4. In Which Applications and Industries is CSPE Commonly Utilized?
Chlorosulfonated Polyethylene‘s formidable array of robust properties makes it an exceptionally versatile material, enabling its penetration into a multitude of demanding applications across a diverse spectrum of industrial landscapes. Before we dive into the applications, if you’re new to CSPE, I suggest reading “What Is CSM Material” for a quick material overview.The material’s commendable processability allows it to be readily formed into various intricate shapes and robust forms, including flexible sheets for lining, durable tubes and hoses, resilient protective coatings, and precision-molded articles, thereby further broadening its already extensive applicability
So, where exactly does this high-performance elastomer make its mark? Its inherent ability to withstand harsh chemical environments, extreme weather conditions, and prolonged operational stress means it is frequently the material of choice for components where failure is simply not an option and where an extended, trouble-free service life is a paramount economic and safety consideration.
From the rigorous demands of heavy industrial settings to specialized, high-value consumer goods, CSPE consistently delivers reliable and predictable performance. The material’s commendable processability allows it to be readily formed into various intricate shapes and robust forms, including flexible sheets for lining, durable tubes and hoses, resilient protective coatings, and precision-molded articles, thereby further broadening its already extensive applicability.
B2B clients, including engineers, specifiers, and product designers, often specify Chlorosulfonated Polyethylene when they require a material that offers a superior, well-balanced combination of chemical resistance, enduring weatherability, and stable temperature performance that many commodity rubbers or even some other specialty elastomers cannot consistently match.
Its long and proven track record in some of the most challenging operational environments has firmly solidified its position as a go-to elastomer for critical, performance-driven applications where material integrity is key.
Examination of common uses in various industrial and consumer products
One of the most prominent and well-established applications for Chlorosulfonated Polyethylene is in the meticulous manufacturing of high-performance industrial hoses.
Here’s the real story behind these critical conduits. These are not your average garden hoses; they are engineered to safely convey highly aggressive chemicals, abrasive slurries, hot oils, or other challenging media under pressure. CSPE’s excellent chemical resistance and good mechanical strength, coupled with its abrasion resistance, make it an outstanding candidate for either the inner tube (in direct contact with the conveyed medium) or the robust outer cover (providing protection against external abrasion, weathering, and ozone attack) of such specialized hoses.
For instance, hoses deployed in the chemical processing industry for transferring concentrated acids or reactive solvents, or those used for high-pressure industrial cleaning applications involving harsh detergents, frequently rely on CSPE for their construction. Another major and highly visible area of application is in roofing membranes.
What makes it suitable for protecting our buildings? Single-ply roofing systems fabricated from CSPE are highly valued and widely specified for their exceptional, long-term weatherability, outstanding UV radiation resistance, and impressive overall longevity.
These durable membranes can effectively withstand extreme temperature fluctuations, damaging hail, significant wind uplift forces, and prolonged exposure to moisture, providing durable, flexible, and watertight protection for large commercial, industrial, and institutional buildings, often for service lives extending several decades.
The availability of CSPE in light, reflective colors also contributes significantly to the development of cool roofing systems, which can significantly reduce building cooling costs and mitigate the urban heat island effect. Protective coatings represent another significant and widespread use domain for Chlorosulfonated Polyethylene.
How does it shield our infrastructure? CSPE-based paints and liquid-applied coatings are frequently applied to vulnerable steel structures, concrete surfaces, and other substrates to provide robust, long-lasting protection against corrosion, aggressive chemical attack, and the damaging effects of weathering.
Think of critical infrastructure like bridges spanning corrosive marine environments, offshore oil and gas platforms battered by saltwater and storms, large-scale chemical storage tanks holding aggressive substances, and the concrete basins and channels within wastewater treatment facilities; many of these rely on the superior barrier properties and durability of CSPE coatings for their long-term integrity and operational safety.
