6. What Safety Considerations Apply To Industrial CPVC Systems?
Pressure testing protocols and requirements ensure system integrity before placing CPVC piping into service. Hydrostatic testing remains most common method involving filling system with water removing air pockets and gradually increasing pressure to specified test level typically 150% of maximum operating pressure but not exceeding pipe pressure rating at test temperature.
This pressure must maintain for specified duration usually minimum one hour while technicians inspect all joints connections and pipe segments for leakage or deformation. You must follow specific procedures regarding pressure increase rates maximum test pressures and temperature considerations as CPVC strength decreases at elevated temperatures.
Pneumatic testing using compressed air or nitrogen presents special hazards due to stored energy and should be avoided unless absolutely necessary with strict pressure limitations and safety protocols. Testing documentation should include test pressure duration temperature ambient conditions and inspection results creating permanent record of initial system condition.
Proper pressure testing identifies installation defects before system commissioning preventing costly leaks or failures during actual operation while establishing baseline for future comparison during routine maintenance inspections or system modifications.
Temperature monitoring best practices protect CPVC systems from exceeding material limitations during operation. Strategic placement of temperature sensors throughout system particularly near heat sources potential hot spots or critical process areas provides early warning of approaching temperature limits. Continuous monitoring systems with alarm capabilities offer greatest protection automatically alerting operators when temperatures approach critical thresholds.
You should implement administrative controls including documented operating procedures training programs and visual indicators highlighting temperature limitations for maintenance and operations personnel.
Automated shutdown capabilities for heating systems or diversion valves for overheated process streams provide additional protection layers for critical applications where temperature excursions could cause significant damage or safety hazards.
Regular calibration verification of temperature monitoring equipment ensures accurate readings throughout system service life. These temperature management practices prevent premature degradation extend system longevity and reduce risks associated with potential failures from thermal damage particularly important in facilities where process upsets or control system failures might create temporary temperature excursions beyond normal operating ranges.
Chemical compatibility verification process represents critical safety element for CPVC piping systems handling industrial chemicals.
Comprehensive compatibility assessment begins during design phase using manufacturer chemical resistance charts identifying acceptable exposure conditions for all process fluids including cleaning agents maintenance chemicals and potential contaminants.
Laboratory testing of specific chemical combinations under actual operating conditions provides additional verification for critical applications or unusual chemical mixtures not clearly addressed in standard reference materials. You should implement management of change procedures requiring chemical compatibility review before introducing new substances into existing CPVC systems.
Proper labeling of piping systems clearly identifies contents and pressure/temperature limitations helping prevent accidental exposure to incompatible materials during operation or maintenance activities. Documented training programs ensure all personnel understand chemical compatibility limitations and procedures for evaluating potential new exposures.
These verification processes prevent catastrophic failures from chemical attack which might otherwise create significant safety hazards through sudden releases of hazardous materials or system failures under pressure.
Regulatory compliance considerations vary by industry location and specific application but generally include several common elements for CPVC piping systems.
Building codes typically address flame spread ratings smoke development characteristics and installation requirements particularly for systems in occupied spaces or critical facility areas. Industry-specific regulations may impose additional requirements such as NSF/ANSI 61 certification for potable water contact FDA compliance for food-adjacent applications or specific pressure testing documentation for hazardous material handling.
You must verify applicable local state and federal regulations during design phase ensuring selected materials installation methods and testing protocols satisfy all jurisdictional requirements. Proper documentation including material certifications test reports installation records and maintenance history demonstrates compliance during regulatory inspections or incident investigations.
Some facilities require registered professional engineer approval for pressure piping systems above certain size or pressure thresholds regardless of material selection. Understanding and addressing these regulatory requirements during design and installation prevents costly modifications enforcement actions or operational restrictions that might otherwise impact facility operations.
Emergency response procedures for system failures require advance planning and preparation regardless of how unlikely failures might seem.
