Choosing the right rubber for your projects is crucial, especially when comparing materials like chlorosulfonated polyethylene (CSM) and neoprene. This article dives deep into the intricate differences between these two popular types of rubber, exploring their essential characteristics, applications, durability, costs, and environmental impacts. The objective is to help industry professionals make informed decisions when selecting the best rubber material for their specific needs.
1. Introduction to Chlorosulfonated Polyethylene and Neoprene
What’s the real story? When it comes to rubber, chlorosulfonated polyethylene and neoprene stand out as two of the most widely used synthetic materials in various industries. CSM is a type of synthetic rubber known for its unique ability to withstand tough environments, including high temperatures and exposure to chemicals. This durability makes it suitable for applications in sectors like automotive and construction. On the other hand, neoprene is celebrated for its versatility, elasticity, and resistance to weathering, making it a go-to choice for products ranging from wetsuits to seals.
As industries continue to develop and evolve, the demand for specialized materials that can withstand stressful conditions has never been higher. Both CSM and neoprene have carved out distinct niches in the market. However, understanding their unique attributes and respective advantages is essential for anyone tasked with selecting a material for a project.
In this article, we will compare these two types of rubber across various parameters, including their chemical compositions, physical properties, cost implications, and sustainability factors. By the end of this comprehensive analysis, readers will be well-equipped to determine which material best fits their specific needs, ultimately leading to more successful project outcomes.
Characteristic | Chlorosulfonated Polyethylene (CSM) | Neoprene |
---|---|---|
Composition | Chlorinated and sulfonated polymer | Polychloroprene |
Primary Uses | Automotive seals, roofing membranes | Wetsuits, insulation, gaskets |
2. Key Characteristics of Chlorosulfonated Polyethylene (CSM)
Let’s take a closer look at what makes chlorosulfonated polyethylene unique. CSM boasts a remarkable combination of physical and chemical properties that make it particularly advantageous for many applications. First and foremost, CSM is known for its chemical resistance. It withstands exposure to oils, ozone, and various weather conditions, allowing it to maintain its structural integrity even in demanding environments.
Another standout quality is its thermal stability. CSM performs exceptionally well in both high and low temperatures. This flexibility in temperature tolerance enables its usage in automotive applications, equipment exposed to fluctuating climates, and roofing materials designed to withstand harsh weather.If you want to know why CSM thrives in harsh environments, see”Why CSM’s UV & Weather Resistance Make It Ideal for Outdoor Use”. For instance, a study showed that CSM compounds maintained their properties when subjected to temperatures exceeding 120 degrees Celsius, a testament to their robustness.
Flexibility is yet another key feature of CSM. Despite its strength, CSM remains flexible, allowing it to be molded into complex shapes and structures. This versatility makes it a popular choice for seals and gaskets that require tight fitting and durability.
Lastly, environmental resistance against ultraviolet light is a critical property of CSM. Materials exposed to the outdoors benefit significantly from this feature. It doesn’t degrade under UV light, ensuring longevity and performance, particularly in applications like roofing and exterior coatings.
CSM Properties | Description | Applications |
---|---|---|
Chemical Resistance | Resists oils, ozone, and environmental stress | Automotive parts, industrial seals |
Thermal Stability | Effective within extreme temperature ranges | Automotive, HVAC, and roofing applications |
Flexibility | Maintains shape and adaptability | Seals, gaskets, and flexible hoses |
UV Resistance | Prevents degradation from sunlight | Outdoor membranes and coatings |
3. Key Characteristics of Neoprene Rubber
Now, let’s dive into the key characteristics of neoprene. Neoprene, also known as polychloroprene, is a versatile synthetic rubber that has been widely adopted in a variety of industries due to its unique properties. One of the most significant benefits of neoprene is its excellent elasticity. This characteristic allows it to return to its original shape even after being stretched or compressed. It’s precisely this elasticity that makes neoprene a popular choice for wetsuits, which require flexibility and comfort.
What’s more impressive? Neoprene also exhibits outstanding resistance to heat. It can endure elevated temperatures without compromising its structural integrity, making it ideal for applications that experience consistent warmth, such as in automotive or industrial settings. In fact, neoprene can typically withstand temperature ranges from -40 degrees Celsius to 120 degrees Celsius, a quality that enhances its suitability across various sectors.
Another essential quality of neoprene is its moisture resistance. This property not only makes neoprene an excellent candidate for wet environments, such as marine and swimming applications, but also aids in thermal insulation. Neoprene is widely used in the production of insulating materials, preventing heat loss or gain in buildings, appliances, or automotive components.
