1. What Exactly is Chlorosulfonated Polyethylene (CSPE)?
Chlorosulfonated Polyethylene, commonly abbreviated as CSPE, carves out a distinct niche within the broad family of synthetic rubbers. It is not merely a modified plastic; rather, it is a true elastomer, engineered for resilience and durability under demanding conditions.
Its unique properties stem from a carefully controlled chemical modification of polyethylene, transforming a common thermoplastic into a high-performance thermosetting rubber upon vulcanization. This transformation process involves the strategic introduction of chlorine and chlorosulfonyl groups onto the polyethylene backbone.
But what does this mean in practical terms? These chemical alterations are fundamental to CSPE’s performance, imbuing it with a combination of resistances – to chemicals, temperature extremes, and weathering – that are often superior to many other elastomers. The polyethylene chain provides a stable, saturated backbone, which is a key contributor to its excellent resistance against ozone and UV degradation.
The chlorine atoms, typically present at 20-40% by weight, enhance its resistance to oils and flame, while also influencing its hardness and flexibility. The chlorosulfonyl groups (-SO2Cl), present in smaller amounts (usually 1-2% sulfur by weight), are the crucial reactive sites. These sites allow for cross-linking or vulcanization, a process that converts the raw polymer into a strong, elastic material with the desirable rubbery characteristics.
This carefully balanced molecular architecture results in a material that can withstand harsh environments where many other polymers would falter, making it a go-to solution for critical applications.
The historical journey of CSPE is largely intertwined with E.I. du Pont de Nemours and Company (DuPont), who pioneered its development in the mid-20th century. It all began with a quest for superior materials.
DuPont commercially introduced CSPE in 1951 under the trade name Hypalon. This launch marked a significant milestone, providing industries with a novel synthetic rubber that offered an unparalleled blend of durability and resistance. The development was driven by the increasing need for materials that could perform reliably in aggressive chemical environments and withstand severe outdoor exposure. Hypalon quickly became the benchmark for CSPE.
Key milestones in its development included the refinement of manufacturing processes to ensure consistent quality and the creation of various grades tailored to specific end-use requirements by adjusting chlorine and sulfur content, as well as polymer viscosity. For decades, Hypalon was specified for a wide array of demanding applications.
However, in a significant market shift, DuPont ceased production of Hypalon in April 2010, citing declining demand and the high costs associated with manufacturing chlorinated materials, particularly in light of evolving environmental regulations. Despite DuPont’s exit, the generic material, Chlorosulfonated Polyethylene, did not disappear.
Other chemical companies around the globe have continued its production, often marketing their CSPE grades as equivalents to the former Hypalon series. This ensures that industries still have access to this high-performance elastomer, building on the legacy and extensive application knowledge established during the Hypalon era.
Characteristic | Description |
---|---|
Polymer Family | Synthetic Rubber (Elastomer) |
Base Polymer | Polyethylene |
Key Modifiers | Chlorine (Cl), Chlorosulfonyl groups (-SO2Cl) |
Backbone Structure | Saturated (no double bonds in main chain) |
Typical Cl Content | 20-40% by weight |
Typical S Content | 1-2% by weight (from -SO2Cl groups) |
Vulcanization | Achieved via chlorosulfonyl groups, leading to a thermoset elastomer |
Primary Benefit | Excellent resistance to ozone, UV, weathering, many chemicals, and good heat resistance. |
Original Trade Name | Hypalon (DuPont – production ceased 2010) |
Current Status | Produced by various global manufacturers as generic CSPE or under different trade names. |
2. How is Chlorosulfonated Polyethylene Produced and What Are Its Main Types?
The synthesis of Chlorosulfonated Polyethylene is a testament to sophisticated polymer chemistry, transforming a basic hydrocarbon polymer into a high-value elastomer. Let’s unpack the manufacturing journey.
