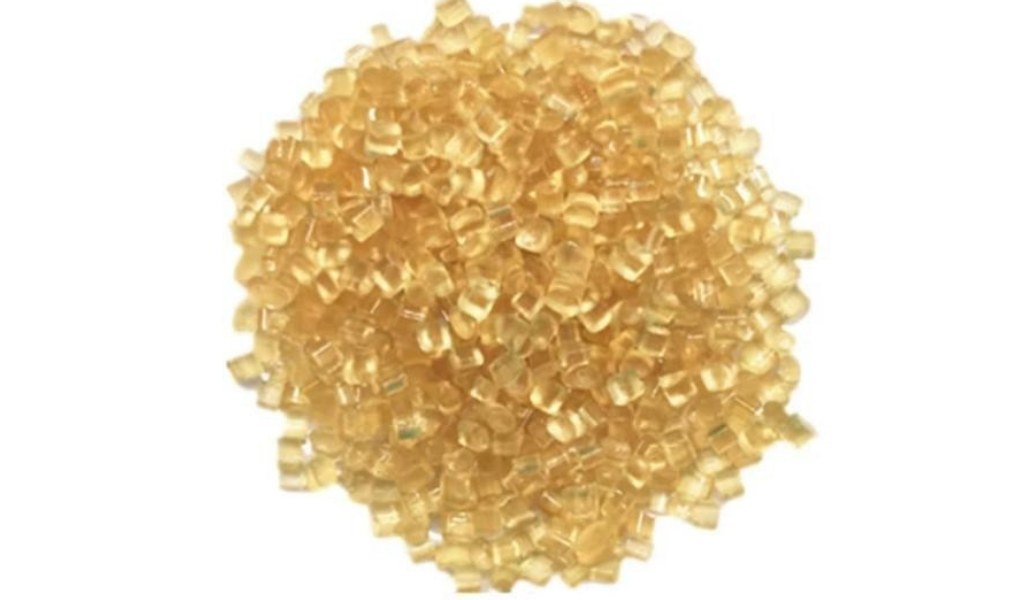
Key CPP Properties
Property | Value / Range |
---|---|
Melting Point | 160–170 °C |
Tensile Strength | 25–35 MPa |
Elongation at Break | 100–300 % |
Seal Initiation Temp | 120–140 °C |
Clarity (Haze %) | < 5 % |
Moisture Uptake | < 0.01 % |
Key differences in material properties
When engineers compare CPE material and CPP material, they often focus on thermal, mechanical, chemical traits that dictate performance under stress. This is where it gets interesting…
Thermal behavior vs mechanical strength
CPE operates reliably from –40 °C up to +120 °C thanks to its chlorine‐modified backbone. CPP handles higher continuous use temperatures, reaching +140 °C before softening. CPE delivers superior low‐temperature flexibility; CPP delivers higher rigidity at ambient and elevated temperatures. Applications requiring dynamic movement in cold conditions favor CPE. Rigid structures needing heat tolerance lean toward CPP.
Chemical resistance vs flexibility
CPE’s chlorine content shields chains against oils, solvents and UV, preventing cracking or swelling. CPP shows good resistance to water and most food acids but weak performance against hydrocarbon solvents. CPE’s elongation at break can exceed 500 %, enabling tight seals and gaskets. CPP elongation topping 300 % suffices for films but not for heavy elastic demands.
But here’s the kicker… these traits translate into distinct cost–performance trade‐offs. Engineers must weigh flexibility needs against temperature or chemical exposure.
Comparison of CPE and CPP Properties
Property | CPE Resins | CPP Resins |
---|---|---|
Temp Range (°C) | –40 to +120 | –20 to +140 |
Tensile Strength (MPa) | 10–25 | 25–35 |
Elongation (%) | 200–600 | 100–300 |
Chemical Resistance | Excellent solvents, oils | Moderate acids, water |
Flexibility | High | Moderate |
Clarity | Opaque | High |
Processing and handling differences
Manufacturers find processing conditions vary greatly between CPE resins and CPP resins. What’s the real story?
CPE processing mirrors standard polyethylene with extrusion and molding but demands careful moisture control. Prior to melt, CPE must dry under 80 °C for several hours to avoid hydrolysis and HCl release, which causes discoloration and embrittlement. Screw design includes gentler compression zones to prevent dechlorination. Cooling rates must balance dimension stability with stress relief. Typical output rates align with PE extruders, though throughput dips 10–20 % given heat‐stabilizer needs.
