Discover why manufacturers are using CPE in 2025 for better durability, flexibility, and sustainability across automotive, construction, and more.
1. Introduction
CPE material is a thermoplastic polymer that offers a range of benefits for manufacturers, setting it apart from traditional materials. But here’s the kicker—its versatility is one of the key reasons manufacturers have turned to CPE in recent years. As demands for durability and performance increase, CPE’s unique characteristics make it an attractive option. In the aerospace, automotive, and construction sectors, manufacturers are constantly looking for materials that strike the right balance between ease of processing and high-performance capabilities. CPE material checks all these boxes.
Understanding the properties and applications of CPE material is vital to tapping into its potential. This article will delve deeper into how CPE material affects manufacturing processes, why so many companies are adopting it, and its implications for the future. By establishing the foundation of knowledge surrounding CPE, we enable manufacturers to appreciate its significance in contemporary operations.
Property | Description | Importance |
---|---|---|
Chemical Resistance | Resists acids, bases, and other chemicals | Ideal for harsh environments |
Thermal Stability | Maintains integrity over a wide temperature range | Suitable for various applications |
Flexibility | Offers superior elasticity compared to similar materials | Enhances product durability |
2. Understanding CPE Material Properties
To appreciate why manufacturers choose CPE material, one must understand its properties. What’s the real story? CPE is known for its exceptional chemical and thermal resistance, making it an ideal material for demanding applications. Its chemical structure is modified to improve performance and durability, which is crucial for industries exposed to corrosive substances or high temperatures.
CPE material also possesses excellent flexibility and elasticity. These properties allow it to perform reliably in situations where other materials might fail, such as sealing applications that require elongation and compression. Manufacturers often find that CPE can withstand repeated stress without losing its original properties, thereby minimizing the likelihood of failure in critical components.
Moreover, the unique molecular structure of CPE contributes to its capability to bond well with other materials, enhancing its versatility. Manufacturers benefit from integrating CPE into systems that require compatibility with multiple substrates, whether for adhesives, coatings, or blended materials. This further widens its appeal across various manufacturing sectors.
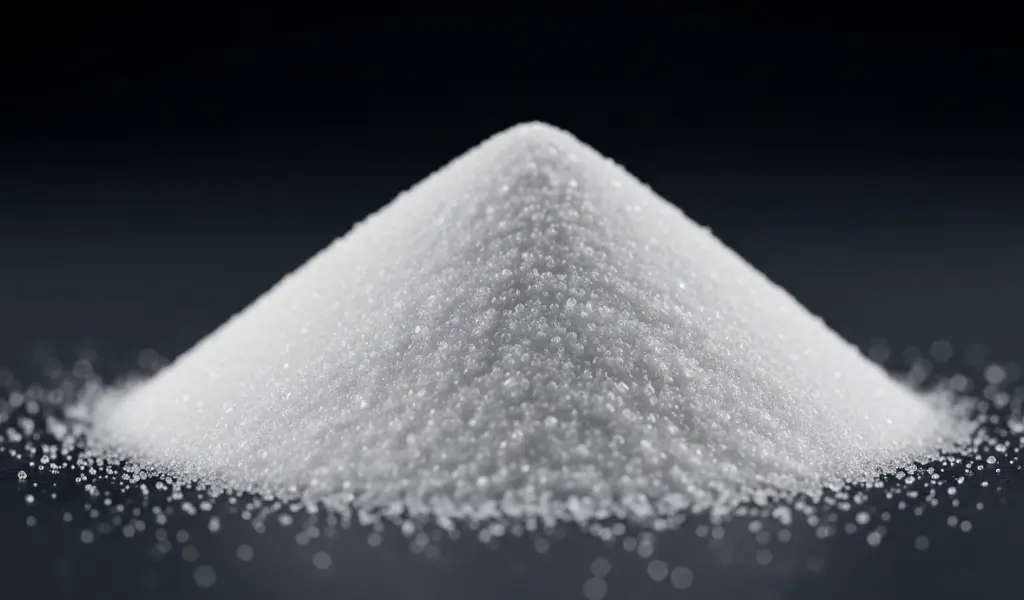
Property | Value/Description | Relevance to Manufacturing |
---|---|---|
Density | Typically ranges from 1.15 to 1.25 g/cm³ | Impacts weight considerations in design |
Hardness | Shore A hardness of 60-80 | Related to durability in end-use applications |
Processing Temperature | Optimal temperatures between 160°C to 180°C | Affects manufacturing methods and energy costs |
3. Applications in Manufacturing
CPE material is becoming increasingly prevalent in different manufacturing sectors. Ready for the good part? Its versatility extends beyond traditional domains, finding a place in industries such as automotive, electronics, and construction. Specifically, CPE is often used to create automotive seals, gaskets, and vibration dampeners. The automotive industry values CPE for its ability to withstand extreme temperatures, exposure to oils and chemicals, and durability in various weather conditions.
