PVC (Polyvinyl Chloride) is widely used for plumbing due to its affordability and versatility. CPVC (Chlorinated Polyvinyl Chloride) is a stronger variant with enhanced temperature resistance, ideal for hot water applications. ABS (Acrylonitrile Butadiene Styrene) offers impact resistance, making it suitable for drain lines and vents. Other materials like PEX (Cross-linked Polyethylene) provide flexibility and resistance to scale buildup, suitable for both hot and cold water plumbing. Each material has specific strengths tailored to different plumbing needs.
Introduction
Pipe Type Comparison: What Are The Differences Between PVC, CPVC, ABS And Other Pipe Materials? This question frequently arises among facility managers, engineers, and procurement specialists tasked with selecting the optimal piping solution for their projects. The right piping material can significantly impact installation costs, system longevity, maintenance requirements, and overall performance. This article explores the key differences between common piping materials, their specific applications, and the critical factors to consider when making selection decisions for your industrial or commercial projects.
1. Fundamentals of Pipe Materials
Understanding pipe materials begins with recognizing their growing significance in modern construction and industrial applications. Plastic piping systems have revolutionized fluid transport across numerous sectors, offering alternatives to traditional metal options with distinct advantages in corrosion resistance, weight, and installation ease. But here’s the kicker – not all plastic pipes are created equal, and selecting the wrong material can lead to premature system failure, contamination issues, or regulatory non-compliance.
The development history of different pipe materials reflects evolving industry needs and technological capabilities. PVC (polyvinyl chloride) emerged commercially in the 1930s, becoming widely adopted by the 1950s due to its excellent chemical resistance and affordability. CPVC (chlorinated polyvinyl chloride) followed in the mid-1950s, addressing the temperature limitations of standard PVC. ABS (acrylonitrile butadiene styrene) gained popularity in the 1960s for its superior impact resistance in cold environments. Each material evolution responded to specific performance gaps in existing options, creating today’s diverse selection of specialized piping solutions.
Material selection profoundly impacts project success across multiple dimensions. The right pipe material ensures system longevity, minimizes maintenance requirements, maintains fluid purity, and provides appropriate pressure and temperature capabilities. Conversely, improper material selection can result in costly failures, safety hazards, contamination issues, and premature replacement needs. The financial implications extend beyond initial material costs to include installation complexity, maintenance requirements, and expected service life – making informed selection critical for total cost optimization.
Basic classification systems for common pipe materials typically divide them into thermoplastics (which can be repeatedly softened and reformed with heat), thermosets (which permanently set after initial heating), and metals. Within the thermoplastic category fall PVC, CPVC, ABS, PE, PP, PEX, and others – each with distinct molecular structures and performance characteristics. Metal options include copper, stainless steel, carbon steel, and various alloys. Understanding these fundamental categories provides the foundation for more detailed material comparisons and selection decisions.
Pipe Material Category | Examples | Key Characteristics | Typical Applications |
---|---|---|---|
Standard Thermoplastics | PVC, ABS | Moderate temperature resistance, good chemical resistance, economical | Drainage, cold water supply, irrigation |
Enhanced Thermoplastics | CPVC, PEX, PP-R | Higher temperature resistance, expanded chemical compatibility | Hot water systems, industrial processes |
Polyolefins | PE, PP | Excellent chemical resistance, flexibility, fusion joining | Gas distribution, chemical transport |
Composite Systems | PEX-AL-PEX, PP-AL-PP | Thermal stability, reduced expansion, oxygen barrier | Radiant heating, potable water |
Metals | Copper, Steel, Stainless Steel | High strength, temperature resistance, established codes | Steam systems, fire protection, structural applications |
2. PVC Pipe Characteristics and Applications
PVC pipe consists primarily of polyvinyl chloride resin (approximately 86-90%), combined with various stabilizers, lubricants, pigments, and processing aids. The manufacturing process involves mixing these components, heating the compound until molten, and extruding it through dies to create the familiar cylindrical form.
What’s the real story behind PVC’s popularity? Its balanced combination of affordability, chemical resistance, and durability has made it the most widely used plastic piping material globally, accounting for over 40% of all plastic pipe installations.
Physical characteristics of PVC pipe include moderate strength-to-weight ratio, rigidity, and limited flexibility. Standard Schedule 40 PVC weighs approximately 0.17 pounds per inch of diameter per foot, making it roughly one-fifth the weight of comparable steel pipe.
This lightweight nature significantly reduces transportation costs and simplifies installation. PVC offers tensile strength around 7,500 psi and flexural strength of approximately 14,500 psi, providing sufficient rigidity for most non-pressurized and moderate-pressure applications.
The material’s smooth interior surface, with a Hazen-Williams C Factor of 150, maintains excellent flow characteristics throughout its service life, unlike metals that may develop internal roughness over time.
