In this article, we will explore how Chlorinated Polyethylene (CPE) compares to Chlorosulfonated Polyethylene (CSM). Both materials are widely used in industrial applications and understanding their differences is crucial for making informed material choices. This detailed examination will highlight their chemical compositions, physical properties, applications, benefits, challenges, and much more. By the end of this article, readers will have a clear understanding of how each material aligns with specific project needs and industry standards.
1. Introduction to CPE and CSM
What’s the real story? Chlorinated Polyethylene (CPE) and Chlorosulfonated Polyethylene (CSM) are two synthetic materials derived from polyethylene, each designed for specific applications and industries. CPE is created by chlorinating polyethylene, which enhances its resistance to chemicals, oils, and weathering. This makes it a popular choice for products requiring flexibility and durability. On the other hand, CSM is achieved by adding sulfuryl chloride to CPE, improving its resilience against harsh chemicals and environmental stressors.
Understanding these materials is essential in various industries, including construction, automotive, and manufacturing. Each plays a unique role in product applications, and knowing their features can significantly impact project efficiency and durability. As various sectors increasingly seek materials that provide superior performance and longevity, determining the right choice between CPE and CSM has never been more critical. In this section, we will lay the foundation for understanding these two polymers and set the stage for further comparisons.
Property | CPE | CSM |
---|---|---|
Source | Chlorinated Polyethylene | Chlorosulfonated Polyethylene |
Chemical Structure | Modified Polyethylene | Sulfonated modified Polyethylene |
Common Applications | Flexible hoses, cable insulation | Roofing membranes, industrial coatings |
2. Chemical Composition
Let’s dive into chemistry. The chemical composition of materials like CPE and CSM plays a crucial role in determining their properties and uses. Chlorinated Polyethylene (CPE) consists of a polyethylene backbone that has chlorine atoms attached to its structure. This chlorination process (as outlined in‘’Chlorinated Polyethylene (CPE) – Types, Properties, Uses & Structure‘’) increases the material’s thermal stability, making it useful in applications where heat resistance is essential.
Conversely, Chlorosulfonated Polyethylene (CSM) begins with CPE, which is further treated with sulfuryl chloride. This additional sulfonation enhances its resistance to corrosive chemicals, making it ideal for environments exposed to strong acids or bases. The incorporation of sulfonic acid groups improves adhesion properties, making CSM particularly valuable in bonding applications.
Additionally, the molecular weight and density of these substances can affect their mechanical performance. CPE typically exhibits a lower density compared to CSM. The differences in chemical composition directly impact various application areas, where performance might vary based on environmental factors, such as temperature and exposure to chemicals. This is where it gets interesting—understanding these fundamental differences can be the key to optimizing material selection for specific functions and projects.
Composition Element | CPE | CSM |
---|---|---|
Backing Material | Polyethylene | Modified Polyethylene |
Chemical Additives | Chlorine | Sulfuryl chloride |
Functional Groups | Halogens | Sulfonates |
3. Physical Properties of CPE and CSM
Understanding the physical properties of CPE and CSM is essential for making informed decisions in material selection. CPE is known for its excellent flexibility, which allows it to be molded into a variety of shapes. This flexibility makes it ideal for applications requiring bending or movement, such as hose manufacturing and insulation for electrical cables. Furthermore, CPE possesses good tensile strength, which ensures that products can withstand considerable stress without breaking.
In stark contrast, CSM displays enhanced dimensional stability and durability. One of its standout features is superior weather resistance, which helps it retain its properties when exposed to UV light and extreme weather conditions. Additionally, CSM maintains flexibility even in low-temperature environments, making it an excellent choice for outdoor applications such as roofing and waterproofing.
The mechanical properties of both materials can vary significantly, depending on formulation and processing conditions. It is this combination of properties that can dictate their use in specific applications. This is where the discussion gets fascinating—understanding how these physical attributes translate into real-world performance can help manufacturers tailor their products for better outcomes.
