Chlorinated polyvinyl chloride pipes is widely used in industrial applications for transporting hot water, corrosive chemicals, and aggressive fluids due to its excellent heat resistance and chemical stability. It is commonly found in chemical processing, water treatment plants, power generation, and metal finishing facilities. Its non-corrosive nature, high pressure tolerance, and long service life make it a reliable and cost-effective alternative to metal pipes in demanding industrial environments.
1. What Is The Full Meaning Of CPVC?
So you might wonder what those four letters actually stand for when somebody mentions CPVC in your facility planning meetings. Well CPVC stands for Chlorinated Polyvinyl Chloride which basically tells you right away that this material has something extra compared to regular PVC.
The chlorination process fundamentally changes how this piping material behaves under stress making it suitable for many applications where standard PVC would fail miserably. The molecular structure gets altered during manufacturing when chlorine atoms replace hydrogen atoms in alternating carbon chains creating a more densely packed and rigid material. This seemingly small chemical modification makes a world of difference in performance characteristics that matter greatly in industrial settings.
The manufacturing process involves taking regular PVC resin and subjecting it to a chlorination reaction where chlorine gas flows through fluidized PVC particles. This reaction happens at carefully controlled temperatures and requires precise timing to achieve just right chlorine content typically between 63-69% compared to regular PVC which contains about 57% chlorine.
Manufacturers then compound this base material with various stabilizers processing aids impact modifiers and colorants to create formulations optimized for specific industrial applications. You might notice different brands having slightly different performance characteristics due to these proprietary formulation differences even though they all qualify as CPVC under industry standards.
Looking back at history CPVC first appeared commercially in mid-1950s when BF Goodrich (now part of Lubrizol) developed this material to address limitations of standard PVC in hot water applications.
Since then numerous advancements in formulation technology have expanded its use across multiple industries. The material gained significant traction in North American industrial markets during 1970s and 1980s as manufacturers demonstrated its cost advantages over traditional metal piping in corrosive environments.
Today global production capacity continues expanding with major manufacturing facilities across North America Europe and Asia producing millions of pounds annually to meet growing demand from chemical processing water treatment and industrial manufacturing sectors.
Physical properties that truly define CPVC and make it valuable for industrial use include its exceptional heat resistance with continuous service temperature rating up to 200°F (93°C) which significantly exceeds regular PVC’s 140°F (60°C) limitation.
This higher temperature tolerance opens up applications in hot water distribution process lines and heated chemical transport that would quickly deform standard plastic piping. Another defining characteristic remains its outstanding chemical resistance particularly against acids bases salts and many aliphatic hydrocarbons that would rapidly corrode metallic piping systems.
The material maintains pressure ratings at elevated temperatures better than most thermoplastics giving engineers confidence when designing systems that must handle both heat and pressure simultaneously.
These fundamental properties combined with relatively low thermal conductivity good flame resistance and non-conductive nature make CPVC a truly versatile material for challenging industrial environments where multiple stress factors exist simultaneously.
2. Why Do Engineers Choose CPVC Over Other Piping Materials?
Temperature resistance tops many lists when engineers justify CPVC selection for industrial projects. Unlike standard PVC which begins to soften and lose structural integrity around 140°F CPVC maintains its mechanical properties at temperatures approaching 200°F in continuous service applications.
This expanded temperature range proves absolutely critical in facilities where process fluids run hot but not quite hot enough to justify expensive alloys or specialized high-temperature materials. You can install CPVC confidently in areas near heat sources where ambient temperatures fluctuate significantly without worrying about premature failure or deformation that would plague standard thermoplastics.
The material also exhibits relatively low thermal expansion compared to other plastics reducing stress on hangers supports and connection points when temperature cycling occurs during normal operations or maintenance shutdowns.
Chemical resistance profiles make CPVC particularly attractive across numerous industrial sectors. The material stands up remarkably well against most inorganic acids including sulfuric hydrochloric and phosphoric acids at concentrations that would rapidly deteriorate metal piping systems. It also resists many bases salt solutions and oxidizing agents commonly found in chemical processing water treatment and manufacturing environments.