The process typically commences with polyethylene, selected for its specific molecular weight and structure, as the foundational raw material. This polyethylene is usually dissolved in an inert solvent, such as carbon tetrachloride (though solvent-free processes like slurry or fluid-bed reactors are also employed by some manufacturers to address environmental concerns associated with chlorinated solvents). The core transformation hinges on two simultaneous or sequential chemical reactions: chlorination and chlorosulfonation. During chlorination, chlorine gas (Cl2) is meticulously introduced into the polyethylene solution or suspension. This reaction, often initiated by free-radical generators like ultraviolet light or chemical catalysts (e.g., azobisisobutyronitrile – AIBN), involves the substitution of hydrogen atoms on the polyethylene backbone with chlorine atoms.
The degree of chlorination is a critical control parameter, directly influencing the resultant CSPE’s oil resistance, flammability, hardness, and low-temperature flexibility. Higher chlorine levels generally enhance fluid resistance but can stiffen the polymer. Concurrently or subsequently, chlorosulfonation occurs. This step involves reacting the polymer with a mixture of chlorine gas and sulfur dioxide gas (SO2), or more commonly with sulfuryl chloride (SO2Cl2). This reaction grafts chlorosulfonyl (-SO2Cl) groups onto the polymer chain. These groups are of paramount importance as they provide the active sites for subsequent vulcanization (cross-linking), which is essential for developing the material’s robust elastomeric properties, such as tensile strength, elasticity, and permanent set resistance.
The entire manufacturing sequence demands precise control over reaction conditions – temperature, pressure, reactant concentrations, and residence time – to achieve the desired degree of chlorination and chlorosulfonation, ensuring consistent product quality and performance characteristics. Following the reactions, the modified polymer, now CSPE, is separated from the solvent (if used), thoroughly washed to remove residual reactants and byproducts, and then carefully dried.
The final product is typically supplied as chips, crumbs, or pellets, ready for compounding and processing by rubber product manufacturers. This intricate process allows for the creation of a versatile elastomer with a precisely tailored property profile, ready to meet diverse and demanding application needs.
Chlorosulfonated Polyethylene is not a monolithic entity; rather, it encompasses a spectrum of grades, each engineered with specific characteristics to cater to a wide array of applications. But how do these grades differ, and what does it mean for the end-user?
Manufacturers differentiate CSPE grades primarily based on three key parameters: chlorine content, sulfur content (which correlates to the concentration of chlorosulfonyl groups), and Mooney viscosity (an empirical measure of the polymer’s molecular weight and processability). These variations translate directly into a diverse range of physical properties, processing behaviors, and curing characteristics.
For instance, CSPE grades with a lower chlorine content (typically in the 20-30% range by weight) tend to exhibit superior low-temperature flexibility and higher resilience. These grades are often the preferred choice for applications where performance in frigid environments is a critical design criterion, such as certain types of seals or flexible conduits exposed to arctic conditions.
Conversely, grades with a higher chlorine content (which can be 40% or even slightly more) boast enhanced resistance to oils, fuels, and a broader range of chemicals, along with significantly reduced flammability. These high-chlorine variants are frequently specified for more demanding applications, such as industrial hoses designed for aggressive chemical transfer, robust linings for chemical storage tanks, or protective jacketing for cables in hazardous locations.
The Mooney viscosity of the CSPE grade also plays a crucial role. Lower Mooney viscosity grades are generally easier to process; they mix more readily with compounding ingredients (like fillers, plasticizers, and curatives) and exhibit better flow characteristics during molding or extrusion operations. This makes them suitable for manufacturing intricately shaped articles or products requiring a very smooth surface finish.
On the other hand, higher Mooney viscosity grades typically yield cured products with superior physical properties, such as higher tensile strength, improved tear resistance, and better green strength (the strength of the uncured rubber compound).
These are often selected for heavy-duty applications where maximum durability is essential. Furthermore, some CSPE grades are specifically formulated for compatibility with particular curing systems. While most CSPEs can be vulcanized using metal oxides (historically lead oxide, though its use has significantly declined due to toxicity, with magnesium oxide and other alternatives now common), organic peroxides, or specialized sulfur-based cure packages, certain grades are optimized to achieve specific end-properties like exceptional heat resistance or very low compression set when cured with a particular system.
This ability to select a CSPE grade with a precisely tailored balance of properties makes it an exceptionally adaptable elastomer, empowering engineers and product designers across numerous industries to meet highly specific performance targets.