Physical Property | CPE | CSM |
---|---|---|
Flexibility | High | Moderate |
Tensile Strength | Good | Superior |
Weather Resistance | Moderate | High |
Thermal Stability | Good | Excellent |
4. Chemical Resistance
Chemical resistance is a vital consideration for materials used in harsh environments. Chlorinated Polyethylene (CPE) offers robust resistance to various chemicals, including oils and greases, which makes it suitable for applications in automotive and marine industries. However, it can be susceptible to degradation when exposed to certain solvents and chemicals like ketones.
In contrast, Chlorosulfonated Polyethylene (CSM) exhibits superior resistance to a wider range of aggressive chemicals, including acids, alkalis, and organic solvents. This enhanced vulnerability means CSM can be used safely in environments where exposure to hazardous substances is likely. Its ability to maintain integrity under such conditions is a critical factor for many industries.
Next, let’s dissect how applications can vary based on these resistance properties. For example, CPE might be preferred in automotive applications where oil exposure is common, while CSM is better suited for chemical processing plants where corrosive substances are present. The nuances in performance can significantly dictate the selection process for engineers and product developers.
Chemical | CPE Resistance | CSM Resistance |
---|---|---|
Oils | Good | Excellent |
Acids | Moderate | Excellent |
Solvents | Moderate | High |
Alkalis | Poor | Excellent |
5. Applications of Chlorinated Polyethylene (CPE)
Chlorinated Polyethylene (CPE) finds its niche across various industries due to its versatility and desirable properties. One of the most common applications of CPE is in the production of flexible hoses (as described in ‘’What Is Chlorinated Polyethylene Used For?‘’) used in both industrial and household settings. Its resistance to oils and chemicals allows these hoses to function safely in a range of environments.
Another application of CPE is in cable insulation. In this role, it performs admirably, thanks to its excellent dielectric properties and flexibility, helping to conduct electricity while protecting sensitive wiring. Furthermore, CPE is often used as a modifier in blends to improve the mechanical properties of other polymers, enhancing the overall performance of end products.
But here’s the kicker—CPE’s relatively low production cost and ease of processing make it a favorable option for manufacturers looking to optimize their cost-efficiency without sacrificing quality. Knowing where and how to leverage CPE can significantly impact project effectiveness and performance.
Application | Description | Key Benefits |
---|---|---|
Flexible Hoses | Used in automotive, industrial sectors | Oil resistance, durability |
Cable Insulation | Insulates electrical wiring | Excellent flexibility, dielectric strength |
Polymer Modifier | Enhances performance of other plastics | Cost-effective, improves mechanical strength |
6. Applications of Chlorosulfonated Polyethylene (CSM)
When it comes to applications, Chlorosulfonated Polyethylene (CSM) demonstrates exceptional performance in demanding environments,as explored in”What are the properties and applications of CSM rubber?”.One of its primary uses is in roofing and waterproofing membranes, where its ability to resist ultraviolet rays and extreme weather plays a critical role in prolonging the lifespan of roofs. CSM’s flexibility also allows it to adapt to building movements, making it ideal in construction settings.
Moreover, CSM is widely used in industrial coatings due to its superior adhesion and chemical resistance. These properties help ensure that surfaces remain protected from corrosion and wear, extending the life of machinery and structures. Additionally, CSM is employed in the manufacturing of flexible hoses and gaskets, often in automotive applications, where compatibility with aggressive fluids is essential.
Ready for the good part? CSM’s versatility allows it to serve across a multitude of sectors, driving increased demand across construction, automotive, and a variety of manufacturing industries. Its unique properties position it as a critical material for any project requiring longevity and resilience.
Application | Description | Key Benefits |
---|---|---|
Roofing Membranes | Waterproofing roofs | UV resistance, flexibility |
Industrial Coatings | Protective coatings for surfaces | Chemical resistance, long-lasting |
Flexible Hoses | Used in automotive and machinery | Superior durability, flexible |
7. Advantages of CPE
Chlorinated Polyethylene (CPE) offers numerous advantages that make it a go-to material for various applications. First and foremost, CPE is known for its excellent flexibility. This characteristic allows it to fit easily into diverse applications, especially where bends and curves are necessary.
