CSM rubber, or chlorosulfonated polyethylene, is a high-performance synthetic rubber known for its excellent resistance to UV, ozone, heat, and chemicals. It maintains flexibility across extreme temperatures and offers long-term durability in harsh environments. Common applications include cable sheathing, automotive hoses, roofing membranes, and chemical-resistant linings, making it ideal for industries that demand weatherproof, flame-retardant, and corrosion-resistant materials.
1. What Is CSM Rubber and Where Did It Originate?
CSM rubber, short for chlorosulfonated polyethylene rubber, has built a quiet reputation across industries where durability and chemical resistance are non-negotiable. If you’ve ever wondered what kind of material survives decades under sunlight, acid rain, or corrosive fumes—this is it. CSM isn’t just another synthetic rubber. It’s built to last, engineered to resist.
But here’s the kicker… CSM was originally developed by DuPont under the trade name Hypalon. It was designed for extreme environments—outdoors, underwater, or anywhere traditional rubbers would fail. Hypalon remained the industry benchmark until DuPont discontinued it in 2009. Since then, several Asian and European manufacturers have filled the supply gap with equivalent grades of CSM rubber, maintaining global availability without compromising quality.
Chemically speaking, CSM is created by reacting polyethylene with chlorine and sulfur dioxide gas. The result is a rubber that inherits polyethylene’s flexibility and gains added resistance through chlorination and sulfonation. These added components give CSM its strength, flame resistance, and outstanding weatherability.
Historically, CSM was heavily adopted in military-grade fuel tanks, industrial roofing membranes, and automotive cable sheathing. Its fame came from performing in the worst conditions—corrosive chemical plants, marine dockyards, and high-voltage applications. Even now, after more than 60 years of use, few materials can claim the same stability and lifespan.
Today, CSM rubber is produced mostly in China, Japan, and parts of Europe. Its role in cable insulation, protective coatings, and industrial linings remains steady. Though it’s no longer called Hypalon, the core chemistry hasn’t changed, and neither has its unmatched performance in aggressive environments.
Origin | Historical Milestone | Modern Equivalent |
---|---|---|
DuPont (USA) | Released Hypalon in the 1950s | Discontinued 2009 |
Global Markets | Adopted in automotive, marine, roofing | CSM fills the gap |
China, EU | Active CSM production since 2010 | Many active brands |
2. What Chemicals Make Up CSM Rubber?
CSM’s secret lies in its molecular backbone. It’s not a random mix of industrial waste—it’s a purpose-built molecule tailored for punishment. Most rubbers struggle against time, UV, or acid. Not CSM. Its formula is like armor for elastomers.
Here’s where it gets interesting… The production starts with polyethylene—a polymer used in common packaging and plastic sheets. Polyethylene alone is soft and chemically reactive. To convert it into CSM, manufacturers expose it to chlorine and sulfur dioxide gas under controlled heat and pressure. This reaction adds chlorine atoms and sulfonyl chloride groups to the chain. These two elements are what make CSM rubber resilient.
Chlorine atoms create a tighter, stronger polymer that resists oil, fuel, ozone, and acid. The sulfonyl groups act like hooks for crosslinking during vulcanization, which adds elasticity and thermal stability. Unlike other synthetic rubbers that soften under heat, CSM keeps its shape.
The amount of chlorine in CSM typically ranges from 20% to 45%. Higher chlorine content results in greater flame resistance but slightly less flexibility. Manufacturers adjust this ratio depending on the application—roofing sheets need softness, while fuel hose linings demand flameproof toughness.
Some formulas may include:
- Carbon black (for UV resistance)
- Plasticizers (for flexibility)
- Peroxide crosslinkers (for strength)
Component | Function in CSM | Typical Range |
---|---|---|
Chlorine | Chemical resistance, flame proof | 20%–45% |
Sulfonyl chloride | Crosslinking ability | 1%–2% |
Polyethylene base | Flexibility, chemical skeleton | Core polymer |
These chemical tweaks make CSM one of the most stable elastomers on the market. Whether it’s acid in a pipe or sunlight on a rooftop, CSM rubber shrugs it off.
