1. What is CSM Material?
CSM material stands for Chlorosulfonated Polyethylene. It’s a synthetic rubber known for its exceptional resistance to chemicals, ozone, UV light, and extreme weather. CSM is not just any polymer—it’s the backbone of many industrial-grade products that demand long-term durability in harsh environments.
But here’s the kicker… CSM isn’t well-known outside industrial circles, yet it powers some of the toughest coatings, hoses, and cable jackets on the market. Originally commercialized under DuPont’s Hypalon brand, CSM has since gained global production and demand under various trade names after DuPont’s exit in 2010.
The name itself is a direct description of the material: polyethylene modified through chlorosulfonation. This chemical process introduces both chlorine and sulfonyl chloride groups into the polymer chain, giving it its defining properties.
It’s worth noting that CSM is categorized under specialty elastomers, and its applications span across infrastructure, automotive, marine, aerospace, and electrical industries. You’ll find it in places where rubber failure simply isn’t an option.
Feature | CSM Material Description |
---|---|
Chemical Composition | Chlorosulfonated Polyethylene |
Structure Modification | Chlorination and sulfonation of PE |
Physical State | Solid, usually in pellet or sheet form |
Common Trade Names | Hypalon (discontinued), other generics |
Standard Color | Natural white, black, or colored blends |
So, why should B2B buyers care? If your application needs something tougher than EPDM or cheaper than fluororubber, CSM may be your ideal middle ground.
2. How is CSM Made?
You might be wondering—how does CSM actually come to life? It all starts with polyethylene, one of the most basic polymers on earth. However, what happens next transforms it into a high-performance material suited for corrosive and outdoor conditions.
The core manufacturing process is known as chlorosulfonation. This involves bubbling chlorine (Cl₂) and sulfur dioxide (SO₂) gases through a solution of polyethylene dissolved in a hydrocarbon solvent. Under ultraviolet light or heat, the gases react with the polymer chain. The result? Polyethylene now contains reactive sites that give it both polarity and improved thermal behavior.
This is where it gets interesting… The balance between chlorine and sulfonic acid groups in the molecule determines how the rubber behaves. More sulfonic groups mean better crosslinking and adhesion to other surfaces. However, too much can make the material stiff and hard to process.
Here’s a simplified breakdown of the process:
Stage | Operation Description |
---|---|
Base Resin Input | High-density polyethylene pellets |
Solvent Dissolution | Dissolved in hexane or cyclohexane |
Gas Injection | Cl₂ and SO₂ injected with agitation |
Reaction Initiation | UV light or thermal energy starts the reaction |
Polymer Recovery | Neutralized, precipitated, filtered, and dried |
Final Stabilization | Add antioxidants and process aids |
Large manufacturers may also blend stabilizers, carbon black, and processing oils to make the material easier to handle. The final product is usually shipped in bales or slabs and must be stored in cool, dry areas to prevent premature crosslinking.
One thing’s clear: CSM is not a backyard polymer. It requires sophisticated handling, chemical expertise, and quality control protocols from start to finish.
3. What Are the Core Properties of CSM?
Let’s cut to the chase. Why would an engineer, formulator, or buyer choose CSM over other elastomers? The answer lies in its remarkable balance of properties.
CSM rubber provides:
- Outstanding resistance to ozone and UV radiation
- Strong resistance to acids, alkalis, oils, and oxidizing agents
- Stable mechanical properties across a wide temperature range (-40°C to +120°C)
- Long aging resistance under outdoor exposure
- Moderate flame retardance
But wait, there’s more… CSM also offers good abrasion resistance and gas impermeability. It does not shrink or crack under stress, which makes it ideal for sealing and insulating applications.
Property | Performance Level | Notes |
---|---|---|
UV/Ozone Resistance | Excellent | Outlasts EPDM and NBR |
Chemical Resistance | Very good | Resists acids, bases, oils |
Flame Retardance | Moderate | Can be improved with additives |
Tensile Strength | 10–20 MPa | Depends on compounding |
Elongation at Break | 250–400% | Highly flexible |
CSM can also be peroxide-cured or sulfur-cured, depending on the application. Peroxide curing delivers better thermal resistance and mechanical stability, while sulfur systems offer ease and lower cost.