In electronics, CPE material serves as an insulator and protective coating. Manufacturers benefit from CPE’s excellent electrical properties, ensuring that electronic components remain safe and operational in diverse settings. Additionally, CPE is used for insulation in cables, where both flexibility and thermal stability are required.
The construction industry utilizes CPE for applications like roofing membranes and sealants, where waterproofing and durability are necessary. CPE materials are employed in creating flexible and robust seals that prevent water ingress in buildings, ensuring architectural longevity. These examples illustrate the breadth of CPE material’s applications and how it enhances product performance across various industries.
Industry | Application | Benefits |
---|---|---|
Automotive | Seals and gaskets | Resistance to extreme temperatures and chemicals |
Electronics | Insulators and coatings | Enhanced electrical performance and durability |
Construction | Roofing membranes and sealants | Long-lasting waterproofing and flexibility |
4. Advantages of CPE Material
The choice of CPE material over other alternatives is not arbitrary. So, what are the significant advantages? One of the foremost benefits of CPE material is its remarkable durability, which means it can withstand various environmental factors without deteriorating. This characteristic is invaluable for manufacturers who need long-lasting products in harsh conditions. Whether it’s extreme heat, moisture, or exposure to chemicals, CPE material consistently performs at a high level.
Another essential advantage lies in its cost-effectiveness. While CPE may have a higher initial cost compared to some materials, its longevity and low maintenance requirements mean lower lifetime costs. Manufacturers can expect fewer product failures and replacements, leading to overall savings and enhanced operational efficiency.
Moreover, CPE material’s compatibility with various other materials opens the door for innovative product designs. It can be easily blended with other polymers and formulated to meet specific performance needs. This flexibility allows manufacturers to experiment with combinations that further enhance product characteristics while leveraging CPE’s core strengths (see‘’Chlorinated Polyethylene (CPE) – Types, Properties, Uses & Structure‘’)..
Advantage | Description | Impact on Manufacturing |
---|---|---|
Durability | Long-lasting performance in extreme conditions | Reduces replacement costs |
Cost-Effectiveness | Lower lifetime costs despite higher initial expenses | Increases profitability |
Compatibility | Easily blends with other materials | Enhances product design flexibility |
5. Challenges in CPE Material Usage
While CPE material has many advantages, it is not without its challenges. But here’s the kicker—understanding these challenges is crucial for manufacturers looking to implement CPE effectively. The first major challenge is regulatory compliance. In many regions, manufacturers must adhere to strict guidelines concerning the use of chlorinated compounds. Organizations must ensure they comply with environmental regulations, which can complicate the sourcing and processing of CPE.
Another challenge lies in the sourcing of high-quality raw materials. Not all CPE materials are created equal, and manufacturers must rely on suppliers who can consistently provide materials that meet stringent performance specifications. Sourcing challenges can lead to production delays and might affect product quality.
Additionally, while CPE offers great flexibility, it can be more difficult to process compared to other thermoplastics. Manufacturers may face issues such as increased cycle times during production, which can affect productivity and throughput. Understanding these challenges overall allows manufacturers to create more robust plans for implementing CPE material into their operations.