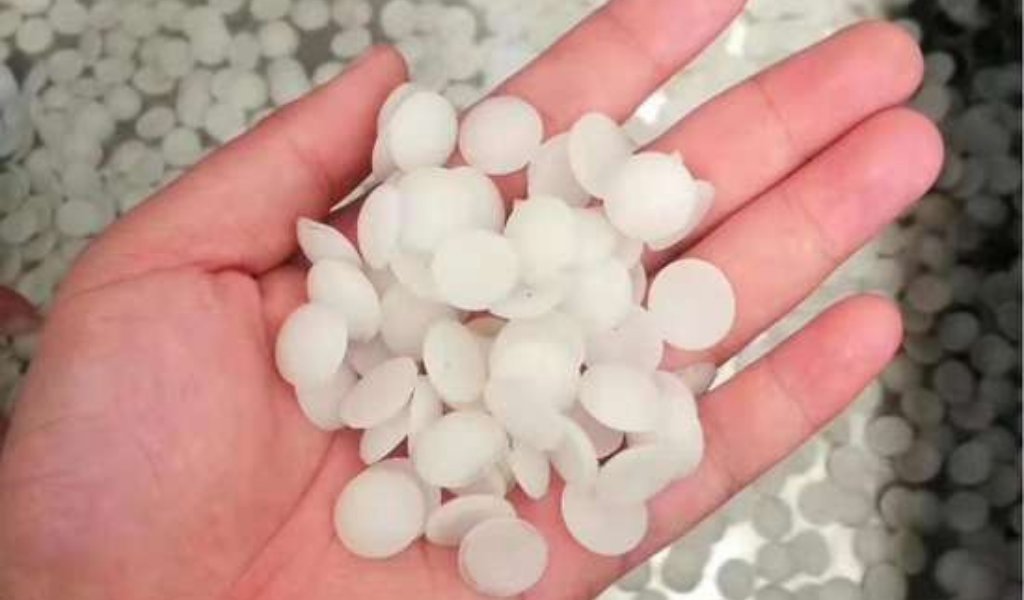
3. How Is CSM Rubber Manufactured?
CSM manufacturing isn’t casual work. You’re not just blending powders in a tub—you’re dealing with gases, reactions, and precision chemistry. Even a slight deviation in temperature or timing can ruin an entire batch.
Ready for the good part? The core process involves chlorosulfonation—a chemical transformation that alters the molecular structure of polyethylene. Here’s how it goes:
- Polyethylene flakes or powder are dissolved in an inert solvent such as carbon tetrachloride or hexane.
- The solution is transferred to a sealed reactor.
- Chlorine and sulfur dioxide gas are injected under pressure while the solution is stirred.
- A controlled light or heat source triggers the reaction, bonding chlorine and sulfonyl chloride groups to the polymer chain.
- The modified polymer is neutralized, precipitated, washed, and dried.
The end product is usually a white or gray rubbery mass. It’s then pelletized, bagged, and sold to compounders and converters for downstream processing.
Safety during this stage is critical. Chlorine and SO₂ are both hazardous gases, so the equipment must include gas scrubbers, ventilators, and sealed reaction vessels. Only facilities with strong environmental and process controls can safely and efficiently manufacture CSM.
Stage | Purpose | Notes |
---|---|---|
Dissolution | PE is softened for reaction | Solvent selection is key |
Gas chlorosulfonation | Modify polymer with Cl and SO₂ | Requires UV or heat catalyst |
Neutralization | Remove residual acid and impurities | Prevents material breakdown |
Drying | Final product formed | Moisture must be eliminated |
While other rubbers like EPDM are extruded from simple blending, CSM requires real chemistry. That’s part of what gives it the performance edge. It’s built from molecules up.
4. What Are the Physical Properties of CSM Rubber?
CSM isn’t just chemically stable—it’s tough. In fact, the physical properties of CSM rubber make it stand out in a world where materials constantly crack, tear, or shrink. What makes it so durable? Let’s dive into the numbers.
Here’s the real story… When engineers talk about physical properties, they care about metrics like tensile strength, elongation, hardness, and aging resistance. CSM scores well across all of them.