Temperature tolerance represents one of PVC’s primary limitations. Standard PVC maintains its structural integrity and pressure ratings at temperatures up to approximately 140°F (60°C), with recommended continuous operating temperatures below 120°F (49°C). Beyond these thresholds, the material progressively softens, losing pressure-bearing capability and dimensional stability.
This temperature limitation restricts PVC from hot water applications, steam systems, or industrial processes involving elevated temperatures. Cold temperature performance remains adequate for most applications, with impact resistance diminishing somewhat below freezing but generally maintaining structural integrity unless subjected to significant impact forces.
Typical applications for PVC pipe span numerous sectors, with particular dominance in cold water distribution, drainage systems, irrigation networks, and chemical handling. In residential and commercial construction, PVC serves as the standard material for potable water supply lines, DWV (drain-waste-vent) systems, and rainwater management.
Agricultural operations rely heavily on PVC for irrigation systems, fertilizer distribution, and drainage networks. Industrial applications include chemical transfer lines, water treatment systems, and process piping for compatible fluids. Underground utilities frequently utilize PVC for water mains, sewer lines, and electrical conduit protection due to its corrosion resistance and long-term burial stability.
Color coding and size standards for PVC pipe follow established industry conventions that communicate important information about intended applications. White PVC typically indicates plumbing applications, while gray often denotes electrical conduit.
Schedule 40 (white) and Schedule 80 (gray or white) designations reflect wall thickness, with Schedule 80 providing higher pressure ratings and mechanical strength at the cost of reduced internal diameter. Size designations follow nominal dimensions, with actual outside diameters standardized to accommodate consistent fitting compatibility.
Various industry standards govern PVC pipe specifications, including ASTM D1785 for pressure applications, ASTM D2665 for drain and vent applications, and NSF/ANSI 61 for potable water safety.
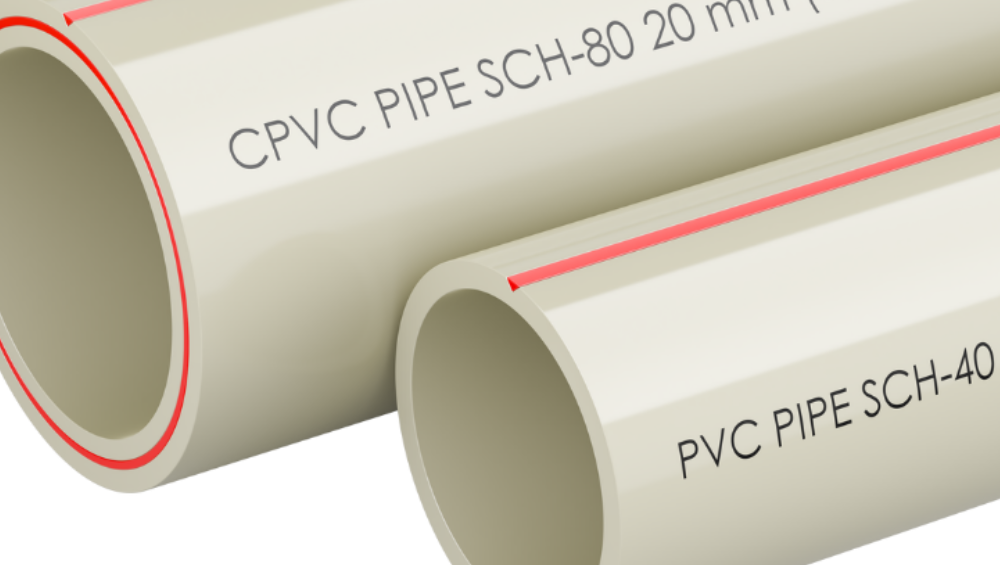
3. CPVC Pipe Characteristics and Applications
CPVC differs from standard PVC through an additional chlorination process that increases the chlorine content from approximately 57% in PVC to around 63-69% in CPVC.
This seemingly minor chemical modification creates significant performance differences by increasing the molecular weight and creating a more complex structure.
Ready for the good part? This structural change elevates the heat distortion temperature from approximately 165°F (74°C) in PVC to around 230°F (110°C) in CPVC, dramatically expanding potential applications into hot water and higher-temperature industrial processes previously unsuitable for standard PVC.
Enhanced heat resistance represents CPVC’s most significant advantage over standard PVC. CPVC maintains pressure-bearing capabilities and dimensional stability at continuous operating temperatures up to 200°F (93°C), compared to PVC’s 140°F (60°C) limitation.
This expanded temperature range opens applications in hot water distribution systems, industrial processes with elevated temperatures, and environments with temperature fluctuations that would compromise standard PVC. The material’s heat resistance derives from the additional chlorine atoms in its molecular structure, which create stronger bonds requiring more thermal energy to disrupt.