Challenge | Description | Potential Solutions |
---|---|---|
Regulatory Compliance | Must meet strict guidelines for chemical use | Work closely with suppliers and regulatory bodies |
Quality Sourcing | Inconsistent material quality can lead to issues | Establish long-term contracts with reliable suppliers |
Processing Complexity | May require specialized machinery and techniques | Invest in staff training and process optimization |
6. Why Manufacturers Choose CPE Material
When it comes to choosing materials, manufacturers weigh various factors. So, what drives manufacturers to select CPE? One of the primary reasons is the material’s superior performance characteristics. Companies look for materials that enhance product reliability, and CPE delivers. Whether in automotive parts or protective coatings, the ability to withstand heat and adverse conditions makes CPE a preferred choice.
Feedback from industry experts consistently highlights CPE’s flexibility and durability as critical performance attributes. Manufacturers gain peace of mind knowing that they are using a material whose properties can be tailored through formulations to meet specific application needs.
Moreover, case studies have shown how transitioning to CPE has led to significant improvements in product performance and customer satisfaction. Companies that have already adopted CPE often report fewer product defects and enhanced overall functioning, which directly contributes to customer loyalty and market competitiveness.
Reason | Description | Impact |
---|---|---|
Superior Performance | High durability and flexible characteristics | Improved product reliability |
Expert Recommendations | Backing from industry specialists | Increased trust and confidence |
Positive Case Studies | Evidence of enhanced functioning in real applications | Boosts market potential and customer satisfaction |
7. Sustainability and CPE Material
Sustainability is a significant concern in today’s manufacturing landscape. What’s the real story? Manufacturers are increasingly committed to adopting eco-friendly practices, and CPE material presents opportunities for sustainability. CPE is recyclable, which means that manufacturers can reduce waste and minimize their environmental impact. The lifecycle of CPE material lends itself well to assessment; its durability means it is less likely to end up in landfills compared to less durable alternatives.
Furthermore, CPE manufacturers are progressing toward sustainable production processes that minimize energy consumption and emissions. Some companies have even begun using bio-based materials to produce CPE, (as highlighted in‘’Chlorinated Polyethylene (CPE) Health & Environment: A Comprehensive B2B Guide‘’) addressing both consumer and regulatory concerns about environmental impact.
The adoption of CPE material can also be a marketing advantage. Today’s consumers are gravitating toward brands that emphasize sustainability. By using CPE, manufacturers not only fulfill environmental commitments but also appeal to eco-conscious customers seeking responsible manufacturing practices.
Aspect | Description | Benefits for Manufacturers |
---|---|---|
Recyclability | CPE material can be recycled | Decreases waste and conserves resources |
Sustainable Production | Techniques used in CPE manufacturing promote sustainability | Aligns with consumer preferences |
Eco-Friendly Alternatives | Use of bio-based inputs in CPE production | Enhances brand reputation and customer loyalty |
8. Future Trends in CPE Material Development
Looking ahead, the trends surrounding CPE material are fascinating. Ready for the good part? Innovations in material science are driving advancements in CPE formulations and applications. Researchers are working on improving the characteristics of CPE, such as enhancing its thermal stability and reducing production costs without sacrificing quality. These innovations have the potential to expand the usability of CPE material in the market further.
Moreover, the movement toward sustainability is likely to become even more pronounced in the coming years. As regulatory environments tighten, the expectation for manufacturers to adopt environmentally friendly materials will only grow. CPE manufacturers that can deliver products that meet these evolving standards will likely see increased demand.
Additionally, technological advancements such as 3D printing are opening up new avenues for utilizing CPE. Manufacturers are exploring how CPE can be integrated into additive manufacturing processes, allowing for greater design flexibility and rapid prototyping.
Trend | Description | Implications for the Manufacturing Industry |
---|---|---|
Enhanced Formulations | Development of next-gen CPE that performs better | Broader applications across industries |
Sustainability Focus | Increased emphasis on eco-friendly production | Aligns manufacturing with regulatory trends |
Integration with 3D Printing | Opportunities for innovative designs and prototypes | Enhances the versatility of CPE material |
9. Comparison with Other Materials
When considering materials for manufacturing applications, it is essential to compare options. So, how does CPE stack up against its competitors? One of the most common comparisons is between CPE and PVC (Polyvinyl Chloride). While PVC is often cheaper, it lacks the flexibility and chemical resistance that CPE offers, particularly in extreme conditions. Additionally, CPE outperforms PVC in many applications requiring durability and longevity.