Let’s break them down:
- Tensile Strength
CSM can withstand 7–14 MPa of tensile force before breaking. That’s more than enough for most industrial hose, cable, and membrane applications. It holds together under mechanical load, even in thin layers. - Elongation at Break
One of CSM’s underrated qualities is its elasticity. It stretches 300%–500% before snapping, depending on the compound. This is critical for gaskets, seals, and flexible couplings that move under stress. - Hardness (Shore A)
CSM compounds range from 50 to 90 Shore A in hardness. That’s a wide range to suit everything from soft sealing strips to rigid protective layers. - Weather Aging Resistance
Here’s where CSM earns its reputation. It resists embrittlement under sunlight, ozone, and salt fog. Even after 1,000 hours of UV exposure in accelerated aging chambers, CSM barely changes. - Tear and Abrasion Resistance
CSM holds its shape under mechanical stress. It doesn’t tear like some cheaper rubbers, especially when cross-linked properly. - Flex Resistance
In repeated bending or twisting applications—like cable jacketing—CSM doesn’t crack, even after years.
Property | Typical Value Range | Significance |
---|---|---|
Tensile Strength | 7–14 MPa | Withstands mechanical tension |
Elongation at Break | 300%–500% | Absorbs mechanical stress |
Hardness (Shore A) | 50–90 | Tunable for soft or rigid needs |
UV/Ozone Resistance | Excellent | Long life in outdoor conditions |
Tear Resistance | High | Doesn’t split under stress |
But here’s the kicker… Unlike materials that achieve one great metric but fail in others, CSM balances strength and flexibility. That’s what makes it so versatile. It won’t sag in heat or crack in the cold. It doesn’t dissolve in solvents or crumble under pressure.
If you’re making products that need to hold up across seasons, under stress, and around chemicals—this is a material you can trust.
5. What Are the Chemical Properties of CSM Rubber?
Not every rubber can sit in acid and come out smiling. But CSM can. It’s not just flexible or UV-proof—it’s chemically armored. Whether you’re talking sulfuric acid, motor oil, or salt spray, CSM stands up without flinching.
You might be wondering how that works. The chemical resistance of CSM comes from the chlorine and sulfonyl chloride groups bonded directly to its backbone. These make the rubber non-reactive to most corrosive agents.
Let’s look at some performance benchmarks:
- Acid Resistance
CSM survives exposure to nitric, sulfuric, and hydrochloric acid. This makes it ideal for use in chemical tank linings and protective gloves in acid-handling operations. - Alkali Resistance
CSM doesn’t break down in caustic soda or ammonia environments. Many rubbers would degrade, but CSM doesn’t absorb or swell. - Solvent Resistance
While not entirely solvent-proof, CSM resists many petroleum-based solvents far better than natural rubber or EPDM. It holds up in kerosene, hydraulic fluids, and diesel fumes. - Ozone and Oxidation Resistance
Exposure to ozone cracks many rubbers in a matter of days. CSM can take months—even years—before showing signs of degradation. The reason? Chlorine atoms block oxidative reactions. - Flame Retardance
CSM doesn’t ignite easily. It self-extinguishes when removed from a flame. That’s why it’s used in electrical insulation and aerospace components.
Chemical Agent | CSM Resistance Level | Notes |
---|---|---|
Sulfuric Acid (98%) | Excellent | No cracking after prolonged use |
Sodium Hydroxide (NaOH) | Good | Slight discoloration, no damage |
Diesel/Kerosene | Very Good | Minor swelling only |
UV/Ozone Exposure | Excellent | No surface cracks |
Combustion Resistance | High | Self-extinguishing |
What’s the bottom line? If your application involves chemicals, fuels, sunlight, or extreme atmospheres, CSM provides a long-term defense. You won’t need frequent replacements, patch jobs, or panic repairs.
6. How Does CSM Perform in Extreme Environments?
If you’re designing products that need to survive heatwaves, blizzards, saltwater, or chemical spills, you can’t afford rubber that fails. That’s where CSM steps in. It doesn’t just meet environmental challenges—it thrives in them.
This is where it gets interesting… CSM rubber maintains performance across a temperature range from -40°C to 130°C, with some grades enduring short spikes up to 160°C. Whether installed in scorching rooftop membranes or freezing oil rigs, it keeps its elasticity without cracking or melting.
Its tolerance to weathering is second to none. In accelerated aging tests, CSM-coated products retain 80–90% of their original mechanical strength even after thousands of hours of UV and ozone exposure. Rain, snow, dust storms—none of these elements cause significant damage over years.
Take a closer look at specific environment-related properties:
- Heat Resistance: CSM retains tensile and elongation values even after 168 hours at 120°C.
- Cold Flexibility: It remains pliable at -40°C without brittle fractures.