You can transport bleach solutions caustic cleaners and many process chemicals without fear of internal corrosion or contamination issues that would necessitate frequent replacement of metal alternatives. This broad chemical compatibility translates directly into lower maintenance costs extended service life and reduced downtime for critical systems where reliability matters tremendously.
Factory managers particularly appreciate avoiding unexpected failures and emergency shutdowns caused by chemical attack on piping infrastructure.
Pressure capabilities deserve serious consideration when evaluating CPVC against alternatives. Standard Schedule 80 CPVC pipe maintains impressive pressure ratings even at elevated temperatures with typical 2-inch pipe handling 320 psi at 73°F and still managing 130 psi at 180°F.
These ratings exceed what many applications actually require providing comfortable safety margins for system designers. The material also maintains consistent pressure performance over time without degradation issues that affect some alternative materials.
You can design systems with confidence knowing that properly installed CPVC will handle specified pressures throughout its service life without creep or stress relaxation problems common to some other thermoplastics. This pressure stability combined with temperature resistance creates a sweet spot for many industrial applications where moderate pressure and elevated temperature conditions exist simultaneously.
Fire safety characteristics often surprise engineers unfamiliar with CPVC properties. The material features limited combustibility with flame spread ratings under 25 according to ASTM E84 testing.
More importantly it self-extinguishes when removed from direct flame sources rather than continuing to burn independently. This inherent flame resistance stems from chlorine content in molecular structure which acts as built-in flame retardant without requiring additional chemical additives that might leach out over time.
You can install CPVC with greater confidence in areas where fire safety concerns exist knowing that it won’t contribute significantly to flame spread during fire events. Many insurance underwriters and facility safety managers recognize these advantages when evaluating material choices for critical process systems especially in facilities handling flammable materials.
Cost analysis consistently favors CPVC when compared against metal alternatives for compatible applications. Material costs typically run 30-80% lower than comparable stainless steel systems depending on current metal market conditions. Installation costs drop even more dramatically with lighter weight materials requiring fewer workers less specialized equipment and faster completion times.
You can expect significant labor savings during installation with no welding requirements simpler cutting procedures and easier handling throughout construction. Maintenance costs over system lifetime typically decrease substantially with no corrosion issues to address no painting or coating requirements and simpler repair procedures when modifications become necessary.
Total lifecycle cost calculations often show CPVC systems costing less than half their metal counterparts when all factors receive proper consideration making budget justification straightforward for procurement teams and financial decision makers.
3. How Does CPVC Perform In Different Industrial Environments?
High-temperature processing facilities present unique challenges that CPVC handles surprisingly well within specific parameters. The material maintains structural integrity and pressure ratings in environments where ambient temperatures remain elevated throughout production cycles.
Factory areas near ovens kilns or steam equipment often maintain ambient temperatures that would quickly degrade standard PVC but CPVC continues functioning normally. You can route process water cooling loops non-steam heating circuits and temperature-controlled chemical lines through these areas without constant concerns about premature failures.
The material does have absolute temperature limitations however and begins losing significant strength above 200°F making alternative materials necessary for steam or extremely hot process fluids. Proper system design must account for maximum temperature exposure including unexpected excursions during abnormal operating conditions or equipment malfunctions nearby that might temporarily raise ambient temperatures beyond normal ranges.
Chemical processing and transport systems represent perhaps ideal applications for CPVC piping networks. The material handles most acids bases and salt solutions without degradation issues that would rapidly destroy carbon steel or even compromise some stainless alloys.
Chemical manufacturing facilities particularly appreciate CPVC for intermediate process lines transfer piping and distribution systems where corrosive materials flow regularly. You can design entire chemical handling systems using CPVC with confidence that material compatibility issues won’t create unexpected failures or contamination problems.
The material also maintains dimensional stability when exposed to many chemicals avoiding swelling shrinking or distortion problems that affect some alternative thermoplastics. This stability proves particularly valuable in precision chemical dosing applications where consistent flow characteristics must remain unchanged over extended service periods.
Facility operators report fewer emergency maintenance events and more predictable service life when using CPVC for compatible chemical service compared to nearly any alternative material option.