Lastly, neoprene provides a certain degree of chemical resistance, able to withstand exposure to some aliphatic hydrocarbons, oils, and oxidizing agents. However, it is worth noting that while neoprene has decent resistance to chemicals, it does not stand up as well against certain solvents when compared to CSM.
Neoprene Properties | Description | Applications |
---|---|---|
Elasticity | High flexibility and recovery | Wetsuits, sports equipment |
Heat Resistance | Capable of withstanding elevated temperatures | Automotive seals and gaskets |
Moisture Resistance | Effective barrier against water | Insulation in various industries |
Chemical Resistance | Resists certain acids and oils | Industrial applications |
4. Comparative Durability Between CSM and Neoprene
When it comes to durability, understanding how CSM and neoprene hold up under stress is critical. This is where it gets interesting… Chlorosulfonated polyethylene generally outperforms neoprene concerning longevity in harsh conditions. One notable aspect is its superior chemical resistance, which allows CSM to be used in aggressive environments without deteriorating over time. For example, CSM is frequently utilized in seals and hoses that come into contact with various chemicals and oils within automotive systems.For a more detailed look at its chemical durability, refer to CSM Chemical Resistance: The Clear Advantage Over Other Elastomers.
On the flip side, neoprene’s durability varies depending on its specific formulation. While it offers excellent flexibility and moisture resistance, it may be more susceptible to degradation from UV light exposure and certain chemicals, particularly solvents. This limitation can impact its lifespan in applications such as roofing or outdoor equipment unless additional protective measures are taken.
Moreover, CSM compounds maintain their structures and perform exceptionally well even at the extreme ends of the temperature spectrum. In contrast, neoprene, while heat-resistant, forms a higher risk of thermal degradation at elevated temperatures over extended durations. This factor is particularly crucial in high-stress environments like propulsion systems where heat build-up can be a concern.
Both materials also react differently to physical stress. CSM’s flexibility and resilience provide better performance under continuous flexing or bending, whereas neoprene may lose its elasticity over time if constantly subjected to such conditions. Manufacturers need to factor in these durability differences when selecting materials for specific applications.
Material | Durability Characteristics | Ideal Use Cases |
---|---|---|
Chlorosulfonated Polyethylene (CSM) | Superior chemical & UV resistance | Automotive seals, industrial applications |
Neoprene | Good flexibility; may not withstand UV as well | Wetsuits, insulation, gaskets |
5. Applications of Chlorosulfonated Polyethylene
Let’s explore where chlorosulfonated polyethylene truly shines. What are its most frequent applications? CSM is widely used in sectors such as automotive, construction, and manufacturing due to its unique properties. One of the most significant applications is in automotive seals and gaskets. CSM’s exceptional durability, chemical resistance, and ability to maintain integrity under various conditions make it a top choice for critical components that prevent leaks.
In the construction industry, CSM is often employed in roofing membranes. Its UV and chemical resistance allow it to provide reliable, long-lasting protection from weather elements, ultimately leading to reduced maintenance needs and repairs. In fact, many modern commercial buildings utilize CSM roofing systems for their durability, significantly extending their expected lifespan compared to traditional materials.Learn how CSM supports performance in multiple industries in”How CSM Polymer Applications Span Roofing to Cables”.
Another area where CSM finds its application is within the industrial sector, particularly in the fabrication of hoses, tubing, and various belting materials. Its reliability in high-pressure scenarios ensures that industries relying on fluid transfer can count on the performance of CSM products.
Moreover, CSM is increasingly being integrated into coatings and adhesives as well. Its properties allow for high-performance solutions in environments that experience harsh conditions. Companies that adopt CSM products often notice improved efficiency and reduced failure rates, contributing to operational success.
Application | Description | Advantages |
---|---|---|
Automotive Seals | Used in preventing leaks | Chemical and temperature resistance |
Roofing Membranes | Provides weather protection | Long lifespan, minimal maintenance |
Industrial Hoses | High-pressure fluid transfer | Robust and durable |
6. Applications of Neoprene Rubber
Now, let’s shift our focus to neoprene. What are its most outstanding applications? Neoprene rubber is used across various industries, primarily due to its flexibility and electrical resistance properties. One of the most popular applications is in the production of wetsuits. Neoprene’s excellent elasticity provides warmth and comfort while allowing freedom of movement, making it essential for surfers, divers, and water sports enthusiasts.