You might be wondering about smaller, yet equally vital, components. Indeed, CSPE is also extensively used for manufacturing a variety of seals, gaskets, and O-rings, particularly in applications where resistance to specific chemicals, elevated temperatures, or persistent ozone exposure is a critical requirement.
These components are indispensable in many automotive systems (e.g., seals for air conditioning refrigerants or certain aggressive fluids), complex industrial machinery, and various fluid handling and control equipment, ensuring reliable, leak-tight performance under demanding and often fluctuating operational conditions.
Its utility further extends to specialized wire and cable jacketing, especially for cables that must endure harsh environmental exposures, offer dependable flame retardancy, or resist mechanical abuse. The material’s adequate dielectric properties, when combined with its exceptional toughness and environmental resilience, make it a suitable choice for these protective outer coverings, safeguarding the electrical conductors within.
Specific examples of its application across different industries
Delving into the specifics of various industrial sectors, the automotive industry, for example, utilizes Chlorosulfonated Polyethylene for a range of demanding under-the-hood and exterior applications.
What is its precise role in our vehicles? Components such as power steering hoses, which must handle hydraulic fluids at elevated temperatures and pressures, certain types of fuel lines and vapor tubes (especially those designed for compatibility with aggressive biofuel blends that can degrade other elastomers), and various critical seals and gaskets benefit immensely from CSPE’s inherent resistance to automotive fluids, engine compartment heat, and atmospheric ozone.
While a plethora of other elastomers are also employed in automotive design, Chlorosulfonated Polyethylene material often fills a crucial niche where a specific and superior combination of these resistances is non-negotiable for performance and longevity. In the expansive construction industry, beyond its well-established use in roofing membranes, Chlorosulfonated Polyethylene is frequently found in high-performance expansion joint seals that accommodate structural movement, durable pond liners and canal liners for water containment, and robust geomembranes used in critical containment applications such as landfill lining or secondary containment for chemical storage areas.
Its exceptional durability and high resistance to environmental stress cracking (ESC) are highly valued attributes for these long-term civil engineering uses, where material failure could have significant environmental or financial consequences. For instance, liners for large water reservoirs or irrigation canals fabricated from CSPE can provide many years, even decades, of reliable, leak-free service. The chemical processing industry (CPI) is a natural and extensive domain for Chlorosulfonated Polyethylene applications.
This is where its profound chemical resistance truly comes into its own. It is widely employed for fabricating protective tank linings to shield steel or concrete tanks from the corrosive action of their contents, for manufacturing durable and chemically inert pump diaphragms, for valve seats and seals handling aggressive media, and, as previously mentioned, for constructing extensive networks of specialized hosing and piping systems designed for chemical transfer.
Its proven ability to handle a diverse range of acids (including oxidizing acids), bases, solvents, and various oxidizing agents makes it an indispensable material in many challenging chemical plant operations. In the electrical and electronics industry, CSPE’s good dielectric strength, when coupled with its excellent flame retardancy and outstanding resistance to weathering, ozone, and moisture, makes it a preferred material for the protective jacketing on a variety of power cables, control cables, and industrial wiring.
This is particularly true for cables intended for use in harsh or hazardous environments, such as in mining operations, shipbuilding, offshore installations, or in outdoor settings where they are directly exposed to the full force of the elements. The material also finds application in certain types of electrical connectors, insulators, and switchgear components where environmental robustness is key.
The marine industry also leverages CSPE for applications like inflatable boats (such as rigid-hulled inflatable boats or life rafts), dock bumpers, and protective coatings for ship components exposed to saltwater and harsh weather.
Its resistance to UV, ozone, and abrasion, along with its colorability, makes it suitable for these demanding marine uses. Lastly, in general industrial applications, CSPE can be found in conveyor belt covers (especially for belts handling oily or chemically active materials), coatings for industrial fabrics (e.g., for tarpaulins or flexible containers), resilient roll covers for printing and processing machinery, and even in specialized printing blankets.