Corrosive environments beyond just chemical exposure include atmospheric conditions found in many industrial settings. Coastal facilities dealing with salt air paper mills with sulfur compounds chemical plants with acidic vapors and water treatment facilities with chlorine atmospheres all create external corrosion challenges for piping systems.
CPVC performs exceptionally well under these conditions requiring no external coatings paints or protective measures to prevent atmospheric attack. You can install exposed CPVC runs throughout these facilities without concerns about external degradation rust formation or coating maintenance that would burden metal piping installations.
The material also resists biological growth algae formation and microbiologically influenced corrosion that affects many systems in humid or wet environments. This corrosion resistance extends system lifetime reduces maintenance requirements and maintains flow characteristics without internal surface roughening that would gradually increase friction losses and reduce system efficiency over time.
Water treatment applications represent major success stories for industrial CPVC implementations. Municipal and industrial water treatment facilities widely adopt CPVC for chlorine handling ozone distribution chemical feed systems and filtered water transport.
The material handles chlorine compounds sodium hypochlorite caustic soda alum solutions and other water treatment chemicals without degradation concerns that would necessitate exotic metal alloys. You can design comprehensive treatment systems using predominantly CPVC materials creating cost-effective installations with excellent service life expectations.
The material also maintains water quality without contributing taste odor or discoloration issues sometimes associated with metal piping especially during initial startup or after system modifications. Treatment plant operators particularly value these characteristics when handling finished water streams where contamination concerns remain paramount.
The non-conductive nature also eliminates galvanic corrosion concerns in mixed-material systems where dissimilar metals might otherwise create premature failure points.
Food and beverage processing facilities face unique requirements where CPVC offers specific advantages for non-contact applications. While not typically used for direct food contact due to regulatory considerations CPVC serves admirably in peripheral systems supporting food production.
Wash-down water supply lines cleaning solution distribution chemical handling systems and waste transport piping commonly utilize CPVC materials. You can implement these supporting systems with confidence that they’ll handle sanitizing chemicals cleaning agents and varying temperature conditions without contamination or failure concerns.
The smooth interior surface resists biofilm formation scaling and product buildup that might harbor bacteria or affect system performance over time. This characteristic proves particularly valuable in facilities requiring frequent cleaning and sanitizing procedures where harsh chemicals might attack other piping materials.
The material also withstands many cleaning protocols including hot water sanitizing cycles without degradation issues that would affect some alternative plastic options.
Performance limitations and environmental constraints deserve honest consideration when evaluating CPVC for specific applications. The material does have definite boundaries beyond which alternative materials become necessary. Continuous exposure to temperatures above 200°F causes progressive degradation and should be avoided entirely. Certain chemicals particularly chlorinated solvents ketones and some aggressive organic compounds can attack CPVC causing swelling softening or outright failure. You must carefully verify chemical compatibility using manufacturer resistance charts before implementing CPVC for any chemical handling application.
The material also exhibits greater brittleness than some alternative thermoplastics especially at lower temperatures making it somewhat more vulnerable to physical impact damage during maintenance activities or from moving equipment in busy facilities.
Proper installation with adequate support protection from mechanical damage and appropriate allowances for thermal movement helps mitigate these limitations in most industrial applications. Environmental considerations include end-of-life disposal challenges as CPVC requires specialized recycling processes not widely available in all regions.