Parameter | Low Value Effect on CSPE | High Value Effect on CSPE |
---|---|---|
Chlorine Content | Better low-temp flex, higher resilience, lower density. | Better oil/fuel/chemical resistance, flame retardancy, higher hardness. |
Sulfur Content (-SO2Cl) | Slower cure rate, may require more active cure systems. | Faster cure rate, higher crosslink density possible. |
Mooney Viscosity | Easier processing, better flow, lower green strength. | Harder processing, higher green strength, often better physicals. |
Crystallinity (Residual) | More amorphous, more rubbery. | Slightly stiffer, can affect low-temp properties. |
Polymer MW Distribution | Affects processability and balance of physical properties. | Affects processability and balance of physical properties. |
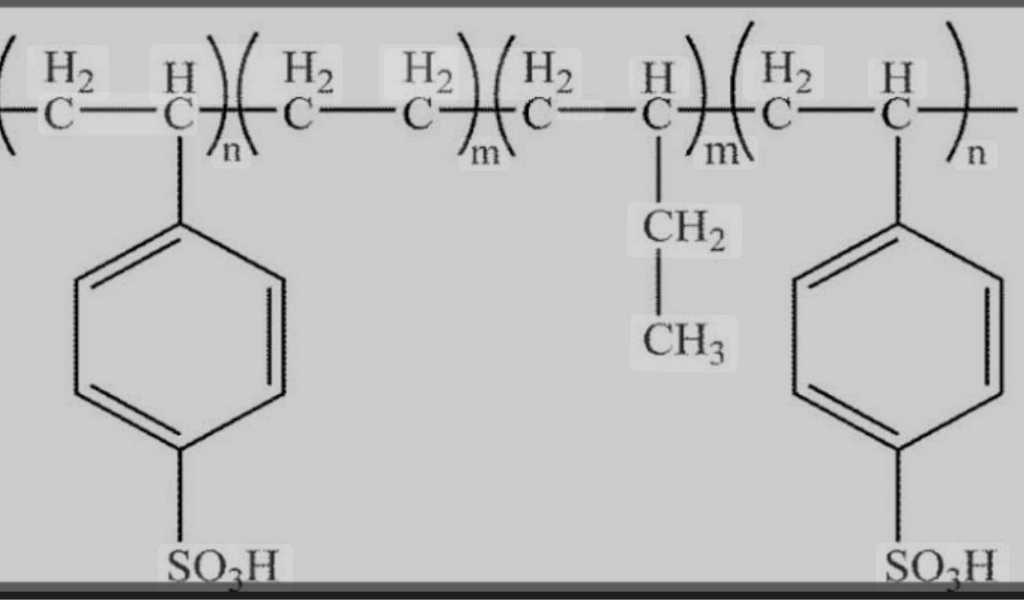
3. What are the Defining Properties and Unique Advantages of CSPE?
Chlorosulfonated Polyethylene (CSPE) distinguishes itself within the crowded field of synthetic elastomers through a unique constellation of inherent properties, meticulously engineered at a molecular level.
What truly sets this material apart from its counterparts? Its defining characteristics are not accidental; they are the direct result of the chlorination and chlorosulfonation processes that transform a simple polyethylene backbone into a high-performance material. This chemical modification imbues CSPE with an exceptional capacity to resist a formidable array of environmental aggressors and chemical attacks. This intrinsic robustness translates directly into enhanced longevity and unwavering reliability in service – attributes of paramount importance for B2B users when selecting materials for high-value, critical, or long-service-life components.
The performance profile of Chlorosulfonated Polyethylene often justifies its selection over other, perhaps less costly, elastomers, particularly when the anticipated operational conditions are severe or when an extended, maintenance-free service life is a primary design objective.
Furthermore, its versatility in compounding allows for the precise fine-tuning of its properties, enabling formulators to meet highly specific application requirements, thereby adding another significant layer to its already impressive list of advantages. This adaptability ensures that CSPE can be optimized for a diverse range of end-uses, from flexible hosing to rigid coatings.
Detailed look at key physical resistance properties
The physical endurance of Chlorosulfonated Polyethylene is a cornerstone of its utility. Let’s examine its resilience more closely. One of its most celebrated attributes is its truly outstanding resistance to ozone.