Another material often compared to CPE is EVA (Ethylene Vinyl Acetate). EVA possesses excellent elasticity, but it may not have the same chemical resistance levels as CPE. Manufacturers will find that while EVA may be suitable for certain applications, CPE offers a broader range of use cases, particularly in harsh environments.
Rubber is another option that manufacturers frequently examine. While rubber is highly flexible, it can degrade over time due to environmental exposure. In contrast, the inherent properties of CPE allow it to maintain performance integrity far longer than traditional rubber materials.
Material | Key Characteristics | Strengths | Weaknesses |
---|---|---|---|
CPE | Chemical resistance, flexibility, durability | Reliable in harsh conditions | Requires careful handling |
PVC | Low cost, good mechanical performance | Cost-effective | Limited flexibility |
EVA | Excellent elasticity | Good for shock absorption | Weaker chemical resistance |
Rubber | High flexibility, compressibility | Effective for sealing | May degrade faster |
10. Testing and Quality Assurance
Before CPE material can be implemented in manufacturing processes, rigorous testing is essential. What’s the real story? Quality assurance in CPE production is crucial to ensure its performance aligns with industry specifications. Various testing methods assess the material’s mechanical, thermal, and chemical properties.
Manufacturers often utilize standardized tests that evaluate tensile strength, elongation, hardness, and thermal stability. These tests not only help confirm that CPE meets requisite performance criteria but also provide insight into any potential defects that may appear during production.
Moreover, implementing a robust quality control system throughout the manufacturing process can prevent issues from arising later. By maintaining high standards of quality assurance, manufacturers can ensure that the end products are reliable and function as intended.
Testing Method | Purpose | Importance |
---|---|---|
Tensile Testing | Determines material strength and elasticity | Ensures product reliability |
Elongation Tests | Measures how much CPE can stretch before breaking | Assesses flexibility and performance under stress |
Hardness Testing | Evaluates surface hardness | Identifies effective application for products |
Thermal Stability Tests | Assesses performance at varying temperatures | Critical for applications in extreme environments |
11. The Economic Impact of CPE Material Choices
The financial implications of choosing CPE material can be significant. But here’s the kicker—the durability and longevity of CPE can ultimately lead to reduced costs for manufacturers in the long run. Initial investments in CPE material may seem higher when compared to alternatives, but the longevity of products made from CPE can result in fewer replacements and lower maintenance costs.
Understanding cost-benefit ratios is vital. Manufacturers conducting a thorough economic analysis will consider factors such as production efficiency, waste reduction, and customer satisfaction. The return on investment associated with CPE often justifies the initial expenditure.
Additionally, adopting CPE material can enhance a manufacturer’s overall competitiveness in the market. With an emphasis on resilient products, organizations can capture a more extensive market share by addressing consumer demands for quality and durability.
Economic Factor | Description | Financial Implications |
---|---|---|
Initial Costs | Higher upfront investment | Justified by long-term savings |
Maintenance Costs | Lower upkeep due to durability | Reduces overall operational expenses |
Market Competitiveness | Enhanced product durability and reliability | Attracts more customers, leading to revenue growth |
12. Adoption Rates of CPE Material Among Manufacturers
As CPE material continues to gain traction, understanding adoption rates is crucial. Ready for the good part? Studies show that more manufacturers are recognizing the advantages of CPE. Industries that rely heavily on durability and resilience, like automotive and construction, are witnessing an increase in the adoption of CPE material.
Current statistics suggest that adoption rates have climbed steadily over the past few years. Factors influencing this shift include technological advancements, increased awareness of CPE’s benefits, and pressure to adopt sustainable materials. As regulatory pressure mounts for eco-friendly materials, manufacturers are migrating toward CPE as a viable option.