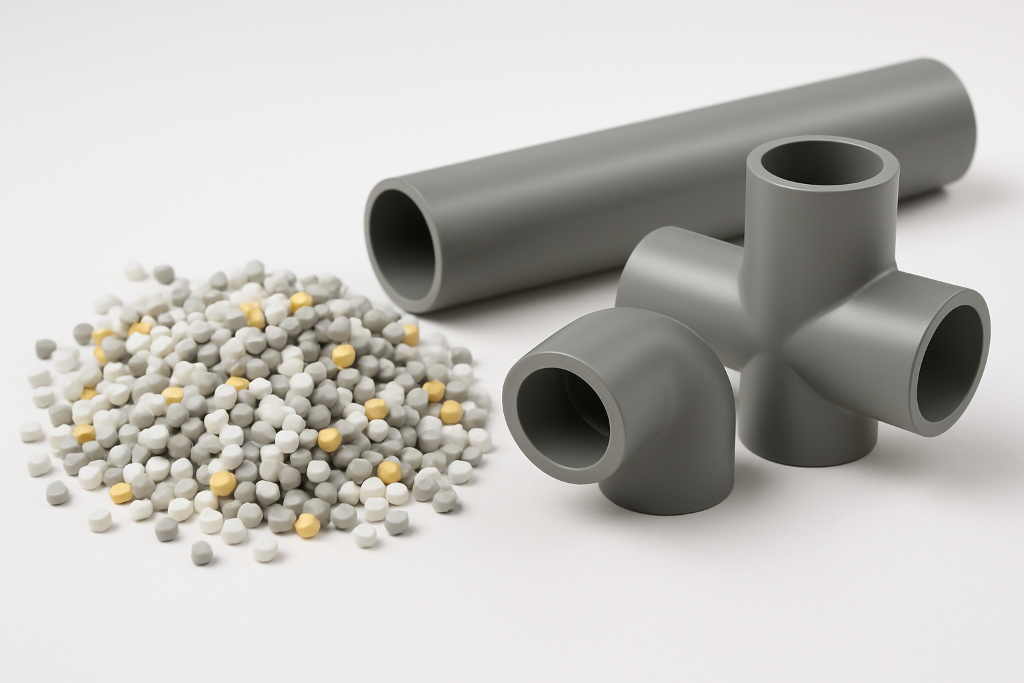
4. What Are The Installation Requirements For CPVC Piping Systems?
Proper joining methods fundamentally determine CPVC system reliability regardless of material quality or design excellence. Solvent cement welding remains most common and creates joints actually stronger than pipe itself when executed correctly.
This process involves applying primer which prepares surfaces by softening and cleaning them followed by solvent cement application which chemically fuses components together as solvents evaporate. You must select cements specifically formulated for CPVC rather than standard PVC products as chemical compositions differ significantly. Threaded connections provide another option particularly for connections to equipment valves or transitions to other materials but require careful thread cutting with proper lubricants and sealants compatible with CPVC chemistry. Flanged connections work well for larger diameters and locations requiring frequent disassembly with appropriate gasket materials and careful bolt torquing procedures.
Each joining method requires specific training proper tools and attention to manufacturer guidelines regarding cure times temperature limitations and application techniques. Rushed or improper joining procedures account for majority of premature system failures making this aspect perhaps most critical for long-term success.
Expansion and contraction considerations cannot be overlooked when designing CPVC piping networks. The material expands approximately 3.8 inches per 100 feet per 100°F temperature change – significantly more than metals but less than many other thermoplastics.
This thermal movement must be accommodated through proper design including expansion loops offsets changes in direction or mechanical expansion joints in longer straight runs. You must provide adequate support while still allowing controlled movement to prevent excessive stress concentration at fittings or fixed points. Anchors and guides require strategic placement throughout system to direct expansion forces predictably without creating excessive stress.
Failure to properly address thermal expansion often results in pulled joints broken supports or cracked fittings particularly in systems experiencing significant temperature cycling. Proper design calculations must account for maximum temperature differential between installation conditions and operating extremes including both normal operation and potential upset conditions that might temporarily push temperatures toward material limits.
Support and hanging requirements differ significantly from metal piping due to material properties and thermal movement needs. CPVC requires more frequent support points with maximum spacing determined by pipe diameter operating temperature and fluid density.
Standard industry guidelines typically specify supports every 5-7 feet for horizontal runs of 2-inch pipe with closer spacing for larger diameters or elevated temperatures. Support materials must include appropriate cushioning or protective elements to prevent abrasion damage from movement across rough surfaces. You should select hangers specifically designed for plastic piping rather than repurposing metal pipe supports which often have sharp edges or insufficient bearing surface area. Vertical runs require support at base plus intermediate restraints to prevent excessive loading on lower fittings.
Proper support design balances need for secure mounting against requirement for controlled movement during thermal expansion and contraction cycles. Inadequate or improper support systems frequently contribute to premature failures through excessive stress sagging or abrasion damage even when all other installation aspects meet requirements.