Neoprene is also widely used in sports equipment, where protective padding and cushioning are required. From knee braces to gloves, its inherent cushioning properties help absorb shocks while offering durability. Additionally, neoprene is often utilized as an insulation material in industries requiring thermal barriers. It is not uncommon to find neoprene insulation in refrigeration and HVAC systems, ensuring efficient thermal management.
Moreover, neoprene is commonly used for gaskets and seals across numerous applications. Its moisture resistance makes it a favorable choice in plumbing systems and metal equipment that require reliable sealing against water and essentially other substances.
Not only that, neoprene is often selected for manufacturing automotive components such as engine mounts and vibration dampening materials. This role emphasizes its ability to absorb shocks and vibrations, which enhances the performance of vehicles under difficult operating conditions.
Application | Description | Advantages |
---|---|---|
Wetsuits | Thermal protection for water sports | Flexibility and comfort |
Sports Equipment | Padding for impact resistance | Shock absorption and durability |
Insulation | Used in HVAC and refrigeration systems | Effective thermal management |
7. Cost Comparison: CSM and Neoprene
What about the financial implications of selecting one material over the other? Cost analysis is a critical factor in decision-making when choosing between chlorosulfonated polyethylene and neoprene rubber. Generally speaking, chlorosulfonated polyethylene is more expensive than neoprene due to the complexity of its formulation and manufacturing process.
However, it is essential to consider the total cost of ownership when assessing value. While neoprene may have lower initial costs, its potential limitations in durability might result in higher replacement costs and maintenance expenses over time. For example, products made from neoprene could require more frequent replacements if used in chemical or extreme temperature applications. In contrast, CSM’s longevity and reliability could lead to less frequent need for replacement, ultimately saving money in the long run.
A good example would be in the automotive industry, where initial investments in CSM seals may seem steep compared to their neoprene counterparts. However, the reduced need for replacements and repairs from leaks could easily negate that initial expenditure.
When investigating cost, it’s also crucial to factor in performance expectations. The right choice should balance upfront costs with long-term potential savings. In sectors where performance and reliability are paramount, CSM may prove to be a wise investment, while neoprene might be suitable for applications where performance isn’t as critical.
Cost Factors | Chlorosulfonated Polyethylene (CSM) | Neoprene |
---|---|---|
Initial Material Cost | Higher initial investment | Lower initial investment |
Lifespan and Replacement Costs | Longer lifespan and less frequent replacements | May require more frequent replacements |
Overall Value | Higher ROI due to less maintenance | Lower upfront costs, but potentially higher lifecycle costs |
8. Environmental Impact of CSM vs Neoprene
The sustainability factor is becoming increasingly vital in material selection. Ready for the good part? Evaluating the environmental impact of chlorosulfonated polyethylene and neoprene is essential for companies seeking to improve their sustainability metrics.
Chlorosulfonated polyethylene is known for its longevity and resistance to environmental factors, which can reduce waste and the need for replacements. Additionally, some manufacturers are developing CSM from bio-based materials, contributing to greener product offerings. However, traditional CSM production processes can have a significant environmental footprint, so understanding the manufacturing practices of suppliers is crucial.
On the other hand, neoprene has gained criticism for its production because it often relies on petroleum-based resources. While neoprene provides benefits in terms of longevity and performance, its raw material sourcing should be carefully considered. However, there are newer eco-friendly formulations on the market that use recycled materials, which can significantly reduce its environmental impact.
Both materials also must conform to various regulations regarding waste management and chemical disposal, especially when used in industries like manufacturing or automotive. Choosing suppliers that follow sustainable practices can enhance a company’s overall environmental stance and contribute to corporate responsibility initiatives.
When comparing these two materials, understanding the source and production methods will allow industries to make informed choices about environmental responsibility while maintaining necessary performance standards.
Environmental Factors | Chlorosulfonated Polyethylene (CSM) | Neoprene |
---|---|---|
Environmental Footprint | Can be high, although bio-based options exist | Traditionally high due to petroleum reliance |
Waste Management | Durable, reducing waste | Concerns regarding disposal and recycling |
Sustainable Practices | Varies by manufacturer | New eco-friendly options are emerging |
9. Performance in Extreme Conditions
So how do CSM and neoprene fare under extreme conditions? That’s where it gets interesting. When examining performance in high-stress situations, chlorosulfonated polyethylene consistently demonstrates superb resilience. Its robustness in environments that deal with extreme heat, cold, and chemical exposure allows it to serve as a reliable choice in applications like automotive seals where daily wear and tear is prevalent.