- Salt and Humidity Tolerance: In marine environments, CSM doesn’t degrade or corrode when in constant contact with salt spray or high humidity.
- Hydrocarbon Fumes: CSM performs well near fuel tanks and refineries where vaporized solvents would ruin other materials.
- Outdoor Exposure: Roofing membranes made from CSM last 20+ years with minimal change in surface or flexibility.
Condition | CSM Result | Usage Example |
---|---|---|
+120°C oven test | No visible deformation | Cable jackets near furnaces |
-40°C flex test | Passed multiple bend cycles | Arctic pipeline gaskets |
5,000h UV exposure | Minimal surface chalking | Roofing sheets |
Salt spray (1000h) | No swelling or delamination | Boat covers, dock seals |
So, what does this mean for your business? Whether your customer installs equipment in South American deserts or Scandinavian cold-storage plants, CSM can adapt. Its performance remains stable without reprocessing or material reinforcement. That kind of reliability saves money—and reputations.
7. How Does CSM Compare to EPDM, CR, and CPE?
Let’s face it—not all synthetic rubbers are created equal. CSM is often compared to materials like EPDM, CR (Chloroprene), and CPE (Chlorinated Polyethylene). Each has pros and cons, but choosing blindly can lead to failure in the field.
What’s the real story? CSM fills a niche for high UV and chemical resistance without sacrificing physical strength. It’s better than EPDM in ozone performance, more flexible than CR at low temperatures, and tougher than CPE in mechanical abuse scenarios.
Here’s how they compare:
Property | CSM | EPDM | CR | CPE |
---|---|---|---|---|
UV/Ozone Resistance | Excellent | Good | Good | Fair |
Chemical Resistance | Very Good | Fair | Good | Moderate |
Heat Resistance (°C) | 130–160 | 120–150 | 100–120 | 100–130 |
Oil/Fuel Resistance | Moderate | Poor | Excellent | Good |
Cost per kg | Mid-High | Low | High | Medium |
Mechanical Flexibility | Very Good | Excellent | Fair | Good |
Flame Retardance | High | Low | Medium | Medium |
But here’s the kicker… EPDM is often cheaper but can’t survive in chemical-rich environments. CR works well in oils but ages poorly in sunlight. CPE tries to balance cost and performance but lags in extreme conditions.
CSM may cost more upfront, but its lifespan and reliability in critical use cases mean fewer complaints, returns, or legal issues. For safety-critical or outdoor industrial goods, it’s often the better long-term bet.
8. What Are the Most Common Applications of CSM Rubber?
CSM isn’t a theoretical material—it’s already working behind the scenes in dozens of industries. You’ve likely seen it without knowing it. Its uses span everything from cable jackets to inflatable boats, and it plays a key role wherever exposure, aging, and performance are non-negotiable.
Here’s the good part… CSM is popular in power cable insulation, roofing membranes, automotive hoses, and chemical containment systems. It’s chosen for these jobs because it handles heat, sunlight, solvents, and pressure without breaking down.
Let’s break it into sectors:
- Power & Electronics: CSM’s high dielectric strength and heat resistance make it perfect for medium- to high-voltage wire sheathing, especially in outdoor installations or near heat sources.
- Automotive: Under-hood hoses, CV boots, fuel-resistant gaskets—all use CSM for its balance between chemical and mechanical durability.
- Construction: CSM roofing sheets outperform EPDM in sunny regions. Sealing strips and membrane linings benefit from its weatherproof nature.
- Marine: CSM-coated fabrics are used in life rafts, boat covers, and inflatable boats because of their saltwater and puncture resistance.
Industry | Product Type | Reason for Choosing CSM |
---|---|---|
Electrical | Wire & Cable Jacket | UV & Flame Resistance |
Auto Parts | Fuel hoses, Engine gaskets | Heat and oil resistance |
Roofing & Waterproofing | Membrane rolls, Corner tapes | UV resistance, long service life |
Chemical Plants | Lining & Sealing Gaskets | Acid and alkali resistance |
Marine & Dock | Inflatable fabrics, bumpers | Saltwater stability |
What does this mean for your product line? If you’re serving infrastructure, energy, or transportation clients, they’ll appreciate the zero-failure reputation CSM carries. It’s not exotic—it’s just smart.
9. What Are the Typical Grades and Technical Specifications?
Choosing the right CSM isn’t just about color or packaging. The material comes in various grades, each with its own physical, chemical, and processing characteristics. Understanding these specs helps ensure you’re not under- or over-engineering your product.