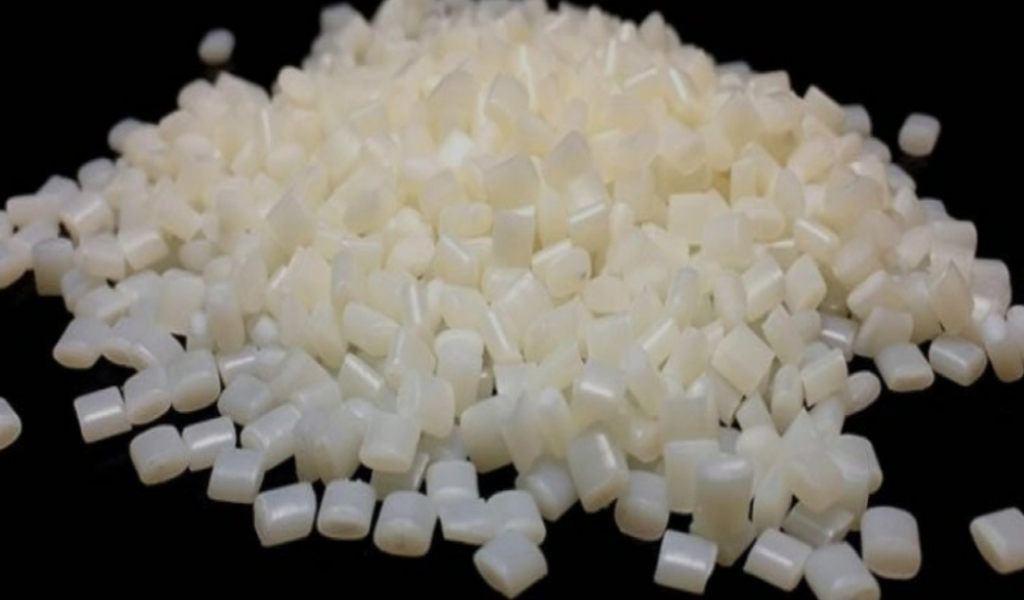
4. What Makes CSM Different from Other Rubber Types?
So what sets CSM apart in a crowded rubber market? Let’s not sugarcoat it—there are dozens of elastomers in commercial use. EPDM, CR (neoprene), CPE, NBR, and even natural rubber each have specific strengths. But CSM manages to carve out a niche due to its rare combination of UV, ozone, and chemical resistance, with reasonably good mechanical performance.
Unlike EPDM, CSM resists oils and solvents. Unlike neoprene, it maintains flexibility at low temperatures without stiffening. Compared to CPE, it cross-links better and exhibits more consistent heat aging. NBR might resist oils better, but it fails quickly under sunlight or ozone. And let’s not even mention natural rubber—it breaks down in just months under UV.
What’s the real story? CSM bridges the gap between cheap commodity rubbers and high-end fluoroelastomers. It gives you more performance than basic rubbers without the price tag of FKM or silicone.
Here’s how it stacks up:
Feature | CSM | EPDM | CR | CPE | NBR |
---|---|---|---|---|---|
UV Resistance | Excellent | Good | Moderate | Good | Poor |
Oil Resistance | Good | Poor | Good | Moderate | Excellent |
Flame Retardance | Moderate | Poor | Good | Moderate | Poor |
Heat Aging Stability | Strong | Moderate | Strong | Strong | Weak |
Price Level | Mid | Low | Mid | Mid | Low |
That blend of resistance traits gives CSM its edge in weatherable coatings, high-end hoses, cable sheathing, and industrial linings. For buyers needing balance, CSM outshines many of its rivals without busting the budget.
5. What Are the Common Grades of CSM?
Here’s where things get specific. CSM isn’t sold as one-size-fits-all. Depending on its chlorine content (usually between 27–45%) and molecular weight, manufacturers create different grades for various processes and applications.
Some grades are better suited for extrusion, while others are designed for compression or injection molding. The physical form also varies—some come in dense pellets, others in sticky slabs or even powdered form.