These diverse examples collectively illustrate the remarkable breadth of Chlorosulfonated Polyethylene’s utility, a versatility driven by its inherent capacity to perform reliably and durably where many other materials would falter or fail prematurely, thereby cementing its status as a key problem-solving elastomer across a wide and varied industrial spectrum.
Industry Sector | Illustrative CSPE Applications | CSPE Properties Leveraged in Sector |
---|---|---|
Automotive | Power steering hoses, specific fuel/vapor lines, A/C seals, wire harness components, some belt constructions. | Resistance to automotive fluids (oils, fuels, coolants), heat, ozone; good flexibility. |
Construction | Single-ply roofing membranes, architectural fabrics, expansion joint seals, pond/canal/landfill liners, concrete coatings. | Exceptional weatherability (UV, ozone, moisture), long-term durability, water impermeability, color stability. |
Chemical Processing | Tank linings (acid/alkali/oxidizer storage), chemical transfer hoses, pump diaphragms, valve seats/linings, gaskets. | Broad chemical resistance, heat resistance, good mechanical strength. |
Electrical/Electronic | Protective jacketing for power/control/instrumentation cables, connectors, insulators (especially for harsh environments). | Good dielectric strength, excellent flame retardancy, weather/ozone/chemical resistance, toughness. |
Marine | Inflatable boats (e.g., RIBs, life rafts), dock bumpers, coatings for shipboard equipment, flexible tanks. | UV/ozone/saltwater resistance, abrasion resistance, colorability, air/water tightness. |
General Industrial | Conveyor belt covers (oily/chemical exposure), industrial fabric coatings, roll covers (printing, processing), printing blankets. | Abrasion resistance, chemical resistance, weatherability, good dynamic properties, non-staining characteristics. |
5. What Safety Precautions and Environmental Aspects are Associated with CSPE?
While Chlorosulfonated Polyethylene (CSPE) stands out for its remarkable array of performance benefits and robust durability in challenging applications, it is imperative, as with any industrial material, that its handling, processing, and end-of-life lifecycle are managed with a thorough consideration of safety protocols and environmental implications.
What critical factors must professionals in B2B environments be acutely aware of to ensure responsible use? A comprehensive understanding of these aspects transcends mere regulatory compliance; it is fundamentally about fostering responsible manufacturing practices, ensuring workplace safety, and promoting diligent product stewardship.
For B2B users, this knowledge is absolutely crucial for establishing and maintaining safe operational workplaces, for proactively minimizing any potential environmental impact stemming from CSPE use or disposal, and for making holistically informed decisions regarding material selection, application design, and ultimate end-of-life management strategies.
The inherent chlorinated nature of CSPE, along with the various chemicals often employed in its production, compounding, and vulcanization, necessitates the implementation of specific, well-defined protocols throughout its entire lifecycle, from the initial raw material manufacturing stages right through to its final disposal or repurposing.
Comprehensive handling guidelines, potential workplace hazards, and necessary personal protective equipment (PPE)
Handling Chlorosulfonated Polyethylene, particularly when it is in its uncured, raw polymer state or during processing operations such as milling, calendering, extrusion, or grinding where dust, fumes, or vapors may be generated, demands strict adherence to comprehensive safety guidelines and best practices.
So, how can these potential risks be effectively identified, mitigated, and managed in an industrial setting? Uncured CSPE, as supplied by manufacturers, may contain small amounts of residual solvents or unreacted monomers stemming from its polymerization process; these substances could potentially pose inhalation hazards or cause skin irritation or sensitization upon direct contact.
During the compounding and processing stages – for example, when CSPE is mixed with fillers, plasticizers, curatives, and other additives on a two-roll mill, or when it is heated and shaped through extrusion or molding – fine particulate dust and various chemical fumes can be released into the workplace atmosphere.
A significant concern is the potential for thermal decomposition if the material is inadvertently overheated beyond its recommended processing temperatures. Such decomposition can liberate hazardous gases, most notably hydrogen chloride (HCl), which is corrosive and an irritant to the respiratory system and mucous membranes, and sulfur dioxide (SO2), another toxic and irritant gas.