Ozone (O3), a highly reactive allotrope of oxygen present in the atmosphere (especially in polluted urban environments or generated by electrical equipment), can rapidly degrade many common unsaturated rubbers, leading to characteristic cracking and premature failure.
CSPE, by virtue of its saturated polymer backbone (meaning it lacks the vulnerable carbon-carbon double bonds found in many other elastomers), exhibits little to no degradation even when exposed to high concentrations of ozone, and importantly, even when under mechanical stress or strain. This makes it an ideal candidate for a multitude of outdoor applications where ozone exposure is an unavoidable reality. Similarly, its performance against the relentless onslaught of ultraviolet (UV) radiation from sunlight is excellent. Many polymeric materials become brittle, discolor, or lose their mechanical integrity upon prolonged exposure to UV rays.
Chlorosulfonated Polyethylene, however, maintains its physical properties and aesthetic appearance over extended periods of outdoor service. This inherent UV stability is crucial for applications such as long-lasting roofing membranes, exposed architectural fabrics, outdoor cable jacketing, and protective coatings that must endure years of direct sunlight. Beyond ozone and UV, CSPE’s general weathering resistance is exemplary.
This holistic term encompasses its ability to withstand the combined effects of sunlight, moisture (rain, humidity, condensation), fluctuating temperatures, and various atmospheric pollutants without significant deterioration of its functional properties. Articles fabricated from Chlorosulfonated Polyethylene can confidently be specified for decades of outdoor service, retaining their flexibility, strength, and protective capabilities. This comprehensive shield against the elements is a primary driver for its selection in construction and exterior applications.
Detailed look at key chemical resistance properties
Beyond its physical resilience, Chlorosulfonated Polyethylene boasts a formidable defense against a wide spectrum of chemical agents.
How does it fare against aggressive substances? CSPE generally exhibits good to excellent resistance against many corrosive and oxidizing chemicals. This includes many inorganic acids, such as sulfuric acid and nitric acid (though performance varies with concentration and temperature – highly concentrated oxidizing acids at elevated temperatures can be challenging for any polymer). It also stands up well to a variety of alkaline solutions. Its performance with mineral oils, greases, and aliphatic hydrocarbons is typically rated as good, making it suitable for seals, hoses, and linings in contact with these substances.
However, it is important to note its limitations: CSPE tends to swell significantly when exposed to aromatic hydrocarbons (like benzene, toluene, xylene) and chlorinated solvents (such as trichloroethylene or methylene chloride). This swelling can lead to a loss of mechanical strength and dimensional stability, so applications involving these types of solvents require careful consideration or alternative material choices. The chlorine content in CSPE contributes significantly to this chemical resistance profile.
The polar chlorine atoms make the polymer less susceptible to attack by non-polar oils and hydrocarbons compared to non-polar rubbers like EPDM or natural rubber. This broad chemical compatibility allows Chlorosulfonated Polyethylene to be reliably used in demanding environments, such as within chemical processing plants for tank linings, valve components, pump diaphragms, and specialized hosing, where lesser materials would quickly succumb to degradation. Its ability to handle a diverse range of chemical exposures, from acidic to alkaline, and including many industrial fluids, underpins its value in these critical sectors.
Mechanical properties
Chlorosulfonated Polyethylene, when properly compounded and vulcanized, delivers a robust suite of mechanical properties that contribute to its durability in service.
What about its strength and elasticity? Typical tensile strength values for CSPE compounds can range from moderate to good, often falling in the 10 to 25 MPa (1450 to 3625 psi) range, depending on the specific grade, reinforcement type and loading (e.g., carbon black, mineral fillers), and cure system used. Elongation at break is generally good, often exceeding 200-500%, indicating good flexibility and the ability to withstand deformation without rupture. Tear resistance is also typically good, which is important for applications subjected to physical abuse or where a tear could propagate and lead to failure.
Abrasion resistance of CSPE is considered fair to good; while not as outstanding as some specialized abrasion-resistant rubbers like high-cis polybutadiene, it is sufficient for many industrial applications, including hose covers and conveyor belt surfaces, especially when formulated with appropriate reinforcing fillers.