But don’t get overwhelmed. Manufacturers usually categorize grades by hardness, viscosity, and chlorine content. A higher chlorine level gives better flame retardance and chemical resistance but can reduce flexibility.
Common CSM grade characteristics:
Grade Type | Chlorine % | Mooney Viscosity | Application Focus |
---|---|---|---|
Soft CSM | 27–30% | Low | Seals, linings |
Medium CSM | 32–36% | Medium | Cable jackets, sheets |
Hard CSM | 38–45% | High | Gaskets, rollers |
Ready for the good part? Some suppliers offer pre-compounded grades with additives, which save time during processing. These versions might include stabilizers, plasticizers, pigments, or anti-aging agents, simplifying work for manufacturers.
Choosing the right grade can make or break your production efficiency. For example, if you’re extruding long tubes or cables, you’ll want something with consistent melt flow and low gel count. Molding applications? Go for a tighter cure curve and high elongation values.
6. What Are the Industrial Applications of CSM?
Still unsure where CSM shows up in the real world? Let’s map it out. CSM might not be flashy, but its presence in industrial manufacturing is massive. Engineers turn to it when weather, heat, chemicals, and UV are constant threats.
Top use cases include:
- Cable sheathing: Especially in mining, shipbuilding, and outdoor applications
- Chemical tank linings: Where acidic or alkaline liquids are stored
- Roof membranes: High-end construction projects with long service requirements
- Automotive hoses: Fuel hoses, brake lines, and coolant ducts
- Printing rollers: Inking and transfer rollers in high-speed presses
- Oil-resistant gaskets and seals
But here’s the kicker… In some cases, CSM outperforms even silicone or fluororubber in real-world durability. Sure, it might not handle 300°C, but over a decade under UV or corrosive gas? It won’t blink.
Let’s break down some high-demand sectors:
Industry | CSM Use Case | Advantage |
---|---|---|
Energy | Cable jackets in substations | Electrical insulation + UV stability |
Water treatment | Pump housings and linings | Corrosion resistance |
Automotive | Brake hoses, seals | Heat and oil tolerance |
Construction | Roof membranes | Long weathering performance |
Chemical processing | Tank linings, hoses | Acid and base resistance |
If your end-use environment chews through normal rubber, chances are CSM is your answer.
7. Why Do Engineers Choose CSM for Harsh Environments?
Let’s face it—nature isn’t kind to rubber. Harsh weather, salty air, acidic vapors, and UV rays destroy standard materials fast. That’s exactly where CSM shines.
With excellent resistance to acids, alkalis, ozone, and oxygen, CSM stays intact in places that make other rubbers crack and crumble. It holds its shape even after extended heat exposure. That’s why engineers use it in infrastructure exposed to chemical fumes, desert climates, or marine spray.
What’s the real story? In long-term studies, CSM retained over 80% of its tensile strength after 1,000 hours of ozone exposure. Meanwhile, natural rubber and even EPDM degraded by more than half.
Performance snapshot:
Harsh Environment | Problem with Other Rubbers | CSM Advantage |
---|---|---|
Acidic surroundings | Swelling, breakdown | Stable under pH 2–12 |
Constant UV exposure | Cracking, chalking | 10+ years without degradation |
High salinity | Surface corrosion | Resists salt spray and oxidation |
Chemical splash zones | Delamination, blisters | Maintains adhesion and shape |
CSM isn’t just weather-resistant. It’s practically armor for polymers.
8. What Are the Processing Methods for CSM?
You might assume all rubbers process the same—but not quite. CSM has its quirks. While it can be processed using standard rubber equipment, the chlorosulfonation gives it a unique behavior that needs special attention.
Common processing methods include:
- Extrusion: For cables, tubing, and profiles. Requires accurate temperature control to avoid scorch.
- Compression and injection molding: Used for seals, gaskets, and rollers.
- Calendaring and coating: For linings, membranes, and textile lamination.
Ready for the good part? CSM works with both sulfur-based and peroxide-based curing systems. That gives compounders flexibility depending on the final product’s required properties. Peroxide cures yield better heat aging and compression set resistance, while sulfur systems are faster and cheaper.