Additionally, CPE exhibits good thermal stability, which means it can withstand a range of temperatures without significant degradation of its properties. This makes it particularly useful for outdoor applications subject to varying climates. The cost-effectiveness of CPE cannot be overlooked either. Compared to other polymers with similar properties, CPE is often more affordable, providing substantial savings to manufacturers.
What’s more interesting? CPE can be blended with other materials, enhancing performance without compromising quality. This makes it a versatile choice when looking to design specific characteristics for various end products that meet industry standards while remaining budget-friendly.
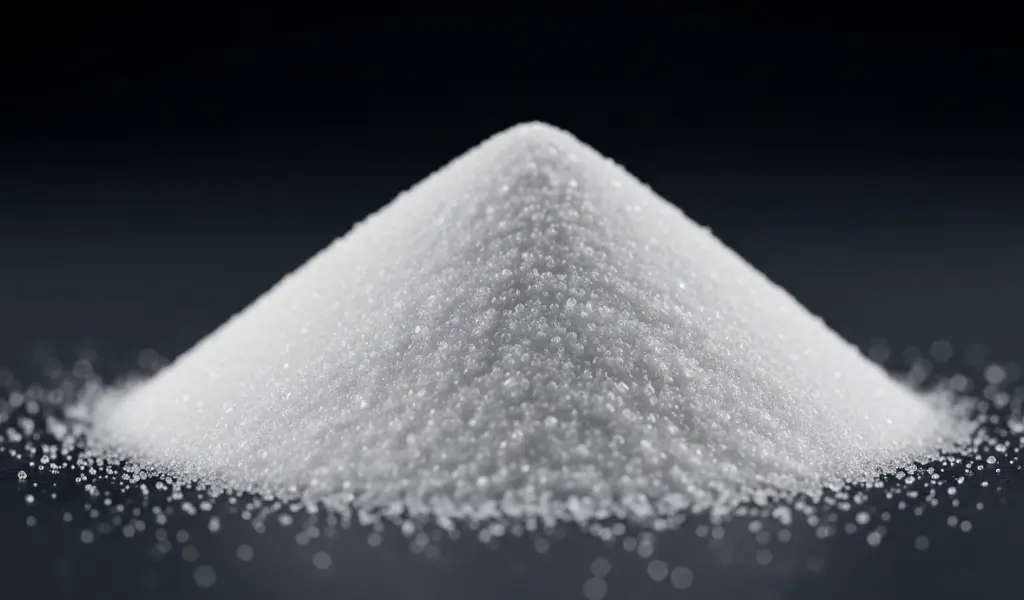
Advantage | Description | Impact on Application |
---|---|---|
Flexibility | Can be molded into various shapes | Ideal for hoses, cables |
Cost-Effectiveness | Lower production costs | Savings for manufacturers |
Thermal Stability | Maintains properties over a range of temperatures | Suitable for outdoor uses |
8. Advantages of CSM
Chlorosulfonated Polyethylene (CSM) brings a unique set of advantages to the table, positioning it as a superior material for critical applications. One of its most significant benefits is its unparalleled chemical resistance. This property ensures that CSM can withstand exposure to harsh environments, such as in chemical processing facilities, without degrading.
Moreover, CSM offers excellent thermal stability, like CPE but with enhanced retention of mechanical properties under extreme conditions. This feature allows CSM to be a favored material in applications requiring both flexibility and durability. The material also showcases impressive adhesion characteristics, ensuring that it bonds effectively with surfaces, which is essential in coatings and membranes.
But here’s the kicker—CSM’s versatility in extreme environments opens up a world of possibilities across various industries. Its properties enable manufacturers to push the boundaries of product functionality and safety while maintaining compliance with stringent regulatory standards.