CPP processing uses cast extrusion onto chilled rollers. Ready for the good part? Unlike biaxially oriented films, cast CPP attains clarity via rapid chill. Film thickness control within ± 1 µm ensures consistent sealing. Chill roll temperatures between 10–20 °C optimize gloss. Melt temperatures run 200–220 °C for proper molecular orientation. Film winding tension impacts gauge uniformity; too high tension induces stress cracking during packaging use.
Handling at line speeds of 200–300 m/min requires robust nip rolls and anti‐scratch coatings for CPP. CPE compounds need corrosion‐resistant barrels given chlorine’s attack on steel; linings of Hastelloy or coated screws extend service life. But here’s the kicker… these tweaks in equipment lower maintenance costs over long runs.
Application use cases
Across industries, engineers match resin choice to application demands. This is where it gets interesting…
Packaging films vs cable jacketing
CPP excels in packaging clear pouches, lamination layers and twist films. Its stiffness boosts film feed accuracy in vertical form‐fill‐seal machinery. Food producers prize CPP’s seal strength and printability for branding. CPE shines in robust cable jacketing, tubing, roofing membranes and hoses. Its elasticity resists cracking under UV and ozone.
Industry Applications of CPE vs CPP
Industry | CPE Application | CPP Application |
---|---|---|
Packaging | Heavy‐duty industrial sacks | Heat‐seal food pouches |
Automotive | Seals, gaskets, hose linings | Protective packaging for parts |
Construction | Roofing membranes, weather‐seal components | Lamination facings on insulation boards |
Electrical | Outdoor cable jacketing | Insulative films for wrapping |
Agriculture | Protective greenhouse and pond liners | Crop packaging films |
Resin selection guidelines
Selecting between CPE resins and CPP resins hinges on balancing performance metrics with cost and supply factors. But here’s the kicker…
Cost factors and quality checks
Raw material pricing fluctuates based on feedstock—ethylene versus propylene costs vary regionally. CPE resins bear added cost from chlorination and stabilizers. CPP remains commodity‐priced yet demands tight process control which can add overhead. Bulk orders yield 5–15 % price breaks for both. Total cost of ownership analysis should include run rates, scrap rates and maintenance downtime tied to resin abrasiveness or corrosion.
Quality checks begin with melt flow index testing—CPE typical 2–8 g/10 min; CPP 1–5 g/10 min. Chlorine content assays verify spec compliance for CPE. Haze measurements under ASTM D1003 ensure CPP clarity. Additive dispersion testing confirms UV or heat stabilizer performance. Vendor audits on production sites assess traceability, technical support and export licensing. Ready for the good part? Suppliers offering on‐site trials reduce risk and speed qualification.
Resin selection guidelines
Assuming performance criteria match, logistics shape final choice. What’s the real story?
Resin availability in nearest port cuts lead times from weeks to days. CPE often ships from specialized plants; CPP from high‐volume facilities. Customs handling for chlorinated polymers may require additional paperwork. Storage conditions diverge: CPP can sit in ambient warehouses; CPE needs dry, covered yards to avoid moisture contact. Inventory buffering accounts for quarterly maintenance shutdowns.
Understanding differences between CPE resins and CPP resins unlocks informed procurement. CPE stands out for flexibility, weathering and flame retardance while CPP excels at clarity, seal strength and rigidity. Processing demands differ—drying and screw design for CPE, chill roll control for CPP. Use‐case studies reveal real benefits in packaging, cable and beyond. Selection hinges on performance needs, cost factors, logistics and supplier support. Aligning resin traits with application requirements ensures product reliability and cost efficiency. Contact our technical team for tailored resin trials and secure supply agreements that drive your business forward.
FAQ Section
Q1: What is CPE resin?
CPE resin refers to chlorinated polyethylene modified for enhanced flexibility, chemical resistance and weather durability in industrial applications.
Q2: What is CPP resin?
CPP resin denotes cast polypropylene grades featuring high clarity, tensile strength and low‐temperature heat seal performance for film and packaging.
Q3: How do CPE and CPP differ?
They differ in chemical makeup—chlorine in CPE versus pure polypropylene in CPP—and in properties like flexibility, temperature range, clarity and chemical resistance.
Q4: Which resin suits packaging films?
CPP suits clear, heat‐seal films and laminate layers while CPE fits heavy‐duty, weather‐resistant packaging where flexibility and UV resistance matter.
Q5: What selection criteria matter most?
Key criteria include thermal and mechanical requirements, chemical exposure, processing compatibility, cost factors, logistics and supplier technical support.