Here’s a table comparing cure systems:
Cure System | Advantages | Disadvantages |
---|---|---|
Sulfur-based | Fast vulcanization, lower cost | Less thermal stability |
Peroxide-based | Better heat aging, cleaner | More expensive, needs precise control |
Fillers, softeners, and stabilizers can be added easily. Carbon black enhances UV and abrasion resistance. Plasticizers improve low-temp flexibility. But CSM is sensitive to scorch—meaning it can start curing early if overheated—so close process monitoring is crucial.
Operators must also keep moisture out. Water can hydrolyze the sulfonyl chloride groups, impacting the cure and long-term strength.
If you’ve got proper mixing equipment, accurate temperature control, and curing discipline, CSM rewards you with consistent, long-life parts that hold up where others can’t.
9. Can CSM Be Blended with Other Materials?
This is where blending gets strategic. Not all applications call for 100% CSM content. To balance cost, processability, and specific performance traits, CSM can be blended with compatible rubbers like CR (neoprene), EPDM, or CPE.
But here’s the kicker… Not every blend behaves nicely. For a successful CSM hybrid, the companion polymer must share similar cure chemistry or polarity. CR is a popular partner—it helps improve adhesion and lower compound costs while retaining decent chemical resistance. EPDM can reduce cost and boost flexibility, but it might reduce chemical durability.
Blending matrix:
Blend Partner | Reason for Blending | Typical Use Case |
---|---|---|
CR | Reduce cost, enhance bond | Adhesives, belts |
EPDM | Improve flexibility | Roofing sheets, profiles |
CPE | Extend chemical resistance | Cable jackets, linings |
The result is a compromise—higher CSM content gives more durability, while blends offer easier processing and lower costs. In high-performance environments, pure CSM or high-ratio blends are preferred.
Processing wise, blends behave similarly to CSM alone but may need adjustments in cure time or filler ratios. Watch for compatibility gaps—some blends may phase-separate or show poor aging if not properly mixed.
CSM blends can make the material accessible to more buyers, especially in price-sensitive projects with mild performance requirements.
10. What Are the Storage and Handling Guidelines for CSM?
Think rubber is low maintenance? Think again. Storing CSM wrong can ruin it before it ever enters your mixer. That’s why suppliers and buyers need strict protocols.
CSM must be:
- Kept away from direct sunlight
- Stored at 5–25°C (preferably air-conditioned)
- Protected from moisture and solvents
- Handled using gloves and non-metal tools
What’s the real story? CSM contains active chlorine and sulfonyl groups, which can prematurely react if exposed to high humidity or acids. Aging also causes changes in viscosity and color.
Shelf life depends on the grade and packaging. In sealed foil bags, it may last up to 24 months. Open storage or plastic wrap? Expect significant degradation in 6–8 months.
Risk Factor | Impact on CSM Quality | Preventive Action |
---|---|---|
High humidity | Hydrolysis, crosslinking | Use sealed moisture-proof bags |
Direct sunlight | Oxidation, hardening | Store in dark containers |
Contact with oils | Surface softening | Avoid contamination |
Also worth noting: CSM slabs can block or stick together under pressure. Use waxed sheets between layers if stacking.
Every responsible warehouse should treat CSM like a temperature-sensitive material. It might not spoil like milk, but bad storage costs you batches, time, and trust.
11. How Does CSM Perform in Electrical Applications?
Let’s talk voltage. CSM’s role in the electrical sector is more significant than many realize. It’s a go-to jacket material for power cables, control wiring, and signal cables, especially in outdoor and industrial environments.
But why does it work so well? CSM is flame retardant, flexible in the cold, UV resistant, and impervious to water and chemicals. These traits are vital for cabling exposed to sun, oil, salt, and abrasion.
Performance markers:
Property | CSM Value |
---|---|
Dielectric Strength | > 15 kV/mm |
Flammability Rating | Self-extinguishing |
Volume Resistivity | ≥ 10¹⁴ ohm·cm |
Weathering Performance | 10+ years outdoor exposure |
Here’s something you didn’t expect. Many CSM cable jackets outperform PVC in real-world tests—especially when installed in harsh climates like oil rigs, ships, and mining zones.