Response plans should address potential failure scenarios including chemical releases pressure loss flooding or system damage from external causes. Isolation valve placement throughout system enables rapid shutdown of affected segments minimizing release volumes and damage extent during failure events. Emergency repair kits containing appropriate materials tools and instructions enable rapid response to minor leaks or damages before they escalate into major failures.
You should conduct regular training exercises ensuring maintenance personnel can quickly locate isolation points implement temporary repairs and properly document incident details for subsequent investigation. Clearly documented procedures for system drainage neutralization of hazardous contents and safe repair protocols protect both personnel and facilities during emergency response activities.
These preparations minimize consequences from unexpected failures reducing potential injury risks environmental impacts and production losses that might otherwise result from inadequate emergency response capabilities.
Personal protective equipment for installation and maintenance activities protects workers from specific hazards associated with CPVC piping systems.
Chemical resistant gloves appropriate for specific solvents and cements used during installation prevent skin contact with potentially harmful substances. Eye protection shields against splashes during solvent application pressure testing or system drainage procedures.
Respiratory protection may be necessary when working with primers and cements in confined or poorly ventilated areas as solvent vapors can cause respiratory irritation or more serious health effects with prolonged exposure.
You should provide appropriate protective clothing for workers handling hazardous chemicals during system maintenance or repair activities. Proper training regarding PPE selection use limitations and maintenance ensures effective protection during all work activities.
Job hazard analysis for specific tasks identifies appropriate protection levels for each activity preventing both overprotection that might create unnecessary discomfort or mobility restrictions and underprotection that could leave workers vulnerable to preventable injuries or chemical exposures. These protective measures demonstrate commitment to worker safety while ensuring regulatory compliance with applicable workplace safety regulations.
7. How Does CPVC Compare To Alternative Piping Materials?
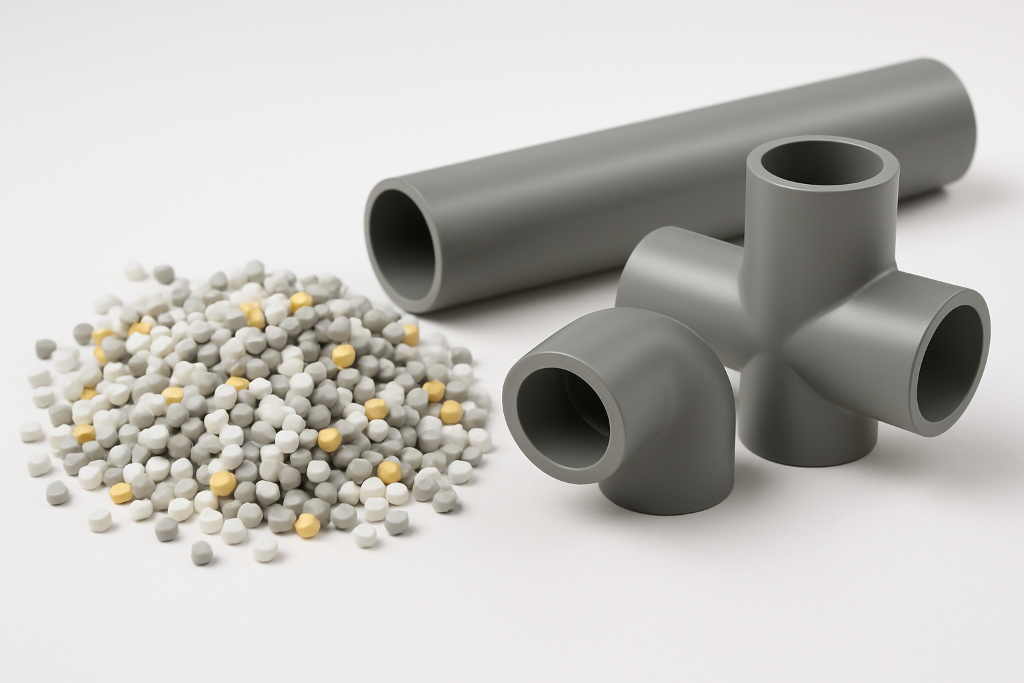
CPVC versus carbon steel piping comparison reveals distinct advantages and limitations for each material. Carbon steel offers higher temperature resistance handling steam and process fluids exceeding 200°F without degradation issues that would affect CPVC.