Chemical resistance profiles for CPVC exceed even PVC’s impressive capabilities, particularly at elevated temperatures where many materials experience accelerated degradation.
CPVC demonstrates excellent resistance to acids, bases, salts, and many aliphatic hydrocarbons across a broader temperature spectrum than standard PVC. This enhanced chemical stability makes CPVC particularly valuable in industrial applications involving corrosive fluids at moderate temperatures, including chemical processing, water treatment, and semiconductor manufacturing.
The material does share PVC’s vulnerabilities to certain solvents, including ketones, esters, and some chlorinated compounds, requiring careful compatibility verification for specific chemical exposures.
Property | PVC | CPVC | Practical Implications |
---|---|---|---|
Maximum Operating Temperature | 140°F (60°C) | 200°F (93°C) | CPVC suitable for hot water systems |
Chlorine Content | ~57% | 63-69% | Higher chlorine increases temperature resistance |
Heat Distortion Temperature | 165°F (74°C) | 230°F (110°C) | CPVC maintains rigidity at higher temperatures |
Tensile Strength | ~7,500 psi | ~8,000 psi | CPVC slightly stronger under tension |
Chemical Resistance at Elevated Temperatures | Good | Excellent | CPVC superior for hot chemical transport |
Material Cost | Lower | 20-30% higher | PVC more economical when temperature permits |
Pressure ratings for CPVC pipe typically exceed comparable PVC configurations, particularly at elevated temperatures. Standard Schedule 80 CPVC pipe in 1-inch diameter maintains a pressure rating of approximately 630 psi at 73°F (23°C), decreasing to about 270 psi at 180°F (82°C) – still sufficient for most hot water and industrial applications.
This pressure-bearing capability at higher temperatures represents a critical advantage over standard PVC, which experiences more rapid pressure rating degradation as temperatures increase. The superior pressure performance derives from CPVC’s more complex molecular structure and higher glass transition temperature, allowing it to maintain rigidity under conditions that would soften standard PVC.
Service life expectations for properly installed CPVC systems typically range from 30-50 years under appropriate operating conditions.
Factors affecting longevity include operating temperature, chemical exposure, pressure cycling, installation quality, and external environmental conditions. CPVC generally demonstrates excellent aging characteristics, maintaining mechanical properties and chemical resistance throughout its service life without significant degradation when used within specified parameters.
This long-term performance reliability makes CPVC particularly valuable in applications where system replacement creates significant disruption or where consistent performance over decades is essential for operational continuity.
Installation requirements for CPVC closely resemble those for PVC, with some important distinctions related to its unique properties. Both materials utilize solvent cement joining, but CPVC requires specific cement formulations designed for its chemical composition – standard PVC cement creates inferior bonds with potentially catastrophic failure risks.
Expansion accommodation becomes more critical with CPVC due to its higher operating temperatures, requiring appropriate allowances for thermal movement through expansion loops, offsets, or mechanical compensation devices.
Support spacing typically follows similar guidelines to PVC, though higher temperature applications may necessitate slightly closer support intervals to prevent sagging as the material experiences thermal softening within its operating range.
4. ABS Pipe Characteristics and Applications
ABS pipe consists of acrylonitrile, butadiene, and styrene polymers combined in a ratio that typically includes 15-35% acrylonitrile, 5-30% butadiene, and 40-60% styrene, along with various additives for processing, stabilization, and coloration.
This is where it gets interesting – each component contributes specific properties: acrylonitrile provides chemical resistance, butadiene delivers impact strength and flexibility, while styrene contributes rigidity and processability.
The manufacturing process involves polymerizing these monomers, compounding with additives, and extruding the material through dies to form pipes with the characteristic black coloration derived from carbon black, which provides UV resistance.
Physical characteristics of ABS include excellent impact resistance, particularly at lower temperatures where many thermoplastics become brittle. ABS maintains impact strength down to -40°F (-40°C), making it especially valuable in cold climate installations.
The material offers a tensile strength of approximately 6,000 psi – somewhat lower than PVC – but compensates with superior toughness and resistance to cracking under impact or stress. ABS provides a relatively lightweight alternative to metal piping, weighing approximately 0.15 pounds per inch of diameter per foot, facilitating easier handling and installation while reducing structural support requirements compared to traditional materials.
Typical applications for ABS pipe concentrate in areas where its specific performance advantages address critical needs. Residential and light commercial drainage systems represent the most common application, with ABS widely used for DWV (drain-waste-vent) systems, particularly in single-family homes and smaller buildings.
Cold climate installations benefit from ABS’s superior impact resistance at low temperatures, making it preferred for exposed drainage applications in northern regions. Manufactured housing frequently utilizes ABS for plumbing systems due to its impact resistance during transportation and installation.