Therefore, the provision and consistent use of adequate ventilation systems, including highly effective local exhaust ventilation (LEV) strategically positioned at points of dust and fume generation on processing machinery, is absolutely paramount. Workplace exposure limits (WELs) or permissible exposure limits (PELs) for these specific gases, as well as for any other volatile compounding ingredients, must be diligently monitored and strictly observed to ensure they remain below legally mandated or recommended occupational health thresholds.
Direct skin contact with uncured CSPE and its associated compounding ingredients should always be minimized or, ideally, entirely avoided. Standard personal protective equipment (PPE) typically includes the use of chemical-resistant gloves (e.g., made from nitrile, neoprene, or butyl rubber, selected based on the specific chemicals being handled), long-sleeved protective clothing to cover exposed skin, and appropriate eye protection, such as safety glasses with side shields or, in situations with a higher risk of splashing, chemical splash goggles or even a full-face shield.
If airborne dust concentrations are significant or if fume levels cannot be adequately controlled below exposure limits through engineering controls like ventilation, then appropriate respiratory protection becomes necessary. This might range from NIOSH-approved disposable particulate respirators (e.g., N95 or P100) to more robust air-purifying respirators equipped with suitable cartridges for organic vapors and acid gases, or even supplied-air respirators in highly contaminated environments.
Crucially, Material Safety Data Sheets (MSDS) or, more currently, Safety Data Sheets (SDS) for the specific CSPE grade being used and for all compounding ingredients must be readily available to all personnel and meticulously consulted before any handling or processing begins.
These documents provide detailed, invaluable information on potential hazards, specific handling precautions, emergency first-aid measures, firefighting procedures, and explicit PPE recommendations. Comprehensive training for all personnel on these hazards, safe handling procedures, emergency response, and the correct use and maintenance of PPE is not just recommended but essential for a safe working environment.
Good housekeeping practices, such as the prompt cleanup of any spills and the regular removal of accumulated dust from surfaces and equipment, also play a vital role in minimizing potential exposure risks. Furthermore, easily accessible emergency eyewash stations and safety showers should be strategically located in all areas where CSPE is handled and processed, allowing for immediate decontamination in case of accidental exposure.
Insights into disposal methods, recyclability challenges and possibilities, and its overall environmental footprint
The end-of-life management of products made from Chlorosulfonated Polyethylene presents certain distinct environmental considerations that require careful attention.
What becomes of CSPE products once they have fulfilled their service life? Owing to its robust, cross-linked (thermoset) nature once vulcanized, and its significant chlorine content, CSPE is not readily biodegradable in landfills and poses considerable challenges for conventional mechanical recycling methods.
Mechanical recycling, which typically involves grinding down the waste material and then re-melting and re-forming it, is largely ineffective for thermoset elastomers like cured CSPE because, by definition, they do not melt and flow when heated; instead, they will char and decompose. Any attempts at straightforward mechanical recycling of cured CSPE usually result in a significantly downcycled material with vastly inferior physical and mechanical properties, severely limiting its potential for use in anything other than very low-value, non-critical applications.
Incineration in appropriately designed and equipped industrial waste-to-energy facilities is a common and often preferred disposal route for many polymeric wastes, including CSPE. When incinerated under carefully controlled high-temperature conditions in modern industrial incinerators that are outfitted with advanced flue gas treatment systems (e.g., acid gas scrubbers, particulate filters), the considerable energy content of CSPE can be effectively recovered and utilized, contributing to resource efficiency.
However, the chlorine content inherent in CSPE means that hydrogen chloride (HCl) will inevitably be formed as a combustion byproduct. This acidic gas must be efficiently neutralized and removed from the exhaust gases by the scrubbing systems to prevent its release into the atmosphere, where it could contribute to acid rain and air pollution.