Steel also provides superior mechanical strength withstanding greater external loads impact forces and pressure ratings particularly at elevated temperatures.
However carbon steel suffers significant disadvantages regarding corrosion resistance requiring protective coatings internal linings or chemical treatment programs to prevent rapid deterioration in many industrial environments. Installation costs typically run significantly higher for steel with requirements for welding specialized cutting equipment heavier support systems and more labor-intensive processes throughout construction.
You can expect substantially higher maintenance expenses with steel systems including regular inspection for corrosion coating maintenance and eventual replacement due to internal or external degradation. CPVC eliminates these corrosion concerns in compatible applications offering maintenance-free operation without protective coatings or chemical treatment programs.
The plastic option weighs approximately one-sixth as much as comparable steel pipe reducing structural loading requirements and simplifying installation particularly in retrofit applications where existing support structures may have limited additional capacity. This weight difference also significantly reduces shipping costs and simplifies material handling throughout construction process.
CPVC versus stainless steel performance analysis presents more nuanced comparison as both materials offer excellent corrosion resistance in many environments. Stainless steel particularly higher alloys like 316L provides superior temperature resistance handling steam and process fluids well beyond CPVC limitations. The metal option also offers greater pressure capacity especially at elevated temperatures and better resistance to physical damage from external forces.
However stainless steel costs substantially more than CPVC with material expenses typically running 3-5 times higher depending on current market conditions and specific alloy requirements. Installation expenses similarly exceed CPVC significantly with specialized welding requirements passivation procedures and heavier support systems adding to overall project costs.
You might encounter unexpected corrosion issues with stainless in certain chemical environments particularly those containing chlorides which cause pitting and stress corrosion cracking even in higher alloys.
CPVC actually outperforms many stainless grades in chloride-containing environments making it preferred choice for chlorine handling sodium hypochlorite distribution and similar applications common in water treatment and chemical processing.
The plastic option also eliminates concerns about metallic contamination making it preferred for high-purity applications where metal ions might affect process chemistry or product quality.
CPVC versus copper piping in industrial applications highlights significant differences in material properties application suitability and economic considerations.
Copper offers moderate corrosion resistance good heat transfer characteristics and established installation methods familiar to most mechanical contractors. It handles higher temperatures than CPVC and provides natural antimicrobial properties beneficial in some specialized applications.
However copper remains vulnerable to erosion-corrosion in high-velocity applications acidic water conditions and exposure to many industrial chemicals that rapidly attack this relatively soft metal. Material costs fluctuate significantly with volatile copper commodity markets but typically exceed CPVC by substantial margins even during favorable market conditions.
You can expect higher installation costs with copper systems due to brazing or soldering requirements specialized tools and more labor-intensive joining processes compared to CPVC solvent welding. The metal option also raises concerns about metal ion leaching in sensitive applications potentially affecting product quality or process chemistry in pharmaceutical food processing or semiconductor manufacturing environments.
CPVC eliminates these contamination concerns while providing superior chemical resistance in most industrial environments making it preferred choice for process chemical handling corrosive water distribution and similar applications where copper would experience accelerated degradation.
CPVC versus other thermoplastics (PP PE PVDF) comparison reveals important differences even among seemingly similar plastic piping materials. Polypropylene (PP) offers excellent chemical resistance particularly against strong bases and some solvents that might attack CPVC but provides lower pressure ratings especially at elevated temperatures.