Marine applications leverage ABS’s combination of chemical resistance and toughness for bilge and sanitation systems. Industrial uses include low-pressure air handling, vacuum systems, and certain chemical drainage applications compatible with ABS’s chemical resistance profile.
Identification features for ABS pipe include its characteristic black color, which distinguishes it from white or gray PVC and cream-colored CPVC. Standard markings printed on the pipe exterior provide essential information including manufacturer, material designation (ABS), applicable standards compliance, size, schedule or dimension ratio, and production date codes.
These markings facilitate proper identification for regulatory compliance, appropriate application, and compatibility with fittings and joining methods. The material’s glossy surface finish also helps distinguish it from other black pipes such as polyethylene, which typically exhibits a more matte appearance.
Key differences between ABS and PVC/CPVC extend beyond appearance to include several performance characteristics. ABS offers superior impact resistance but lower tensile strength compared to both PVC and CPVC. Temperature resistance falls between standard PVC and CPVC, with ABS maintaining structural integrity to approximately 160°F (71°C) – higher than PVC’s 140°F (60°C) but below CPVC’s 200°F (93°C).
Chemical resistance profiles differ significantly, with ABS showing better resistance to certain bases and fatty acids but greater vulnerability to many solvents that PVC and CPVC tolerate well. Installation methods also differ, with ABS utilizing a one-step solvent welding process compared to the primer-plus-cement approach typically recommended for PVC and CPVC.
These distinctions make each material optimal for specific applications rather than universally superior or inferior.
5. Analysis of Other Common Plastic Pipe Types
Polyethylene (PE) pipe has evolved through multiple generations, with current high-density polyethylene (HDPE) and cross-linked polyethylene (PEX) variants dominating modern applications.
What’s the real story behind PE’s growing popularity? Its exceptional flexibility, chemical resistance, and fusion-joining capabilities make it ideal for applications requiring long continuous runs, resistance to ground movement, and leak-free connections.
HDPE offers excellent chemical resistance against acids, bases, and many organic compounds, while maintaining flexibility even at temperatures approaching freezing. The material’s typical applications include water and gas distribution networks, landfill leachate collection, mining slurry transport, and geothermal ground loops.
PE’s limitations include lower temperature resistance than CPVC (typically limited to 140°F/60°C for standard HDPE) and lower pressure ratings at elevated temperatures compared to more rigid materials.
Polypropylene (PP) pipe provides exceptional chemical resistance, particularly against aggressive acids, bases, and chemical compounds that might attack other materials.
Modern PP piping systems utilize random copolymer (PP-R) or polypropylene-random crystallinity temperature (PP-RCT) formulations that enhance temperature resistance and long-term strength.
PP demonstrates excellent resistance to chemical transport, maintaining structural integrity when exposed to many industrial chemicals, acids, and bases that would degrade alternative materials. Common applications include chemical processing facilities, semiconductor manufacturing, food and beverage production, and high-purity water systems.
PP systems typically employ heat fusion joining methods (socket fusion, butt fusion, or electrofusion) that create homogeneous connections without adhesives or mechanical components, eliminating potential leak paths and chemical compatibility concerns at joints.
PEX (cross-linked polyethylene) pipe has revolutionized residential and commercial plumbing since its North American introduction in the 1980s.
The cross-linking process creates permanent bonds between polyethylene molecular chains, dramatically improving temperature resistance, chemical stability, and long-term strength compared to standard polyethylene.
Three manufacturing methods produce slightly different variants: PEX-A (peroxide method), PEX-B (silane method), and PEX-C (electron beam method), each with subtle performance differences. PEX’s exceptional flexibility allows it to bend around obstacles without fittings, significantly reducing potential leak points while simplifying installation in confined spaces.
The material’s thermal memory allows it to expand when frozen without bursting, then return to its original dimensions when thawed – a critical advantage in freeze-prone applications. Primary applications include residential and commercial hot/cold water distribution, radiant floor heating, snow melting systems, and district heating networks.
Pipe Type | Temperature Range | Chemical Resistance | Joining Method | Key Applications | Relative Cost |
---|---|---|---|---|---|
PE (HDPE) | -40°F to 140°F (-40°C to 60°C) | Excellent against acids, bases; poor against hydrocarbons | Butt fusion, electrofusion, mechanical | Water/gas distribution, drainage, mining | Low |
PP | 32°F to 180°F (0°C to 82°C) | Superior against most chemicals including acids, bases, solvents | Heat fusion, electrofusion | Chemical processing, high-purity systems | Medium-High |
PEX | -40°F to 200°F (-40°C to 93°C) | Good against many chemicals; poor against chlorine at high temps | Expansion fittings, compression, crimp rings | Potable water, radiant heating | Medium |
PB | 32°F to 200°F (0°C to 93°C) | Good against acids, bases; poor against chlorine, UV | Compression, heat fusion | Potable water (limited use due to failures) | High |
PVDF | -40°F to 280°F (-40°C to 138°C) | Exceptional against most chemicals including strong acids | Heat fusion, threaded, flanged | Semiconductor, pharmaceutical, chemical | Very High |
Polybutylene (PB) pipe gained popularity in residential plumbing from the 1970s through early 1990s before widespread failure issues led to its virtual disappearance from the North American market.