When subjecting CSM to temperature extremes, studies show that samples maintain consistent physical properties, which is paramount for any material expected to undergo significant temperature fluctuations. This is particularly relevant in sectors dealing with machinery or processes that experience rapid heating and cooling cycles.
Neoprene, while also possessing a degree of thermal stability, may exhibit some limitations at high temperatures, especially beyond its recommended usage range. In intense heat, neoprene can begin to decompose, becoming less effective over time. This performance drop-off may become a critical issue in certain applications, especially in the automotive or chemical sectors, where materials are frequently exposed to elevated temperatures or aggressive conditions.
Moreover, the moisture resistance of neoprene makes it appropriate for wet environments. However, it doesn’t withstand UV exposure as well as CSM does, making it less suitable for outdoor applications where sun exposure is routine.
Both materials can handle pressure reasonably well, but it’s critical to assess the specific application requirements when making a selection. In projects requiring durability under various extreme conditions, CSM often has the edge over neoprene.
Condition | Chlorosulfonated Polyethylene (CSM) | Neoprene |
---|---|---|
High Temperature Performance | Excellent thermal stability | Limited performance at elevated temps |
Low-Temperature Performance | Retains flexibility | Maintains flexibility but less durable under freezing |
Moisture Resistance | Good, but not as effective as neoprene | Excellent moisture barrier |
10. Customization and Formulation of CSM and Neoprene
Customization can make a significant difference in performance. But here’s the kicker: both CSM and neoprene can be formulated to meet specific project requirements. The ability to customize these materials allows manufacturers to enhance properties such as elasticity, strength, and thermal resistance according to their end-use applications.
For chlorosulfonated polyethylene, additives and fillers can be introduced to adjust characteristics like hardness and tensile strength. For instance, an industrial manufacturer can allow their CSM formulation to withstand particular stress levels by tweaking its design based on specific project needs. This flexibility means companies can adapt CSM for various uses, from automotive to medical applications, ensuring top-notch performance.
Neoprene also offers ample customization options, including variations in thickness, density, and surface finishes. These tweaks can improve neoprene properties, allowing manufacturers to create products like padded sports gear that offer enhanced comfort or seals that provide superior compression.
One fascinating area of development is the incorporation of recycled materials into formulations. As companies are increasingly pushed toward sustainability, both CSM and neoprene can adapt to include recycled polymer content, minimizing environmental impact while retaining performance features.
In summary, while both materials boast their customization abilities, understanding customer expectations and operational needs are pivotal in selecting the right formula. The right customization approach for your chosen rubber can make a substantial difference in the overall success of your project.
Customization Factor | Chlorosulfonated Polyethylene (CSM) | Neoprene |
---|---|---|
Additives and Fillers | Can enhance properties and performance | Adjust density and elasticity |
Thickness Options | Varies widely based on needs | Available in various thicknesses |
Environmental Considerations | New eco-friendly formulations are emerging | Incorporates recycled materials |
11. Expert Insights on Choosing Between CSM and Neoprene
Insights from industry experts can illuminate the path to making the best rubber selection. What should professionals focus on? The preference between chlorosulfonated polyethylene and neoprene often hinges on specific project requirements. Experts agree that assessing chemical exposure is a key determinant. For projects involving aggressive chemicals or outdoor exposure, CSM is typically recommended due to its superior resistance properties.
Another consideration is temperature tolerance. In sectors like automotive manufacturing, the longevity and resilience of CSM generally outstrip that of neoprene. Professionals in these fields often express that consistently using CSM has led to fewer operational setbacks, reinforcing its status as a trusted material.
Flexibility and comfort are also critical in domains such as sports equipment and consumer goods. For applications where user experience is paramount, neoprene reigns superior. Experts frequently highlight that neoprene’s elasticity provides a unique advantage when design and comfort are serious considerations.
Lastly, the overall costs can influence material choices as well. While some professionals may lean towards the lower initial cost of neoprene, others are becoming increasingly aware of the total cost of ownership. This perspective has led many to recognize the long-term value that can be derived from investing in CSM.
Considering these diverse expert insights can prove invaluable in guiding companies toward making well-informed material selections that align with current and future needs.