Polyethylene (PE) delivers outstanding flexibility impact resistance and fatigue strength but cannot handle temperatures approaching CPVC capabilities and suffers from lower pressure ratings and potential oxidation issues in some environments.
Polyvinylidene fluoride (PVDF) provides exceptional chemical resistance even against solvents that attack CPVC but costs substantially more approaching or exceeding stainless steel in many markets. You should consider specific application requirements including maximum temperature chemical exposure pressure requirements and installation constraints when selecting among these thermoplastic options.
CPVC generally offers best balance between chemical resistance temperature capability and economic considerations for many industrial applications particularly those involving acids bases and salt solutions at moderate temperatures. Each thermoplastic presents distinct joining methods support requirements and installation considerations requiring contractor familiarity with specific material characteristics for successful implementation.
Material selection among thermoplastic options often comes down to specific chemical compatibility temperature requirements and economic considerations rather than clear superiority of any single material across all potential applications.
Decision matrix for material selection provides structured approach for evaluating piping material options against specific application requirements.
Comprehensive evaluation should include temperature requirements chemical compatibility pressure ratings mechanical strength needs installation considerations maintenance expectations and economic factors including both initial and lifecycle costs.
Weighted scoring systems help prioritize factors most critical for specific applications while ensuring all relevant considerations receive appropriate attention during selection process. You can develop customized decision matrices addressing unique requirements for your facility or process conditions ensuring systematic evaluation rather than defaulting to familiar materials without proper analysis. This structured approach often identifies optimal material choices that might otherwise be overlooked through habit or incomplete consideration of alternatives.
The evaluation process should include input from multiple stakeholders including operations personnel maintenance teams design engineers and financial decision makers ensuring all perspectives receive consideration during selection process.
Properly executed material selection using comprehensive decision matrix typically identifies most appropriate material for specific application conditions while documenting reasoning behind selection for future reference during system modifications expansions or replacements.
Total cost of ownership calculations provide compelling economic justification for appropriate material selection beyond simple initial purchase price comparisons.
Comprehensive analysis includes material costs installation expenses maintenance requirements expected service life replacement frequency and operational impacts including energy efficiency production reliability and downtime risks. CPVC frequently demonstrates lowest total ownership cost for compatible applications despite sometimes higher initial material costs compared to basic options like carbon steel.
Installation savings from lighter weight simpler joining methods and reduced labor requirements often offset any material cost premium within initial construction budget. You can expect significant maintenance savings throughout system lifetime with no painting requirements corrosion monitoring or protective treatment programs necessary for CPVC systems.
Extended service life in corrosive environments dramatically reduces replacement frequency and associated costs including both direct expenses for materials and labor and indirect costs from production interruptions during system replacement. Energy efficiency considerations include smoother interior surfaces maintaining lower friction losses throughout service life and superior insulating properties reducing heat loss in hot service applications or condensation issues in cold service.
These combined economic factors frequently demonstrate substantial total cost advantages for CPVC in compatible applications even when initial material costs exceed metal alternatives.
FAQ
Q1: Can CPVC handle steam and hot water transport in manufacturing facilities?
CPVC can handle hot water up to 200°F (93°C) continuously but is not suitable for steam transport. The material degrades when exposed to steam pressure making alternatives like stainless steel more appropriate for steam applications. For hot water below this temperature threshold CPVC remains a cost-effective and corrosion-resistant option. You should carefully verify maximum temperature exposure including potential excursions during abnormal operations before selecting CPVC for hot water service. The material performs exceptionally well in hot water return lines heating system distribution networks and process water applications throughout this temperature range. Many facilities successfully implement CPVC for hot water systems where temperatures remain controlled below specified limits while using alternative materials only for higher temperature segments creating hybrid systems optimized for both performance and economy. Proper design must include appropriate expansion compensation adequate support and clear identification of temperature limitations for maintenance personnel to prevent inadvertent exposure to excessive temperatures during system modifications or repairs.