The material offered excellent flexibility, freeze resistance, and simple installation, but experienced catastrophic degradation when exposed to chlorinated water under typical domestic conditions.
This cautionary case demonstrates the importance of long-term testing under actual usage conditions before widespread adoption of new piping materials. While PB remains available in some international markets with modified formulations, its North American applications have been largely replaced by PEX, which offers similar benefits without the degradation concerns.
Composite piping systems combine multiple materials to leverage their complementary properties while mitigating individual limitations.
Common configurations include aluminum-plastic composites (PEX-AL-PEX or PP-AL-PP) that sandwich a thin aluminum layer between inner and outer plastic layers. This structure provides the chemical resistance and potable water compatibility of the plastic with the reduced thermal expansion, oxygen barrier properties, and shape retention of aluminum.
The aluminum layer also enables heat transfer for applications like radiant heating while preventing oxygen permeation that could damage system components. These composite systems find applications in radiant heating, potable water distribution, compressed air systems, and specialized industrial applications where their unique combination of properties addresses specific performance requirements not met by single-material solutions.
6. Comparison Between Metal and Plastic Pipes
Copper piping has served as the gold standard for residential and commercial plumbing for generations, offering a proven track record of reliability and performance.
But here’s the kicker – while copper provides excellent heat transfer, bacteriostatic properties, and resistance to UV degradation, its significantly higher material cost and vulnerability to both external and internal corrosion under certain conditions have increasingly pushed the market toward plastic alternatives.
Copper’s advantages include exceptional heat conductivity (making it ideal for heat transfer applications), natural antimicrobial properties that inhibit bacterial growth, and established installation methods familiar to most plumbing professionals.
The material handles continuous operating temperatures up to 400°F (204°C), making it suitable for steam and high-temperature applications beyond plastic capabilities. However, copper remains vulnerable to erosion-corrosion in high-velocity applications, pinhole leaks in aggressive water conditions, and external corrosion when exposed to certain soils or building materials.
Stainless steel piping offers unmatched corrosion resistance, temperature tolerance, and pressure-bearing capability among commonly available piping materials.
Various alloys provide specialized performance characteristics, with Type 304 (containing approximately 18% chromium and 8% nickel) serving general applications and Type 316 (with added molybdenum) providing enhanced resistance to chloride environments.
Stainless steel maintains structural integrity at temperatures exceeding 800°F (427°C), making it suitable for steam, high-temperature process fluids, and fire protection systems. The material’s exceptional strength allows thin-wall designs that partially offset its weight disadvantage compared to plastic alternatives. Primary applications include food and beverage processing, pharmaceutical manufacturing, chemical processing, and marine environments where its corrosion resistance justifies the premium cost.
Limitations include high material and installation costs, susceptibility to chloride stress corrosion cracking in certain environments, and potential for galvanic corrosion when connected to dissimilar metals without appropriate isolation.
Galvanized steel pipe, consisting of carbon steel with a protective zinc coating, once dominated water supply applications but has largely been replaced by more corrosion-resistant alternatives in new construction. The zinc coating provides temporary protection against corrosion, but inevitably deteriorates over time – particularly when exposed to acidic or mineral-laden water.
As the coating degrades, internal corrosion accelerates, leading to flow restriction from mineral buildup, water discoloration, and eventually pipe failure. Despite these limitations, galvanized steel remains common in fire sprinkler systems, natural gas distribution, and certain industrial compressed air applications where its strength, fire resistance, and established code acceptance outweigh corrosion concerns.
The material’s primary advantages include mechanical strength, rigidity, and fire resistance, while its disadvantages encompass corrosion vulnerability, weight, and labor-intensive installation requiring threading or welding connections.
Cost comparison between metal and plastic piping systems extends beyond simple material pricing to include installation labor, maintenance requirements, and expected service life.
Material costs typically show dramatic differences, with plastic options generally ranging from 20-80% lower than comparable metal systems depending on specific materials and current market conditions. Installation costs often reveal even greater disparities due to plastic’s lighter weight, simpler joining methods, and reduced equipment requirements.
A typical commercial installation might require 40-60% fewer labor hours for plastic systems compared to welded metal piping of equivalent size. Maintenance expenses over system lifetime typically favor plastic options, which eliminate concerns about internal corrosion, external painting, and many chemical treatment requirements common with metal systems.