You might be wondering, “Aren’t they all the same?” Not at all. CSM grades are categorized by Mooney viscosity, chlorine content, particle size, and application type.
Common technical parameters include:
- Mooney Viscosity (ML 1+4 at 100°C): Usually ranges from 40 to 90. Lower viscosity means easier processing; higher viscosity gives better mechanical strength.
- Chlorine Content: Between 25%–45%. Higher values improve fire resistance but reduce flexibility.
- Color: Typically off-white or gray. Easily tinted during compounding.
- Physical Form: Pelletized, powdered, or bales depending on supplier and equipment needs.
- Volatile Content: Should be under 1.0% for most applications.
Grade Code | Chlorine (%) | Mooney Viscosity | Best Use Case |
---|---|---|---|
CSM-601 | 25 | 45 | General extrusion |
CSM-703 | 35 | 60 | Wire insulation, roofing |
CSM-805 | 42 | 80 | Chemical resistance sheets |
So what’s the takeaway? Don’t assume one grade fits all. For high-heat cables, go with higher Mooney and chlorine. For flexible parts like gaskets, lower viscosity works better. Ask your supplier for full tech sheets—and test thoroughly.
10. Can CSM Be Blended with Other Rubbers?
Here’s something most buyers overlook—CSM isn’t just great on its own. It also plays well with others. When you blend it with compatible rubbers or additives, you can fine-tune performance without compromising durability.
But here’s the kicker… CSM can be blended with CR (neoprene), NR (natural rubber), EPDM, and certain types of SBR. This gives manufacturers more flexibility to adjust cost, hardness, elongation, and chemical stability based on the final product’s requirements.
Let’s break it down:
- CSM + CR (Chloroprene Rubber)
This blend enhances flame retardancy and oil resistance. It’s commonly used in mining conveyor belts and industrial hoses. - CSM + NR (Natural Rubber)
When softness and rebound are important (like in flexible seals), this combo works well. However, it slightly reduces weather and chemical stability. - CSM + EPDM
Great for roofing and waterproof membranes. EPDM adds low-temperature flexibility, while CSM reinforces aging and UV resistance. - CSM + SBR (Styrene-Butadiene Rubber)
Offers cost savings for low-load applications, like static seals. Not recommended for high-chemical or outdoor use unless protected. - CSM + Plasticizers + Fillers
Additives like paraffinic oil or carbon black help improve processing, modify density, and adjust color or texture.
Blend Composition | Purpose | Trade-Offs |
---|---|---|
CSM + CR | Flame + Oil Resistance | Higher cost |
CSM + NR | Flexibility, rebound | Lower weather resistance |
CSM + EPDM | UV and low-temp performance | Slight reduction in oil resist |
CSM + SBR | Cost reduction for static parts | Not for harsh environments |
CSM + Fillers/Additives | Processability & surface properties | Varies by formula |
So why blend at all? Custom blends allow you to optimize your product based on your customer’s exact requirements—whether they want cost savings, softer texture, or added chemical toughness. It’s how you serve multiple markets with one base polymer.
11. What Processing Methods Work Best for CSM?
You’ve got the right grade of CSM. Now comes the next question—how do you turn it into a product? Processing CSM takes a bit more effort than some other rubbers, but the results are worth it.
Ready for the good part? CSM rubber is versatile enough to be processed through extrusion, molding, calendaring, and coating. The key is managing its reactivity, crosslinking behavior, and compound viscosity.
Here’s a snapshot of popular methods:
- Extrusion
Common for cable sheathing, hose lining, and gasket strips. Use lower viscosity CSM for smoother flow. Pre-heating the compound helps minimize die swell. - Injection Molding
Excellent for complex parts—grommets, seals, boots. Requires peroxide-based or metal oxide vulcanization for optimal results. - Compression Molding
Ideal for medium- to low-volume parts like washers and heavy-duty seals. Slower than injection but simpler to set up. - Calendaring
Used to make continuous sheets, roofing membranes, or rubber-coated fabrics. Proper plasticization is key to avoid edge cracking. - Solution Coating
For fabric coating (boats, tanks), CSM is dissolved in solvent and applied via brush or spray. Requires controlled curing.