Compression set values, which measure the ability of a material to recover its original thickness after prolonged compressive stress at elevated temperatures, can be formulated to be quite low for CSPE, particularly with peroxide cure systems.
Low compression set is critical for sealing applications to ensure long-term sealing effectiveness. The hardness of CSPE compounds can be varied over a wide range, typically from around 50 Shore A (relatively soft and flexible) up to 90 Shore A or even higher (quite hard and stiff), by adjusting the polymer grade, type and amount of fillers, and plasticizer content. This versatility in hardness allows CSPE to be tailored for applications ranging from soft seals to semi-rigid protective sheets.
Thermal properties
Chlorosulfonated Polyethylene exhibits a commendable performance across a useful range of temperatures.
How does it handle the heat and cold? Its general continuous service temperature range is typically cited as -20°C to 120°C (-4°F to 248°F), with some grades and formulations capable of intermittent exposure to slightly higher temperatures, perhaps up to 140°C or 150°C. Specialized grades, particularly those with lower chlorine content, can offer improved low-temperature flexibility, pushing the lower service limit down towards -35°C or even -40°C for certain applications, although it may stiffen considerably at these extremes.
Its heat aging resistance is generally good, meaning it retains a significant portion of its physical properties after prolonged exposure to elevated temperatures within its service range. This is attributed to its saturated backbone, which is inherently more stable against thermal oxidation than unsaturated rubbers. This thermal stability makes CSPE suitable for under-hood automotive components, industrial equipment operating at elevated temperatures, and roofing membranes exposed to intense solar heating.
However, like all polymers, its properties will degrade over time with prolonged exposure to very high temperatures, and its maximum service temperature should not be exceeded to ensure product integrity and safety.
Electrical properties
While not primarily selected for its electrical insulation properties in the same way as materials like silicone rubber or EPR (ethylene propylene rubber), Chlorosulfonated Polyethylene does possess useful dielectric characteristics.
Can it be used in electrical applications? Yes, CSPE exhibits good dielectric strength, making it suitable for wire and cable jacketing, particularly in applications where its excellent environmental resistance, flame retardancy, and toughness are also required. Its volume resistivity is typically high enough for low and medium voltage insulation and jacketing.
The presence of chlorine, while beneficial for flame retardancy, can slightly increase dielectric loss compared to purely hydrocarbon polymers, but for many power and control cable applications, its electrical properties are more than adequate. Its ability to withstand ozone, UV, moisture, and chemical exposure makes CSPE-jacketed cables very durable in harsh industrial, marine, or outdoor environments. It provides a robust protective layer that maintains electrical integrity under challenging conditions.
Thus, while not a primary high-voltage insulator, its overall balance of electrical and physical robustness carves out a niche in specialized electrical applications.
Flame retardancy
An important characteristic of Chlorosulfonated Polyethylene is its inherent flame retardancy.
Does it burn easily? Due to its significant chlorine content (typically 20-40%), CSPE exhibits good resistance to ignition and flame propagation compared to many hydrocarbon-based elastomers. When exposed to a flame, the chlorine in the polymer tends to interfere with the combustion process, acting as a flame retardant. While CSPE will burn if exposed to a sufficiently intense flame source, it generally self-extinguishes or burns slowly once the ignition source is removed, especially in formulations designed to maximize this property.
This characteristic can be further enhanced by the addition of synergistic flame retardant additives, such as antimony trioxide (though its use is also under scrutiny) or phosphorus-based compounds. This makes CSPE a valuable material for applications where fire safety is a concern, such as in wire and cable jacketing for public transport or industrial facilities, conveyor belts in mines, construction materials like roofing membranes and architectural fabrics, and protective clothing or equipment.
Its ability to meet various flammability standards without excessive loading of additives (which can sometimes compromise other properties) is a distinct advantage.
Colorability and color stability
Chlorosulfonated Polyethylene offers excellent colorability and maintains its color exceptionally well over time, even under prolonged outdoor exposure.