However, certain specialized applications may justify metal’s premium cost through superior performance characteristics, regulatory compliance, or specific property requirements not adequately addressed by plastic alternatives.
Lifespan and maintenance requirements vary significantly between metal and plastic piping systems, influenced by material selection, installation quality, operating conditions, and environmental factors.
Properly installed copper systems in favorable conditions can exceed 50 years of service, while stainless steel may deliver 75+ years in appropriate applications. High-quality plastic systems typically offer 30-50 year expected lifespans, with actual performance often exceeding these conservative estimates in non-demanding applications. Maintenance requirements generally favor plastic systems, which eliminate concerns about corrosion monitoring, protective coating maintenance, and chemical treatment programs often necessary with metal piping.
However, plastic systems require appropriate consideration for thermal expansion, UV protection for exposed installations, and compatibility verification for chemical exposures. The optimal material selection balances these longevity and maintenance factors against initial costs, performance requirements, and application-specific considerations rather than defaulting to either material category.
7. Key Considerations for Pipe Material Selection
Application environment represents the foundational consideration in pipe material selection, encompassing temperature exposure, pressure requirements, and chemical compatibility.
This is where it gets interesting – even the most premium piping material will fail prematurely if mismatched to its operating environment. Temperature considerations must address both continuous operating conditions and potential excursions during abnormal situations, with appropriate safety margins applied to maximum ratings.
Pressure requirements similarly demand careful analysis of normal operating pressures, potential surge conditions, and long-term pressure cycling effects that might cause fatigue failure.
Chemical exposure evaluation must consider not only primary process fluids but also cleaning agents, maintenance chemicals, and potential contaminants that might occasionally contact the piping system. Environmental factors including UV exposure, burial conditions, potential physical damage, and fire safety requirements further influence material suitability for specific applications.
Installation complexity and required technical expertise vary dramatically between piping materials, significantly impacting project timelines, labor costs, and quality assurance requirements.
Long-term cost and maintenance considerations often reveal significant differences between initially similar options when evaluated across the system’s entire lifecycle. Initial material and installation costs represent only the beginning of the economic analysis, with maintenance requirements, energy efficiency, replacement frequency, and operational impacts providing a more complete picture of total ownership costs.
Plastic systems typically offer advantages in corrosion resistance, eliminating expensive monitoring programs, protective treatments, and premature replacement due to internal or external degradation. Metal systems may provide superior mechanical protection, fire resistance, and established code acceptance that simplifies approval processes.
Energy efficiency considerations include thermal conductivity for insulated systems, friction losses affecting pumping costs, and heat transfer characteristics for temperature-critical applications. These long-term economic factors often justify premium material selection when properly quantified against lower-cost alternatives with shorter service lives or higher maintenance requirements.
Selection Factor | PVC | CPVC | ABS | PE | Copper | Stainless Steel |
---|---|---|---|---|---|---|
Maximum Temperature | 140°F (60°C) | 200°F (93°C) | 160°F (71°C) | 140°F (60°C) | 400°F+ (204°C+) | 800°F+ (427°C+) |
Chemical Resistance | Very Good | Excellent | Good | Excellent | Moderate | Very Good |
Installation Complexity | Low | Low | Low | Medium | High | Very High |
Material Cost | Low | Medium | Low | Low | High | Very High |
Expected Service Life | 30-50 years | 30-50 years | 30-50 years | 50+ years | 50+ years | 75+ years |
Pressure Capability | Moderate | Moderate | Low | Moderate | High | Very High |
Fire Resistance | Poor | Moderate | Poor | Poor | Excellent | Excellent |
UV Resistance | Poor | Poor | Moderate | Poor | Excellent | Excellent |
8. Connection Methods for Different Pipe Materials
Solvent cementing represents the predominant joining method for PVC, CPVC, and ABS piping systems, creating chemical bonds that effectively fuse the pipe and fitting into a single continuous unit. Ready for the good part?
When properly executed, solvent-cemented joints actually exceed the strength of the pipe itself, with failure testing typically resulting in pipe fracture rather than joint separation. The process involves applying chemical solvents that temporarily soften the plastic surfaces, allowing polymer chains to intermingle before the solvent evaporates, leaving a homogeneous connection.
PVC and CPVC systems typically require a two-step process with primer application followed by solvent cement, while ABS utilizes a one-step cement that combines these functions. Critical factors affecting joint quality include proper pipe cutting (square ends without burrs), appropriate surface preparation, cement selection matched to pipe material and size, ambient temperature and humidity conditions, and adequate cure time before pressure testing.
Common installation errors include insufficient cement application, improper insertion depth, excessive force causing cement displacement, and inadequate cure time – all potentially resulting in joint failure under pressure.