Similarly, the sulfur content in CSPE will lead to the formation of sulfur dioxide (SO2), another acid gas that requires similar abatement. Uncontrolled burning of CSPE (e.g., in open fires) or its indiscriminate landfilling is highly undesirable from an environmental perspective. Landfilling contributes to the growing problem of plastic waste accumulation, and while CSPE itself is relatively inert and stable in a landfill environment, there could be very long-term concerns about the potential leaching of additives or degradation products, although generally, these concerns are less pronounced for CSPE than for some other plastics that contain more mobile or leachable plasticizers.
Are there any emerging, greener alternatives on the horizon? Research into advanced recycling technologies, such as pyrolysis (thermal decomposition in the absence of oxygen to produce oils or gases) or chemical recycling (solvolysis or other chemical processes to break the polymer down into its constituent monomers or other valuable chemical feedstocks), might offer potential future pathways for more sustainable end-of-life management of CSPE. These methods could theoretically recover more value from the waste material than simple incineration.
However, these advanced technologies are generally not yet commercially widespread, economically viable, or specifically optimized for CSPE on a large scale. The overall environmental footprint of CSPE also encompasses its manufacturing phase, which, as discussed, can involve the use of chlorinated solvents (in some older or less optimized processes) and energy-intensive chemical reactions.
Continuous efforts by conscientious manufacturers to reduce or eliminate solvent use, improve energy efficiency in production, and minimize emissions are essential for lowering CSPE’s environmental impact.
DXD Group adopts an advanced process that avoids using chlorinated solvents entirely, addressing the ozone-depleting emissions common in traditional CSM production. This green technology not only reduces energy consumption and production costs but also ensures the final product is free from carcinogenic chlorinated compounds—protecting both the environment and worker health. For end-users and specifiers, selecting CSPE only when its superior properties are truly needed, designing for long life, and considering take-back or refurbishment options all help support more sustainable use.
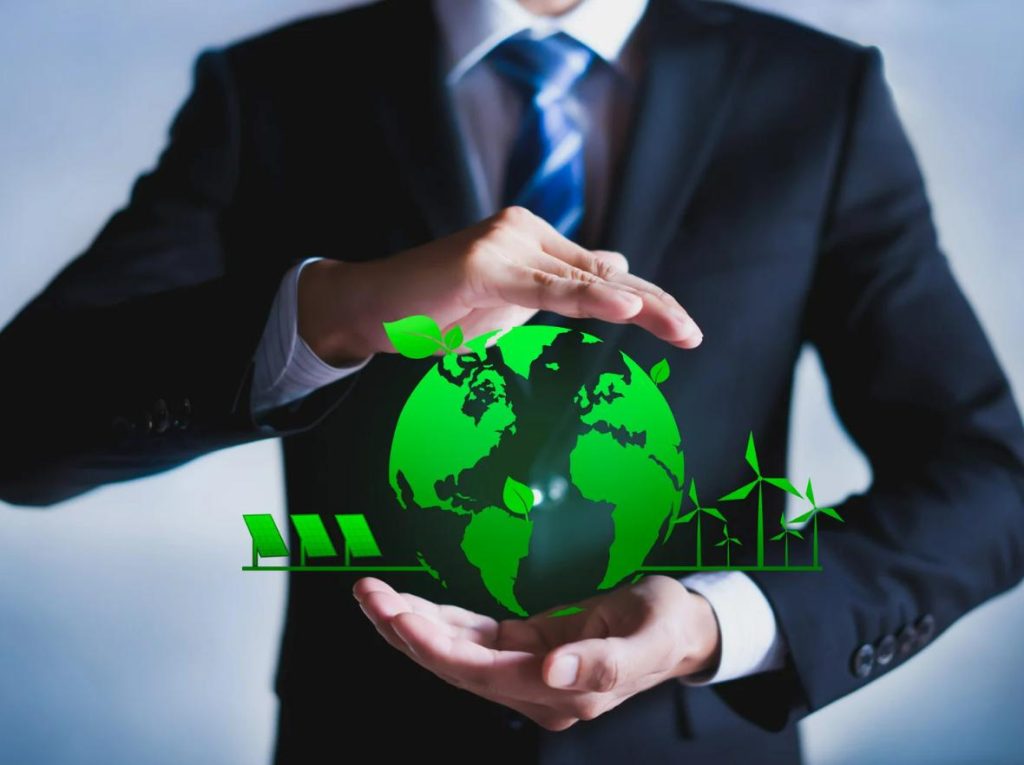
Given the current technological landscape, the focus for CSPE end-of-life management leans more towards responsible disposal via controlled incineration with efficient energy recovery and thorough flue gas cleaning, rather than extensive material recycling in the traditional sense.