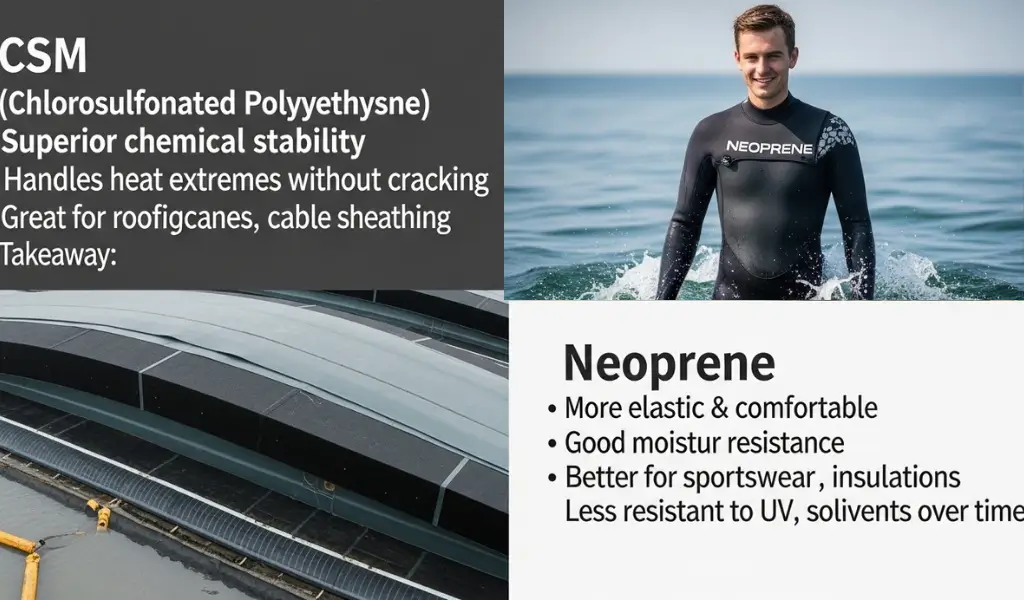
Expert Focus | Chlorosulfonated Polyethylene (CSM) | Neoprene |
---|---|---|
Chemical Resistance | Superior for aggressive environments | May struggle with certain solvents |
Temperature Resilience | Capable of handling extreme ranges | Good, yet has limitations on extreme heat |
Flexibility and Comfort | Less flexible compared to neoprene | Best for consumer-facing applications |
12. Future Trends in the Rubber Industry
What’s on the horizon for CSM and neoprene? Emerging trends can significantly influence how industries approach rubber material selection. One of the most significant shifts involves sustainability. As industries face mounting pressure to reduce carbon footprints, the focus on eco-friendly formulations will only intensify. This is leading to the development of more bio-based CSM materials, as well as the introduction of recycled content into neoprene formulations.
Additionally, advanced manufacturing technologies, including 3D printing and automation, will play a key role in the rubber industry. These technologies will enable custom rubber parts to be produced more efficiently and accurately. Customization will enhance performance and allow industries to cater to specific applications more rapidly, substantially reducing lead times.
Furthermore, the growing trend toward smart materials will likely impact how both CSM and neoprene are developed and marketed. Innovators are exploring materials that can adapt to environmental conditions, incorporating sensors or other technologies into rubber formulations that could respond to changes in temperature or other factors.
Lastly, there is a rising interest in hybrid solutions that combine the best properties of various materials. This research endeavors to merge the thermal stability of CSM with the flexibility of neoprene, leading to a new class of product that could meet myriad performance demands across different industries.
In summary, the rubber industry is on the brink of exciting changes. A commitment to sustainability, technological advancements, and the evolution of new materials will shape how businesses leverage CSM and neoprene in the future.
Future Trend | Implications for CSM | Implications for Neoprene |
---|---|---|
Sustainability Focus | Increased demand for bio-based options | Adoption of recycled materials |
Advanced Manufacturing | More efficient custom production | Improved lead times for bespoke products |
Smart Material Development | Potential integration of technology | New applications via innovative formulations |
13. User Reviews and Experiences
User experiences can provide real-world insights into the advantages and limitations of CSM and neoprene. While many professionals praise CSM for its robustness, ease of use, and longevity, some have noted that the initial cost can be a barrier. However, those who’ve adopted CSM often cite fewer replacements and a consequent reduction in long-term operational costs as significant upsides.
On the other hand, neoprene users appreciate its comfort and flexibility, particularly in consumer products like wet suits and sports gear. The easy availability of neoprene and its lower cost also make it a popular choice for manufacturers seeking budget-friendly solutions. However, users acknowledge that performance can vary significantly based on formulation, meaning that businesses must choose products wisely to ensure quality and performance.