Predictions suggest that as production techniques improve and CPE becomes more mainstream, adoption rates will likely accelerate. Staying ahead of this trend will position manufacturers favorably in their markets.
Year | Adoption Rate (%) | Influencing Factors |
---|---|---|
2020 | 30% | Initial awareness of benefits |
2021 | 45% | Enhanced sustainability considerations |
2022 | 60% | Improved production techniques and quality |
2023 | 70% (predicted) | Regulatory pressure for eco-friendly options |
13. Customer Expectations Regarding
Understanding customer expectations is crucial for manufacturers. But here’s the kicker—today’s consumers are increasingly informed and demanding. They seek transparency in materials and production processes, placing a premium on products that deliver quality and performance. CPE material, with its high durability and favorable environmental properties, aligns perfectly with these expectations.
Engaging directly with customers through surveys or feedback mechanisms can provide invaluable insights. Manufacturers that take customer feedback into account can better tailor their CPE-based products to meet specific needs and preferences.
Moreover, companies that market their use of CPE material can enhance their brand image. Positioning CPE as a sustainable and high-quality choice allows manufacturers to connect more deeply with consumers looking for responsible purchasing options.
Expectation | Description | Implications for Manufacturers |
---|---|---|
Quality Assurance | Demand for high-performance materials | Necessary to ensure product reliability |
Sustainability | Preference for eco-friendly options | Alignment with sustainable practices |
Transparency | Desire for clear communication about materials | Strengthens brand loyalty and trust |
14. Expert Insights on CPE Material
Industry experts offer valuable perspectives on the use of CPE material. What’s the real story? Interviews with material scientists and manufacturing professionals reveal that CPE’s unique properties and versatility significantly enhance product performance in various applications. Many experts advocate for CPE as a material of choice for future developments, given its adaptability to emerging technologies.
Gleaning insights from industry leaders provides manufacturers with actionable strategies. Best practices for implementation, based on expert recommendations, often include thorough training sessions for employees on the handling and processing of CPE materials. This ensures that manufacturers fully realize the benefits of incorporating CPE into their products.
Furthermore, experts emphasize the necessity for continual research and development. Keeping pace with consumer demand trends and regulatory shifts ensures CPE manufacturers remain competitive and relevant.
Expert Field | Key Recommendations | Benefits |
---|---|---|
Material Science | Invest in R&D to enhance CPE characteristics | Improves product offerings |
Manufacturing Practices | Train teams on CPE handling and processing | Increases efficiency and reduces errors |
Market Analysis | Monitor trends and consumer feedback | Aligns product development with market needs |
15. Conclusion: The Role of CPE Material in Future Manufacturing
In conclusion, the narrative surrounding CPE material is rich with opportunities. Ready for the good part? Manufacturers are increasingly recognizing CPE’s advantages—its durability, flexibility, and eco-friendly properties make it a material of choice moving forward. As global demands for sustainability grow, CPE positions itself as a leading option for companies looking to meet these evolving needs.
Understanding CPE material’s properties, applications, and advantages enables manufacturers to make informed decisions that will benefit them in the long term. The future is bright for CPE, and embracing this material is critical for companies aiming to innovate and thrive in an ever-competitive landscape.
FAQ Section
CPE material, or Chlorinated Polyethylene, is a thermoplastic polymer known for its flexibility, durability, and resistance to extreme temperatures and chemicals.
Q2: How does CPE material benefit manufacturers?
CPE material provides high durability, cost-effectiveness, and excellent compatibility with other materials, enhancing product performance across various applications.
Q3: What are the common applications of CPE material?
CPE is commonly used in automotive parts, electronic insulators, and construction materials, providing reliable performance in numerous industries.
Q4: What are the challenges associated with CPE material usage?
Challenges include regulatory compliance, sourcing quality materials, and processing complexities, which manufacturers must address for successful implementation.
Q5: How does CPE material compare to other manufacturing materials?
CPE generally offers better durability and flexibility than alternatives like PVC and rubber, making it suitable for demanding applications where reliability is essential.