Advantage | Description | Impact on Application |
---|---|---|
Chemical Resistance | Withstands harsh chemicals | Widely used in industrial settings |
Thermal Stability | Maintains performance in extreme conditions | Essential for safety and efficiency |
Adhesion Properties | Bonds well with surfaces | Improves performance in coatings |
9. Disadvantages of CPE
While Chlorinated Polyethylene (CPE) has many advantages, it is not without its drawbacks. One primary issue is its vulnerability to certain solvents, which can lead to degradation over time. In environments where exposure to aggressive chemicals is prevalent, CPE may not perform as effectively as other materials.
Additionally, CPE is not as resistant to extreme temperatures compared to its counterpart, CSM. In high-temperature scenarios, CPE’s mechanical properties may begin to diminish, potentially compromising the integrity of products made from it. Furthermore, while CPE’s production costs are relatively lower, the potential long-term costs associated with maintenance and replacement in challenging environments can offset initial savings.
This leads us to understand that while CPE is versatile, selecting it for applications without considering its limitations can lead to performance issues. Thus, making informed material choices based on comprehensive knowledge of its properties is essential.
Disadvantage | Description | Impact on Application |
---|---|---|
Chemical Vulnerability | Prone to degradation in solvents | Limited use in certain industries |
Temperature Limitations | Loses properties in high heat | Not ideal for extreme conditions |
Long-Term Costs | Replacement and maintenance can be costly | Potential hidden expenses |
10. Disadvantages of CSM
Chlorosulfonated Polyethylene (CSM) can encounter various challenges, which might affect its adoption in certain applications. One significant disadvantage is the higher production and process costs compared to CPE. These costs can deter manufacturers from choosing CSM, especially in highly competitive markets where profitability is critical.
Another issue with CSM is its processing characteristics. The material requires specific equipment and conditions, making it less accessible for some manufacturers accustomed to working with simpler materials. Additionally, while CSM offers significant advantages in chemical resistance, it can still degrade when subjected to certain aggressive environments over extended periods. Understanding these limitations is critical for proper application selection.
So what does this mean for potential users? While CSM offers superior properties in many areas, organizations must weigh these benefits against the drawbacks to make the best material choice for their needs. The trade-off between performance and cost-effectiveness is a crucial aspect of material selection.
Disadvantage | Description | Impact on Application |
---|---|---|
Higher Production Costs | More expensive than CPE | May limit use in budget-sensitive projects |
Complex Processing | Requires specific equipment | Less accessible for some manufacturers |
Chemical Vulnerabilities | Can degrade over time in harsh conditions | May not be suitable for all environments |
11. Real-World Comparisons
Let’s take a look at the real-world scenario. Comparing the applications of CPE and CSM reveals striking differences in their performance and suitability across various industries. A practical example can be seen in the automotive sector. CPE is often utilized for flexible hoses that transport fluids, where its elasticity is crucial. However, in applications needing enhanced chemical resistance, such as fuel lines or components exposed to corrosive substances, CSM would be the preferred choice due to its superior properties.
In construction, CPE is commonly used for insulation purposes, where temperature fluctuations are a concern. Conversely, CSM is favored for roofing applications, where its waterproofing capabilities and resistance to UV degradation come into play. Additionally, CSM’s ability to maintain integrity in harsh environments makes it an ideal choice for industrial coatings, while CPE’s cost-effectiveness offers an accessible alternative for everyday materials.
Why does this matter? These real-world applications illustrate how understanding the unique properties of each material can lead to smarter, more efficient choices in product development and project execution.
Industry | CPE Applications | CSM Applications |
---|---|---|
Automotive | Flexible hoses | Fuel lines and engine components |
Construction | Insulation materials | Roofing systems and waterproofing |
Industrial Coatings | Basic coatings | Protective industrial coatings |
12. Future Trends in CPE and CSM Use
As industries evolve, so do the materials that comprise them. The future for Chlorinated Polyethylene (CPE) and Chlorosulfonated Polyethylene (CSM) shows promising developments driven by innovation and sustainability concerns. Manufacturers are increasingly seeking green alternatives and more environmentally friendly production processes, which could lead to the development of bio-based versions of these materials.