Transition fitting options deserve careful consideration wherever CPVC connects to other piping materials. Metal-to-CPVC transitions present particular challenges due to different thermal expansion rates galvanic corrosion potential and mechanical stress considerations. Specialized transition fittings with appropriate dielectric protection prevent galvanic issues when connecting to copper or steel components. Threaded transitions require careful thread preparation compatible sealants and proper torque control to prevent cracking from overtightening.
You can utilize flanged connections with appropriate gaskets for larger diameter transitions or locations requiring future disassembly. Mechanical couplings with appropriate gasket materials provide another option particularly for transitions to grooved piping systems.
Each transition type requires specific installation procedures and limitations regarding pressure temperature and external loading. Transitions often represent weakest points in mixed-material systems making proper selection and installation particularly critical for system reliability.
Manufacturers offer extensive transition fitting options designed specifically for common material combinations encountered in industrial applications with engineered solutions for most connection challenges.
Tools and equipment needed for proper installation include several specialized items beyond standard plumbing tools. Pipe cutters designed specifically for CPVC produce square clean cuts without creating stress-concentrating burrs or cracks that might propagate during service.
Chamfering tools prepare pipe ends for proper solvent cement application ensuring full penetration into fitting sockets. Appropriate applicators for primers and cements ensure proper coverage without excessive material that might run inside pipes creating flow restrictions.
You need proper measuring and marking tools for accurate layout including allowances for fitting dimensions and insertion depths. Specialized tools for larger diameters include strap wrenches that won’t damage pipe surfaces chain vises for secure holding during cutting and threading operations and support equipment for handling longer pipe sections.
Temperature monitoring equipment helps verify appropriate conditions during installation as extreme temperatures affect solvent cement cure times and joint quality.
Investment in proper tools pays dividends through faster installation better joint quality and reduced callback issues compared to attempting installation with inadequate or improvised equipment.
Common installation mistakes provide valuable learning opportunities for avoiding similar problems in your projects. Inadequate surface preparation ranks among most frequent errors with installers skipping primer application rushing drying times or failing to remove surface contamination before joining.
Improper cement selection also causes problems particularly using standard PVC cement on CPVC which creates chemically incompatible joints prone to early failure. Insufficient cement application leaves dry spots in joint areas while excessive application creates internal obstructions or weakened areas from solvent damage.
You should avoid overtightening threaded connections which cracks female threads due to CPVC’s relatively rigid nature compared to other thermoplastics. Failing to properly align pipes before joining creates stress concentrations that may not cause immediate failure but significantly reduce service life under operating conditions.
Inadequate curing time before pressure testing represents another common mistake as joints require full chemical cure before withstanding system pressures. Rushing installation during cold weather without accounting for extended cure times similarly leads to joint failures during initial testing or early service. Learning from these common errors helps installation teams avoid costly mistakes and callbacks while ensuring system reliability matches material capabilities.
5. How Long Does CPVC Piping Last In Industrial Settings?
Expected service life under various conditions represents primary consideration for many industrial buyers evaluating CPVC against alternatives. Under optimal conditions with appropriate chemical compatibility moderate temperatures and proper installation CPVC systems routinely deliver 30+ years of reliable service.
This longevity matches or exceeds many metallic alternatives particularly in corrosive environments where metals might require replacement in as little as 2-5 years.
You can reasonably expect decades of trouble-free operation from properly designed and installed systems handling compatible chemicals within temperature limitations. Actual service life varies considerably based on specific operating conditions with higher temperatures chemical exposure pressure cycling and external factors all influencing longevity.
Manufacturers typically warranty materials against defects for periods ranging from 5-10 years but practical experience demonstrates much longer actual service life in most applications. This extended service life translates directly into lower lifecycle costs reduced replacement expenses and fewer production interruptions for maintenance activities compared to many alternative materials in compatible applications.
Factors affecting longevity and performance include several variables both within and beyond system designer control. Chemical exposure represents perhaps most significant variable with incompatible chemicals dramatically reducing service life through material degradation swelling or embrittlement.
Temperature conditions similarly impact longevity with systems operating near maximum temperature ratings experiencing accelerated aging compared to moderate temperature applications. Pressure cycling causes cumulative fatigue effects particularly in systems frequently starting and stopping or experiencing significant pressure fluctuations during normal operation. You should consider UV exposure for outdoor installations as unprotected CPVC gradually degrades under direct sunlight requiring either protective coatings or UV-resistant formulations for external applications. Physical damage from maintenance activities vibration from nearby equipment or improper support also reduces service life through stress concentration or abrasion effects.