Q2: What chemicals will damage or degrade CPVC piping systems?
Strong oxidizing acids polar solvents like ketones and esters and certain hydrocarbons can degrade CPVC. Chemicals like chlorinated solvents aromatic compounds and some aggressive cleaning agents should be avoided. Always consult chemical resistance charts from manufacturers before implementing CPVC in chemical transport applications. You must consider not only primary process chemicals but also cleaning agents maintenance chemicals and potential contaminants that might occasionally contact piping systems. Concentration temperature and exposure duration significantly affect compatibility with some chemicals acceptable at room temperature but problematic at elevated temperatures or higher concentrations. Some chemical effects develop gradually over extended exposure periods rather than causing immediate visible damage making thorough compatibility verification particularly important for critical applications. Manufacturers maintain extensive chemical resistance databases based on laboratory testing and field experience providing valuable guidance for specific applications and exposure conditions. Independent testing with actual process chemicals under operating conditions provides additional verification for critical applications or unusual chemical combinations not clearly addressed in standard reference materials.
Q3: Is CPVC piping suitable for underground industrial installations?
CPVC can be installed underground for industrial applications with proper bedding backfill and protection. The material requires sand or fine gravel bedding appropriate depth coverage and consideration for ground movement. Underground CPVC installations typically need thicker pipe walls and may require additional protective measures against root intrusion and ground shifting. You should implement tracer systems for non-metallic underground piping ensuring future locating capability for maintenance or excavation activities near buried lines. Proper compaction procedures prevent excessive loading while maintaining adequate support throughout pipe length. Thrust blocking at direction changes prevents joint separation from hydraulic forces particularly important in pressurized systems experiencing temperature fluctuations. The material performs well in most soil conditions but requires protection from sharp rocks potential impact damage during backfilling and excessive point loading from large stones or construction equipment. These installation requirements add some complexity compared to above-ground installations but CPVC still offers significant advantages over metal alternatives for compatible applications particularly regarding corrosion resistance in aggressive soil conditions.
Q4: How do temperature fluctuations affect CPVC piping systems?
Temperature fluctuations cause CPVC to expand and contract at a rate of approximately 3.8 inches per 100 feet per 100°F temperature change. Proper installation must include expansion loops offsets or expansion joints to accommodate this movement. Failure to account for thermal expansion can result in stress on fittings potential leaks or system failure. You should design systems with appropriate anchors and guides directing expansion movement predictably without creating excessive stress concentrations at fittings or connection points. Support systems must allow controlled lateral movement while maintaining vertical support preventing sagging or misalignment during thermal cycles. The material exhibits greater expansion than metals but less than many other thermoplastics requiring careful design particularly at transitions between different materials with mismatched expansion rates. Systems experiencing frequent or rapid temperature changes require special attention to expansion compensation with additional loops or mechanical expansion joints at strategic locations. Proper design accounting for these thermal movement characteristics ensures reliable long-term performance even in applications with significant temperature variations during normal operation.
Q5: What certifications should industrial buyers look for when purchasing CPVC piping?
Industrial buyers should look for ASTM F441/F441M compliance for CPVC pressure pipes NSF/ANSI 61 certification for potable water applications FM approval for fire protection systems and UL listings where applicable. Additionally manufacturer-specific certifications ISO 9001 quality management systems and industry-specific approvals relevant to your application should be verified before purchase. You should request documentation verifying these certifications directly from suppliers ensuring materials actually meet claimed standards rather than simply accepting catalog claims without verification. Material traceability documentation provides additional assurance regarding manufacturing source production batch and quality testing results particularly important for critical applications where material failure could create significant safety hazards or operational impacts. Some specialized applications require additional certifications such as USP Class VI for pharmaceutical applications or specific fire testing certifications for installations in sensitive facilities. Proper documentation of these certifications belongs in project records providing verification of material compliance during regulatory inspections system modifications or failure investigations throughout system service life.