Furthermore, advancements in technology allow for the enhancement of material performance through improved formulations and processing techniques. This innovation is particularly significant in construction, where materials that offer improved thermal efficiency and lower environmental impact are in demand. Likewise, CSM is expected to see modifications that enhance its chemical resistance and longevity in challenging environments.
So what’s the takeaway? As these materials adapt and evolve, businesses that stay informed about emerging trends can leverage new opportunities for growth and efficiency in their manufacturing and design processes. Keeping abreast of these changes will be crucial for companies striving to maintain a competitive edge.
Trend | Impact on CPE | Impact on CSM |
---|---|---|
Sustainability | Demand for eco-friendliness | Development of bio-based versions |
Technological Advancements | Improved formulations | Enhanced resistance properties |
Industry Innovations | Shift towards greater efficiency | Growth in demand for flexible applications |
13. Making the Right Material Choice
Choosing between Chlorinated Polyethylene (CPE) and Chlorosulfonated Polyethylene (CSM) can be a challenging decision without the right understanding. Start by evaluating the specific requirements of your project. What environmental conditions will the material face? Will it be exposed to harsh chemicals or temperatures? Understanding these factors plays a crucial role in determining the appropriate material.
Additionally, consider the long-term impacts of your choice. While CPE may offer immediate cost savings, CSM could provide greater durability and lower maintenance costs over time. Engage with manufacturers and suppliers to learn about the latest advancements in both materials, and assess their recommendations based on your project needs.
Ultimately, ensuring a material choice aligns with both current and future project demands will lead to more efficient operations and enhanced performance across applications. Taking a thoughtful approach to this decision can yield significant benefits in both the short and long term.
Criteria | Considerations for CPE | Considerations for CSM |
---|---|---|
Environmental Exposure | Moderate chemical resistance | High chemical resilience |
Cost Considerations | Lower initial costs | Higher production costs |
Longevity and Maintenance | Potential for higher maintenance | Durability can lead to cost savings |
14. Conclusion: Key Takeaways
As we wrap up our examination of Chlorinated Polyethylene (CPE) and Chlorosulfonated Polyethylene (CSM), several key takeaways emerge. CPE is celebrated for its flexibility and cost-effectiveness but comes with some limitations in harsh chemical environments. In contrast, CSM shines with its chemical resistance and longevity, making it the material of choice for demanding applications, albeit at a higher price point.
Understanding the nuances between these two materials is essential for making sound decisions in various industries. The primary factor to consider is the context in which the material will be used and the specific performance characteristics required for success.
Plan for future innovations, embrace sustainability, and continually reassess material performance as industries evolve. By doing so, businesses can harness the inherent strengths of each material to optimize their product offerings and enhance project outcomes.
Summary Point | CPE | CSM |
---|---|---|
Key Advantage | Flexibility, cost savings | Chemical resistance, longevity |
Ideal Applications | Automotive, construction | Industrial, roofing |
Future Considerations | Sustainable alternatives | Technological advancements |
FAQ Section
Q1: What is Chlorinated Polyethylene (CPE)?
Chlorinated Polyethylene (CPE) is a synthetic rubber created by chlorinating polyethylene, enhancing its resistance to chemicals and weathering for various industrial applications.
Q2: How does Chlorosulfonated Polyethylene (CSM) work?
Chlorosulfonated Polyethylene (CSM) is produced by sulfonating chlorinated polyethylene, leading to a material that boasts improved chemical and environmental resistance, making it suitable for demanding applications.
Q3: What are the key differences between CPE and CSM?
CPE is flexible and cost-effective but may degrade in harsh chemicals, while CSM offers superior chemical resistance and durability, making it ideal for critical applications.
Q4: What are the advantages of using CPE?
CPE’s main advantages include flexibility, thermal stability, and cost-effectiveness, allowing it to be used across various applications without significant performance compromises.
Q5: How do I choose between CPE and CSM for my project?
When selecting materials, consider factors such as environmental exposure, cost, and longevity needs. Understanding specific project requirements and consulting with suppliers will aid in making the best choice.