The ongoing development of more inherently sustainable elastomers with comparable performance profiles and the advancement of more effective and economical recycling technologies remain significant challenges and important goals for the broader polymer and rubber industry.
Safety & Environmental Aspect | Considerations for Chlorosulfonated Polyethylene (CSPE) |
---|---|
Workplace Handling (Uncured) | Potential for residual solvent/monomer exposure (inhalation, skin). Use in well-ventilated areas. Strict adherence to SDS recommendations. Avoid dust generation. |
Processing Hazards | Thermal decomposition above recommended temperatures can release HCl, SO2 (toxic, corrosive gases). Requires effective local exhaust ventilation (LEV). Monitor airborne contaminant levels. |
Required PPE | Chemical-resistant gloves, eye protection (goggles/face shield), long-sleeved clothing. Respiratory protection (e.g., N95/P100, acid gas/organic vapor cartridges) if ventilation is insufficient. |
Decomposition Products | Hydrogen Chloride (HCl), Sulfur Dioxide (SO2), carbon monoxide, other organic compounds upon overheating or combustion. |
End-of-Life: Biodegradation | Not readily biodegradable due to its stable, cross-linked structure. Persists in landfills. |
End-of-Life: Recycling | Mechanical recycling of cured CSPE is very difficult and results in low-value material. Chemical recycling/pyrolysis is largely developmental, not widely commercialized for CSPE. |
End-of-Life: Incineration | Preferred option if done in controlled industrial incinerators with energy recovery. Requires advanced flue gas scrubbing systems to neutralize HCl and SO2 emissions. |
Manufacturing Footprint | Can involve chlorinated solvents (older processes) and is energy-intensive. Modern processes aim to reduce solvent use and improve energy efficiency. |
Sustainability Strategy | Design for durability and long service life. Use only when its specific high-performance properties are essential. Promote responsible disposal. Support research into greener alternatives/recycling. |
FAQ Section
Q1: What is the most common trade name previously associated with Chlorosulfonated Polyethylene?
The most common and widely recognized trade name previously associated with Chlorosulfonated Polyethylene was Hypalon®.
This was a registered trademark of DuPont, who pioneered its development and commercialization. DuPont ceased the production of Hypalon® in 2010, but generic CSPE materials with similar properties continue to be manufactured and supplied by other chemical companies globally under different trade names or as generic CSPE.
Q2: How does Chlorosulfonated Polyethylene perform in terms of oil and chemical resistance?
Chlorosulfonated Polyethylene (CSM) offers strong chemical resistance, especially to acids, alkalis, mineral oils, and oxidizers. However, it swells in aromatic hydrocarbons and chlorinated solvents. Overall, it outperforms general-purpose rubbers like NR, SBR, and often EPDM in oil resistance.
Q3: Is CSPE a suitable material for long-term outdoor applications, and why?
Yes, CSPE is ideal for long-term outdoor use. Its saturated polymer structure resists UV, ozone, moisture, and weathering, helping it stay flexible and durable for decades in applications like roofing, cables, and coatings.
Q4: Considering DuPont ceased its production, is Hypalon or equivalent CSPE material still available on the market?
Although DuPont stopped producing Hypalon® in 2010, CSPE is still widely available. Manufacturers like DXD Group offer high-quality CSPE with similar performance, making it a reliable option for both old and new applications.