Heat fusion joining methods create molecular bonds between thermoplastic materials through controlled heating and pressure application, resulting in connections as strong as the original pipe.
Three primary variations include socket fusion (pipe end and fitting heated separately then joined), butt fusion (pipe ends heated and pressed together without fittings), and electrofusion (embedded electrical resistance elements heat the joint from within). These methods predominate in polyethylene (PE) and polypropylene (PP) systems, with growing applications in specialized PEX and PVDF installations. The fusion process creates homogeneous connections without adhesives, gaskets, or mechanical components that might otherwise limit chemical compatibility or create potential leak paths.
Critical parameters include surface preparation, heating temperature, heating duration, cooling time, and applied pressure – all requiring careful control through trained personnel and often specialized equipment.
The resulting joints offer exceptional strength, complete leakproofness, and chemical resistance identical to the parent pipe, making fusion methods particularly valuable for critical applications including gas distribution, chemical transport, and high-purity systems.
Mechanical connection systems encompass numerous designs utilizing compression forces, elastomeric seals, or mechanical interlocks to create pressure-tight joints without chemical bonding or heat application.
Common variations include compression fittings, push-to-connect systems, grooved couplings, flanged connections, and various proprietary designs specific to particular piping materials. These systems offer several advantages including immediate pressure capability without cure time, disassembly potential for maintenance or modification, and suitability for joining dissimilar materials.
Limitations typically include higher material costs, potential leak paths at sealing surfaces, and maintenance requirements for systems utilizing elastomeric components that may degrade over time. Application suitability varies by specific design, with some mechanical systems approved for direct burial while others require accessibility for periodic inspection and maintenance.
Selection factors include pressure requirements, temperature exposure, chemical compatibility of sealing components, code acceptance for specific applications, and installation space constraints.
Threaded connections, created by cutting standardized helical threads onto pipe ends and fittings, remain common for metal piping and limited plastic applications despite inherent limitations.
Comparative advantages and disadvantages between connection methods highlight the importance of selecting appropriate joining techniques for specific applications and materials.
Solvent cementing offers permanent, strong connections with excellent chemical resistance but requires cure time before pressure application and creates permanent connections not easily modified. Heat fusion provides the strongest possible joints with identical chemical resistance to the parent pipe but requires specialized equipment, trained personnel, and longer installation time.
Mechanical connections allow immediate pressure capability and future disassembly but introduce potential leak paths, maintenance requirements, and material compatibility considerations for sealing elements. Threaded connections provide universal compatibility and simple installation but reduce pressure ratings, create stress concentration points, and require sealants that may limit chemical compatibility.
The optimal connection method balances these factors against specific application requirements including pressure, temperature, chemical exposure, code compliance, maintenance needs, and installation constraints rather than defaulting to a single approach across all situations.
9. Durability and Lifespan Analysis of Pipe Materials
Expected service life under various conditions represents a critical consideration in piping material selection, particularly for infrastructure applications where replacement creates significant disruption and expense.
This is where it gets interesting – while manufacturers typically provide conservative warranty periods of 5-10 years, properly selected and installed piping systems routinely deliver service lives measured in decades. PVC, CPVC, and ABS systems in non-demanding applications commonly exceed 50 years of functional service, with actual replacement more often driven by capacity changes or renovation requirements than material failure.
Polyethylene systems demonstrate similar longevity, with modern PE100 materials engineered for 100-year service life in water distribution applications.
Metal systems show greater variability, with copper potentially lasting 50+ years in favorable water chemistry but experiencing premature pinhole leaking in aggressive conditions. Stainless steel offers exceptional longevity, potentially exceeding 75 years when properly specified for its environment.
These projections assume appropriate material selection for operating conditions, proper installation practices, and absence of unexpected chemical exposure or physical damage during service.
Maintenance strategies to extend piping system lifespan focus on preventing or mitigating the specific degradation mechanisms relevant to installed materials.
Water treatment programs address internal corrosion and scaling in metal systems through pH adjustment, oxygen scavengers, corrosion inhibitors, and scale control chemicals tailored to specific water chemistry and metallurgy.
Cathodic protection systems mitigate external corrosion on buried metal piping through impressed current or sacrificial anodes that alter electrochemical reactions. Protective coatings and wrappings provide physical barriers against external corrosion, UV degradation, and physical damage for both metal and plastic systems in challenging environments.
Regular inspection programs identify developing issues before they cause failure, with techniques including visual examination, ultrasonic thickness measurement, radiographic testing, and various specialized methods for specific degradation concerns.
Operational practices including proper startup procedures, controlled temperature and pressure conditions, minimized water hammer effects, and appropriate chemical handling further contribute to maximized service life across all piping materials.