For instance, a boat manufacturer using neoprene foam for cushioning in their vessels indicated that comfort and moisture resistance were critical but cautioned about the foam’s degradation under prolonged sun exposure. A construction firm utilizing CSM membranes for roofing reported exceptional satisfaction with performance and waterproofing, noting that the upfront investment paid off regarding durability.
These anecdotal experiences help paint a clearer picture of how each material operates in practice. Ultimately, user feedback can be a valuable tool for individuals and companies navigating the complexities of material selection.
User Group | Experiences | Key Takeaways |
---|---|---|
CSM Users | Praise for longevity and durability | Initial costs weighed against long-term savings |
Neoprene Users | Appreciate comfort and ease of use | Variability in quality tied to formulations |
Boat Manufacturers | Concerned about UV degradation | Importance of protective coatings |
14. Common Mistakes in Material Selection
What should industries watch out for when selecting rubber materials? Common mistakes in rubber material selection can lead to subpar performance and increased expenses. One of the significant errors is failing to conduct thorough assessments of project requirements. Many companies make the mistake of selecting materials based solely on initial cost without considering performance implications.
For instance, using neoprene in applications that expose it to harsh chemicals can lead to rapid degradation, necessitating costly replacements. On the other hand, choosing CSM for applications that don’t require high durability may lead to unnecessary expenses. It’s critical to align material choices with specific application needs.
Another common pitfall is overlooking supplier credibility. Businesses that choose suppliers based on price without investigating material quality can find themselves with substandard products that ultimately damage their operations. Different manufacturers have varying levels of expertise regarding CSM and neoprene, so it’s essential to prioritize quality and reliability over costs.
Furthermore, companies sometimes fail to consider the environmental implications of their material choices. As sustainability becomes increasingly important, businesses must consider material sourcing, lifecycle impacts, and recycling options.
In summary, avoiding these errors can dramatically enhance project outcomes and reduce costs. A well-informed selection process is crucial for the longevity and performance of the materials used.
Common Mistake | Description | Consequences |
---|---|---|
Overlooking Application Needs | Choosing based on cost rather than fit | Reduced performance and costly replacements |
Ignoring Supplier Reputation | Selecting based on price only | Risk of acquiring low-quality materials |
Lack of Environmental Consideration | Failing to assess sustainability | Missed opportunities for resource efficiency |
15. Conclusion and Key Takeaways
In conclusion, the comparison between chlorosulfonated polyethylene and neoprene highlights essential considerations for professionals selecting rubber materials. Both materials come with unique properties, practical applications, and user experiences that must be evaluated carefully to make informed decisions. CSM’s chemical and environmental resistance sets it apart for high-stress applications, while neoprene shines in areas requiring flexibility and comfort.
When weighing costs, it’s crucial to think long-term and assess total ownership costs beyond initial expenditures. Sustainability has become an indispensable aspect of material selection, and awareness of environmental impacts will guide industries toward more responsible choices.
In order to enhance operational effectiveness and product quality, businesses must be proactive in understanding the characteristics, applications, and limitations of each material. This thorough evaluation guarantees that manufacturing and operational challenges can be met with confidence.
Ultimately, equipping themselves with knowledge about CSM and neoprene will empower professionals to make choices that align with project demands and organizational values, leading to greater success across diverse applications.
FAQ Section
Q1: What is chlorosulfonated polyethylene?
Chlorosulfonated polyethylene (CSM) is a synthetic rubber known for its excellent chemical resistance, heat tolerance, and flexibility, widely used in automotive and construction applications.
Q2: How does neoprene rubber work?
Neoprene rubber is a flexible synthetic material that provides durability and moisture resistance, widely used in sports equipment, wetsuits, gaskets, and insulation.
Q3: What are the key differences between CSM and neoprene?
The key differences include their chemical resistance, temperature tolerances, durability, and applications suited for each, with CSM generally preferred for harsh environments and neoprene for flexibility.
Q4: Which rubber is better for outdoor applications?
Chlorosulfonated polyethylene (CSM) is typically better for outdoor applications due to its superior UV and environmental resistance, enhancing durability over neoprene.
Q5: How do I determine the right rubber for my project?
To determine the right rubber, assess specific project needs like exposure conditions, performance expectations, and potential costs, and compare the properties of CSM and neoprene against those needs.