Processing Method | Best Use Cases | Notes |
---|---|---|
Extrusion | Hoses, seals, cable jackets | Watch melt temp & pressure |
Injection Molding | Automotive gaskets, boots | Use peroxide or MO cure system |
Compression Molding | Static seals, industrial parts | Long cycle but low setup cost |
Calendaring | Roofing sheets, fabrics | Uniform thickness matters |
Solution Coating | Canvas, boats, protective wear | Solvent safety is critical |
So what’s the trick? Pay close attention to your cure system. CSM works best with peroxide-based or metal oxide crosslinking—sulfur systems don’t bond well due to its chlorine content. Invest in curing control, and you’ll get top-tier results.
12. How Do You Select the Right CSM Grade?
Let’s say your customer asks for CSM. How do you choose from dozens of grades, viscosities, and chlorine levels? Picking the wrong one could mean the product fails before it even ships.
You might be thinking—“Just grab a general-purpose grade, right?” That’s a trap. Instead, you should match grade to usage environment, product geometry, and curing method.
Here’s a checklist to help:
- Application Type
Is it static (gasket) or dynamic (hose)? Exposure to chemicals, UV, or high temperature? - Process Method
Extrusion? Injection molding? Some grades flow better than others. Know your machine limitations. - Chlorine Content
Higher chlorine improves flame resistance, lowers oil absorption, but stiffens the rubber. Choose higher levels for roofing, lower for flexible seals. - Color Needs
If the final product must be tinted or white, ask for low-pigment or white base CSM. - Curing System
Are you using peroxide, metal oxide, or something else? Some grades work poorly with sulfur systems.
Decision Criteria | Recommended Grade | Why |
---|---|---|
Flame Retardant Roofing | CSM 703, high Cl content | Good UV, high heat tolerance |
Electrical Cable Jackets | CSM 805, peroxide-curable | Dielectric strength |
Automotive Hoses | Mid-range viscosity grades | Oil & flex balance |
Marine Fabrics | Soft grade + coating additive | Abrasion + saltwater resistance |
Static Gaskets | Low Mooney, good flow | Simple mold fill |
Still unsure? Test small batches first. Ask your supplier for tech sheets with specific tensile, tear, and aging data. The right grade pays off in product lifespan and user satisfaction.
13. What Are the Challenges When Using CSM?
No material is perfect—not even CSM. While it offers impressive performance, it comes with quirks that need managing. Skip the fine print and you’ll face production headaches.
Here’s the deal… The main challenges when working with CSM include processing stiffness, curing issues, and raw material cost. Let’s unpack each.
- Processing Difficulty
Higher Mooney grades are hard to mix. If under-plasticized, CSM can crack during calendaring or extrusion. Preheating and good kneading solve this. - Curing Complexity
Unlike EPDM or SBR, CSM doesn’t work well with sulfur systems. You need peroxide or metal oxides—and careful control of time and temperature. Otherwise, you’ll get undercured or scorched rubber. - Raw Material Cost
CSM typically costs more than EPDM, NR, or SBR. But you make up for that with longer service life and less product failure in the field. - Dusting in Powder Grades
CSM in powdered form can generate airborne dust during mixing. Use ventilation or switch to granulated forms. - Coloring Limitations
Some CSM grades are slightly grayish. Getting pure white or light-colored final parts may need extra pigment.
Challenge | Mitigation Strategy | Risk If Ignored |
---|---|---|
Tough Mixing | Preheat, plasticize, use open mills | Poor dispersion, surface cracks |
Cure System Sensitivity | Use peroxide, not sulfur | Incomplete bonding |
Higher Raw Material Cost | Sell on performance, not price | Undervalued premium product |
Powder Dusting | Use granules or sealed mixers | Safety, mess |
Light Color Matching | Ask for pigment-friendly grades | Poor visual appearance |
So, what’s the bottom line? CSM isn’t plug-and-play. But once dialed in, it gives results most other rubbers can’t match. If you’re serious about reliability, the learning curve is worth it.
14. Is CSM Environmentally Friendly or Recyclable?
Environmental responsibility is no longer optional. Clients ask. Governments inspect. Markets reward it. So where does CSM fit?
You might assume: “High-performance rubber must be bad for the planet.” Not entirely. CSM has both pros and cons in the green space, and understanding both helps you sell or source smarter.