Water hammer presents particular concerns in liquid handling systems where sudden valve closures create pressure spikes exceeding normal design parameters. Proper system design installation and operation mitigates many these factors extending service life toward maximum material capabilities under given conditions.
Signs of degradation and replacement indicators provide valuable guidance for maintenance planning and system management. Discoloration often provides earliest visible indication with yellowing or browning suggesting thermal degradation while whitening might indicate chemical attack on pipe surfaces.
Surface crazing (fine networks of shallow cracks) suggests environmental stress cracking from chemical exposure combined with mechanical stress. Embrittlement manifests through unusual breakage during minor impacts or maintenance activities that previously caused no damage.
You should monitor pressure drop increases across system segments as internal surface degradation roughens pipe interiors increasing friction losses and reducing flow capacity. Visible deformation including sagging between supports bulging near fittings or dimensional changes indicates material softening from chemical attack or excessive temperature exposure.
Regular inspection programs focusing on these indicators help identify potential issues before catastrophic failures occur allowing planned replacement during scheduled maintenance periods rather than emergency repairs during production. Proactive replacement based on condition monitoring typically costs significantly less than emergency response to unexpected failures particularly considering production losses during unplanned downtime.
Preventative maintenance practices significantly extend CPVC system service life even under challenging conditions. Regular inspection programs identifying early degradation signs allow intervention before problems affect system performance.
Proper water treatment in recirculating systems prevents scale buildup biological growth and particulate accumulation that might create localized turbulence or abrasion issues. Temperature monitoring ensures systems remain within design parameters particularly during abnormal operating conditions or nearby equipment changes that might affect ambient conditions.
You can implement periodic pressure testing at levels below maximum ratings but above normal operating pressures to identify developing weaknesses before they cause in-service failures. Proper chemical management prevents accidental exposure to incompatible substances through clear labeling documented procedures and staff training regarding system limitations.
Support system maintenance ensures continued proper alignment appropriate movement allowance and protection from physical damage throughout service life. These preventative practices require minimal investment compared to premature replacement costs making them highly cost-effective approaches for maximizing system longevity and reliability in industrial applications.
Case studies of long-term CPVC installations provide compelling evidence for material capabilities under real-world conditions. Chemical processing facilities report CPVC acid handling lines remaining in continuous service for 25+ years without significant degradation or performance issues.
Water treatment plants document similar experiences with chlorine distribution systems and chemical feed lines maintaining full functionality after decades of operation. Industrial cooling water systems demonstrate excellent longevity particularly in facilities where corrosive water conditions would rapidly degrade metal alternatives. You can find documented examples across nearly every industrial sector with properly selected and installed CPVC consistently outperforming expected service life projections.
These case studies frequently highlight importance of proper material selection appropriate installation techniques and ongoing system management in achieving optimal results. Facilities maintaining good records regarding installation dates operating conditions and maintenance history provide particularly valuable data for evaluating actual service life expectations in similar applications.
Industry organizations and major manufacturers maintain extensive case study libraries documenting successful long-term installations across diverse industrial environments.
Warranty considerations from major manufacturers provide additional confidence for industrial buyers evaluating CPVC systems. Leading manufacturers typically offer material defect warranties ranging from 5-10 years depending on specific product lines application environments and installation certification requirements.
These warranties generally cover material replacement costs but may exclude labor expenses or consequential damages resulting from system failures. You should carefully review warranty documentation noting specific exclusions maintenance requirements and notification procedures for warranty claims.
Some manufacturers offer extended warranty programs for installations completed by certified contractors following documented procedures with appropriate inspection and documentation.
Warranty coverage typically excludes damage from chemical exposure outside published compatibility guidelines improper installation techniques or operation beyond specified temperature and pressure limitations.
While warranties provide valuable protection against manufacturing defects they represent minimum performance expectations rather than typical service life projections. Most properly designed and installed systems significantly outlast warranty periods continuing reliable operation long after coverage expires.