In some cases, flame resistance can be further enhanced by adding aluminum hydroxide or antimony oxide. These additives, while raising cost slightly, improve safety ratings to meet UL or IEC standards.
For engineers, CSM’s electrical traits offer one less thing to worry about during long-term field deployments.
12. What Are the Limitations of Using CSM?
Let’s not pretend it’s perfect. CSM, while versatile, has a few drawbacks worth noting before you commit to bulk purchases or long-term contracts.
Common concerns:
- Price: CSM is more expensive than EPDM or CR.
- Processing complexity: It has tight cure windows and scorch sensitivity.
- Limited low-temperature elasticity: Below -40°C, performance can decline.
- Difficult to recycle: Crosslinked CSM cannot be remelted or reshaped.
Limitation | Impact | Workaround |
---|---|---|
High cost | Budget pressure | Use in blends or thin coatings |
Cure control sensitivity | Rejects, quality variation | Automated mixing + precise cure |
Rigidity in cold | Cracking in artic zones | Add plasticizer or blend w/ EPDM |
Incompatibility | Difficult cross-blending | Use single-rubber formulations |
But here’s the kicker… These aren’t showstoppers. Most of CSM’s issues are manageable through formulation, equipment calibration, and grade selection. As long as buyers are aware and plan properly, CSM pays back in durability and reduced replacement frequency.
13. How to Select the Right CSM Grade for Your Project?
Here’s the deal—choosing the wrong grade will cost you. Whether you’re coating a chemical tank or insulating a cable, the CSM you pick must match your application, process, and environment. That’s why selection is more than just grabbing whatever’s cheapest from the catalog.
To get it right, you need to ask:
- What chemicals or stresses will the material face?
- What’s the expected lifespan of the end product?
- Is it being molded, extruded, or calendered?
- How much flexibility is required?
This is where it gets interesting… Most buyers look at chlorine content, Mooney viscosity, and cure system compatibility. Lower chlorine levels give more flexibility but reduce flame retardance. Higher chlorine means better resistance to solvents and acids.
Here’s a quick selector table:
Need | Recommended Grade Type | Reason |
---|---|---|
Outdoor weathering | Mid-chlorine, UV-stable | Balanced resistance and processability |
Chemical exposure | High-chlorine, peroxide-cure | Maximum chemical durability |
Cold flexibility | Low-chlorine, sulfur-cure | Better at sub-zero temps |
Low smoke, flame retardant | High-chlorine + additives | Meets cable fire safety codes |
Work with your technical team or supplier to get test sheets and trial samples. Ask for compounding suggestions too—many CSM materials need reinforcing fillers or specific cure packages.
What’s the real story? The difference between a successful product and a failed one often lies in the 5% of ingredients you didn’t think about. Grade matching is the cheapest insurance against rejection, failure, or costly returns.
14. What Should You Know Before Importing CSM from China?
Thinking of buying from China? You’re not alone. Most global CSM comes from Chinese manufacturers—and for good reason. Their cost structure, production volume, and compound customization options are unmatched.
But here’s what smart buyers do first… Vet the supplier. Ask for:
- Product data sheets
- References from clients in similar industries
- Sample orders before placing large POs
Shipping also plays a big role. CSM must be packed in airtight bags, boxed to avoid pressure, and shipped in climate-safe containers. Some grades may require palletized wooden crates or custom labeling for customs compliance.
FAQ
- Q1: What is CSM material?
CSM stands for Chlorosulfonated Polyethylene, a high-performance synthetic rubber used in outdoor, chemical, and electrical applications. - Q2: How is CSM made?
It’s created by chemically modifying polyethylene with chlorine and sulfur dioxide under UV or heat, forming a tough, flexible polymer. - Q3: What are the benefits of CSM in cable insulation?
CSM provides UV, flame, and chemical resistance, making it ideal for protecting cables in exposed and hazardous environments. - Q4: Can CSM be recycled or reused?
CSM is thermoset and cannot be re-melted, but offcuts and waste may be ground for use in low-spec applications. - Q5: How does CSM compare with EPDM or CR?
It resists chemicals and UV better than both, offers longer service life, and performs well in harsh industrial conditions.