What about aesthetics and identification? Unlike many elastomers that require carbon black for UV protection and are thus limited to black or very dark shades, CSPE\’s inherent UV stability means it can be compounded in a virtually unlimited range of vibrant, light-stable colors. This includes bright whites, pastels, and deep tones. This is a significant advantage for applications where aesthetics are important, such as architectural fabrics, designer roofing membranes, consumer goods, or safety equipment where color-coding is essential for identification (e.g., colored hoses or cable jackets).
The color in CSPE products remains stable over long periods without significant fading or yellowing, even when exposed to intense sunlight and harsh weather conditions. This lasting color integrity enhances the visual appeal and functional lifespan of the end products, making CSPE a preferred choice when both performance and long-term appearance are critical design factors.
Discussion of its unique benefits when compared to other common elastomers
When Chlorosulfonated Polyethylene is systematically compared with other widely used elastomers, its unique blend of advantageous properties becomes particularly evident, highlighting its role as a specialized problem-solver. How does it stack up against the competition?
- Versus Natural Rubber (NR) and Styrene-Butadiene Rubber (SBR): While NR and SBR offer excellent mechanical properties like high tensile strength and abrasion resistance at a lower cost, they are highly susceptible to degradation from ozone, UV radiation, and many chemicals. CSPE vastly surpasses them in all these environmental resistance aspects, offering significantly longer service life in outdoor or chemically aggressive environments. CSPE also provides better heat resistance and inherent flame retardancy.
- Versus EPDM (Ethylene Propylene Diene Monomer): EPDM shares excellent ozone, UV, and weathering resistance with CSPE, and often exhibits better low-temperature flexibility. However, standard EPDM grades generally have poor resistance to oils and aliphatic hydrocarbon fuels, whereas CSPE offers good resistance in these areas. CSPE also typically provides better flame retardancy due to its chlorine content and can sometimes be easier to process or adhere to other substrates in certain applications.
- Versus Nitrile Rubber (NBR): NBR is renowned for its excellent resistance to petroleum-based oils, fuels, and greases. While CSPE\’s oil resistance is good, high-nitrile NBR usually outperforms it for very aggressive fuel or oil immersion. However, NBR has poor resistance to ozone, UV, and weathering, making it unsuitable for most outdoor applications unless specifically compounded with protective additives, which can compromise other properties. CSPE shines in applications requiring both moderate oil resistance and excellent outdoor durability.
- Versus Neoprene (CR – Polychloroprene): Neoprene is another chlorinated elastomer that shares several positive attributes with CSPE, including good weathering resistance, moderate oil resistance, and inherent flame retardancy. However, CSPE generally offers superior resistance to strong oxidizing chemicals (like concentrated acids) and often exhibits better long-term heat aging characteristics and color stability. Depending on the grade, CSPE might also offer advantages in specific processing or adhesion characteristics. The choice between CSPE and CR often comes down to the specific chemical environment, temperature exposure, and precise balance of properties required.
This comparative analysis underscores that while no single elastomer is universally superior, CSPE carves out a valuable niche by offering a robust and well-rounded combination of resistances that is difficult to achieve with other materials, especially when color stability and inherent flame retardancy are also key requirements.
Property | CSPE (General) | Natural Rubber (NR) | EPDM | Nitrile Rubber (NBR) | Neoprene (CR) |
---|---|---|---|---|---|
Ozone Resistance | Excellent | Poor | Excellent | Poor | Good |
UV Resistance | Excellent | Poor | Excellent | Poor | Good |
Weathering | Excellent | Poor | Excellent | Fair | Good |
Oil/Fuel Resistance | Good | Poor | Poor | Excellent (High ACN) | Moderate |
Chemical Resistance | Good to Excellent | Fair | Good (Non-oxidizing) | Fair to Good | Good |
Heat Resistance | Good (to 120°C+) | Fair (to 70-80°C) | Good (to 130°C+) | Good (to 100-120°C) | Good (to 100-120°C) |
Low-Temp Flex | Fair to Good (-40°C) | Good (-50°C) | Excellent (-55°C) | Fair to Good (-40°C) | Good (-40°C) |
Flame Retardancy | Good (Inherent) | Poor | Poor | Poor | Good (Inherent) |
Color Stability | Excellent | Poor | Good | Poor | Fair (can discolor) |
Tensile Strength | Moderate to Good | Excellent | Good | Good to Excellent | Good |