Let’s start with the negatives:
- Not Easily Recycled
Like many thermoset rubbers, CSM can’t be re-melted or reshaped after vulcanization. Recycling involves grinding into powder and using as filler—which lowers performance. - Chlorine Content
Environmental critics focus on chlorine, fearing dioxin emissions during incineration. However, controlled industrial incineration facilities address this with scrubbers and emission control.
Now the positives:
- Extremely Long Lifespan
CSM lasts 3–5 times longer than NR or SBR. That means fewer replacements, less waste, and lower lifecycle carbon footprint. - No Halogenated Solvents Needed in New Tech
Advanced Chinese manufacturers now use solvent-free CSM production or water-based slurry systems, drastically cutting VOC emissions. - Non-toxic in Use
Once cured, CSM emits no hazardous fumes, leachables, or dust. It’s inert, stable, and non-irritating.
Environmental Factor | CSM Score | Context |
---|---|---|
Recyclability | Low | Same as EPDM or CR |
Lifecycle Duration | High | Long use, fewer disposals |
Emission During Use | None | Safe when fully cured |
Production VOC | Moderate to Low | New solvent-free tech available |
Chlorine Safety | Requires managed disposal | Incinerate responsibly |
So what’s the verdict? CSM isn’t a bio-based miracle, but it’s responsible when used right. It delivers long-term performance, avoids frequent replacement, and increasingly uses cleaner production methods.
15. What Should You Consider When Sourcing CSM from China?
The supplier matters as much as the material. When you buy CSM from China—or any global market—you need to know what to look for.
Here’s what most buyers miss… Not all CSM is equal. Some factories lack proper quality control. Others skip material testing or misrepresent chlorine content. That leads to returned shipments, failed certifications, or worse—product recalls.
Here’s your sourcing checklist:
- Technical Datasheets (TDS)
Always request TDS showing Mooney, chlorine %, tensile, and elongation. If unavailable or vague—walk away. - Batch Consistency
Ask for past test results across multiple production lots. Fluctuation in color, viscosity, or curing behavior signals poor controls. - Certifications
Confirm REACH, RoHS, and ISO documentation. If shipping to Europe or North America, these are mandatory. - Lead Time and MOQ
Some smaller plants offer fast delivery but impose large MOQs (Minimum Order Quantities). Be clear on your volume flexibility. - Support After Sale
Good suppliers help with compounding tips, curing guidance, and tech sheets. Great ones help troubleshoot line issues.
Evaluation Point | Why It Matters | Red Flags |
---|---|---|
TDS Available | Confirms basic specs | “We don’t share that info.” |
Batch Control | Reduces production variability | Big property shifts in samples |
Certifications | Legal compliance | Outdated or non-existent docs |
Lead Time + MOQ | Delivery planning | MOQ too high for testing |
Tech Support | Faster time-to-market | No chemist or contact assigned |
So what’s the takeaway? Don’t just chase price. Check documentation, test samples in real production, and build a relationship with the supplier. Good sourcing is strategic, not transactional.
FAQ
- Q1: What is CSM rubber?
CSM rubber stands for chlorosulfonated polyethylene rubber. It’s a type of synthetic elastomer known for its superior resistance to UV, ozone, chemicals, and extreme weather conditions. Originally marketed as Hypalon by DuPont, it is now produced by various manufacturers and widely used in outdoor, electrical, marine, and chemical applications. - Q2: How does CSM resist weathering and UV?
CSM’s structure includes chlorine and sulfonyl groups chemically bonded to a polyethylene backbone. These functional groups protect the material from oxidative degradation caused by UV rays and ozone, preventing cracking, chalking, and brittleness even after prolonged exposure. - Q3: Can CSM be used in high-voltage cable sheathing?
Yes. CSM’s excellent dielectric properties, combined with its flame resistance and heat tolerance, make it suitable for insulating medium- to high-voltage power cables, particularly those exposed to outdoor or chemically aggressive environments. - Q4: Is CSM better than EPDM or CR?
CSM offers better chemical, flame, and UV resistance than EPDM. Compared to CR (neoprene), it is more resistant to weathering and heat but slightly less oil resistant. The choice depends on the specific application environment and cost-performance balance. - Q5: What’s the storage condition for CSM rubber?
Store CSM rubber in a cool, dry, and well-ventilated place, away from direct sunlight, heat sources, and strong oxidants. Keep it in sealed packaging to avoid moisture absorption and prolong shelf life. Proper storage ensures consistent processing and product quality.