Pipe Material | Expected Service Life | Primary Degradation Mechanisms | Maintenance Requirements | End-of-Life Indicators |
---|---|---|---|---|
PVC | 30-50+ years | UV degradation, chemical attack, physical damage | Minimal; protect from UV if exposed | Discoloration, brittleness, stress cracking |
CPVC | 30-50+ years | Oxidation at high temps, chemical attack | Minimal; verify temperature limits | Discoloration, reduced impact strength |
ABS | 30-50+ years | UV degradation, certain chemical exposures | Minimal; protect from UV if exposed | Surface chalking, impact failure |
PE | 50-100+ years | Oxidation, stress cracking, UV degradation | Minimal; proper installation critical | Stress cracking, reduced flexibility |
Copper | 25-70+ years | Pitting, erosion-corrosion, pinhole leaks | Water chemistry management | Green staining, pinhole leaks |
Stainless Steel | 50-75+ years | Chloride stress corrosion, pitting | Minimal; avoid chloride concentration | Rust staining, localized pitting |
Carbon Steel | 15-40+ years | General corrosion, localized attack | Corrosion monitoring, water treatment | Wall thinning, tuberculation, leaks |
Conclusion
Pipe Type Comparison: What Are The Differences Between PVC, CPVC, ABS And Other Pipe Materials? As we’ve explored throughout this article, each piping material offers distinct advantages and limitations that make it optimally suited for specific applications rather than universally superior.
The key to successful system design lies in understanding these material-specific characteristics and matching them appropriately to application requirements including temperature, pressure, chemical exposure, and environmental conditions. Proper material selection, combined with appropriate installation techniques and maintenance practices, ensures optimal performance, longevity, and value across the system’s entire lifecycle.
When evaluating options for your next piping project, consider not only initial costs but also long-term performance, maintenance requirements, and expected service life to identify the truly optimal solution for your specific needs.
FAQ
Q1: What is the main difference between PVC and CPVC piping?
PVC (polyvinyl chloride) and CPVC (chlorinated polyvinyl chloride) differ primarily in their temperature resistance and chemical structure. CPVC undergoes additional chlorination, increasing its chlorine content from approximately 57% to 63-69%, which raises its maximum operating temperature from 140°F (60°C) for PVC to 200°F (93°C) for CPVC. This makes CPVC suitable for hot water applications where standard PVC would fail. CPVC also offers enhanced chemical resistance at elevated temperatures, though it typically costs 20-30% more than standard PVC.
Q2: How can you correctly identify different types of plastic pipes?
Different plastic pipe types can be identified through several methods: color (PVC is typically white or gray, CPVC is cream/light yellow, ABS is black), printed markings on the pipe (containing material type, specifications, pressure ratings, and manufacturing information), physical characteristics (rigidity, flexibility), and flame testing (different plastics burn with characteristic flames and odors). The most reliable method is checking the identification code printed on the pipe, such as “PVC-U” (unplasticized PVC), “CPVC,” or “ABS.” For installed unmarked pipes, professional identification kits or consulting with plumbing specialists may be necessary.
Q3: Which pipe material is best for residential drainage systems?
For residential drainage systems, both PVC and ABS perform well, with selection often depending on local building codes, climate conditions, and installer preference. ABS offers better impact resistance, especially in cold temperatures, and requires only a one-step cementing process. PVC provides better flame resistance, produces less smoke when burned, and typically has more available fittings and accessories. In colder climates, ABS may be preferred for its superior impact resistance at low temperatures, while in areas with stricter fire codes, PVC might be favored. Always verify local code requirements, as some jurisdictions specifically require one material over the other.
Q4: How do temperature fluctuations affect different piping materials?
Temperature fluctuations cause all piping materials to expand and contract, but at different rates. Plastic pipes generally have higher thermal expansion coefficients than metals – PVC expands approximately 3 times more than copper and 5 times more than steel for the same temperature change. This expansion must be accommodated through proper installation techniques including expansion loops, offsets, or mechanical expansion joints. CPVC and PEX maintain flexibility at higher temperatures than PVC, while metals like copper and steel offer more dimensional stability but can transfer heat more readily, potentially increasing energy loss or condensation issues.
Q5: What factors should be considered when selecting pipe materials for industrial applications?
When selecting pipe materials for industrial applications, consider: operating temperature range (both normal and potential excursions), pressure requirements (including surge conditions), chemical compatibility with process fluids and cleaning agents, mechanical strength needs, installation environment (indoor/outdoor, buried/exposed), code compliance requirements, connection methods, maintenance access, expected service life, and total lifecycle costs. For critical applications, also evaluate fire resistance, electrical conductivity, and potential contamination concerns. Consulting manufacturer chemical resistance guides, relevant industry standards, and experienced engineers is essential for making optimal selections in complex industrial environments.