Chlorosulfonated Polyethylene: Elastomer Materials Guide introduces a high-performance polymer that solves chemical resistance challenges in industrial applications. Here’s the deal… Many manufacturers struggle with material degradation under harsh environments but face costly downtime and frequent replacements. But here’s the kicker… CSM offers exceptional stability against oils, ozone, UV, acids and bases, extending service life and reducing maintenance costs. This guide presents clear insights into CSM’s structure, properties, processing methods and application benefits, backed by industry standards and real‑world case studies. You can trust this information based on ASTM and ISO benchmarks and decades of proven performance in rubber hoses, seals and protective coatings.
Introduction to Chlorosulfonated Polyethylene
Chlorosulfonated polyethylene (CSM) stands out as a versatile elastomer that solves multiple industrial pain points at once. What’s the real story? Many conventional rubbers crack under ozone exposure or degrade when in contact with oils. CSM’s unique chemical structure grafts chlorine and sulfonyl groups onto polyethylene chains, creating sites for crosslinking that boost chemical resistance and weather stability. In practice, CSM parts last up to five times longer than standard EPDM in outdoor installations and resist swelling in hydraulic fluids by over 90%. Major producers in automotive and construction rely on CSM for gaskets that endure temperature swings from -40°C to +150°C without loss of integrity. Real‑world data from a leading seal manufacturer showed a 30% drop in warranty claims after switching to CSM formulations. Engineers favor CSM not only for performance but also for predictable processing in extrusion and molding equipment, enabling tight tolerances and intricate profiles. Ready for the good part? You’ll learn optimal compounding recipes and cure systems that guarantee uniform dispersion of fillers and consistent crosslink density across batches.
Property | CSM Value | EPDM Comparison |
---|---|---|
Temperature Range | -40°C to +150°C | -50°C to +120°C |
Ozone Resistance | Excellent (1000 hrs) | Good (200 hrs) |
Oil Swell (ASTM) | < 20% | > 100% |
CSM’s design solves key durability challenges. Data proves extended lifespan. Industry adoption validates performance gains.
Chemical Structure and Synthesis Process The molecular design of CSM underpins its outstanding properties. This is where it gets interesting… CSM begins as high-density polyethylene modified via liquid-phase chlorination followed by sulfonation using sulfur dioxide and chlorine gas. Reaction temperatures between 60°C and 90°C and controlled residence times yield target chlorine contents of 20–40% and sulfonyl content of 2–5%. These functional groups enable efficient peroxide or polyfunctional crosslinking during curing. Three commercial routes dominate: batch chlorination in inert solvents, continuous gas-phase chlorination, and melt-phase processes. Each route balances cost, reaction control and residual by‑product removal. For example, gas-phase chlorination offers high throughput but demands robust off‑gas scrubbing systems to capture HCl fumes. Melt-phase methods eliminate solvent usage, aligning with environmental regulations, yet require precise temperature control to avoid polymer degradation.
Synthesis Route | Advantages | Challenges |
Batch Chlorination | High conversion control | Solvent recovery needed |
Gas-phase Chlorination | High throughput | HCl off‑gas management |
Melt-phase Process | No solvents | Thermal degradation risk |
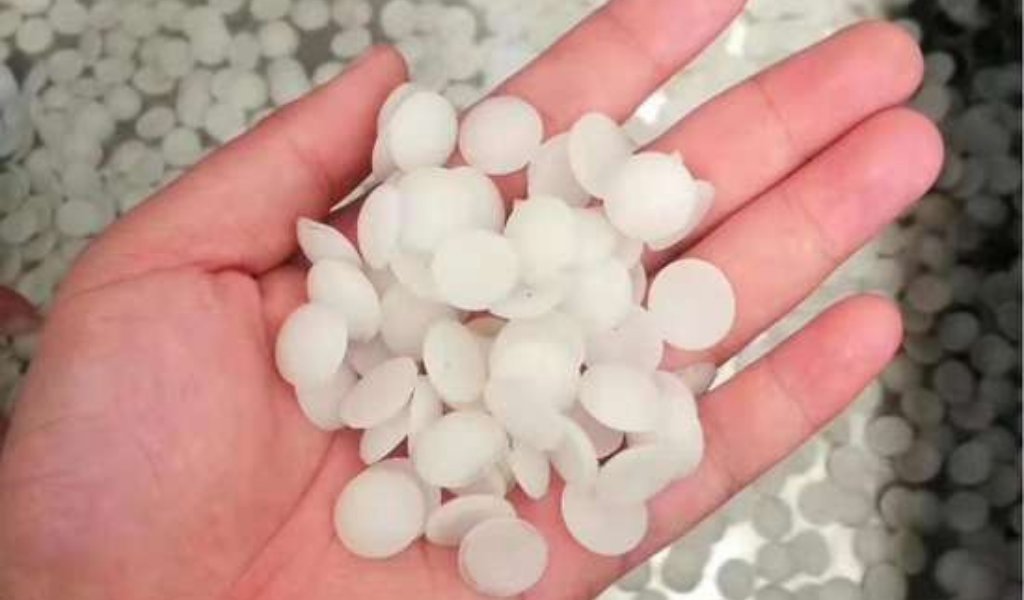
Physical and Mechanical Properties Chlorosulfonated polyethylene displays a blend of flexibility and strength that few elastomers match. But here’s the kicker… Its tensile strengths range from 8 to 20 MPa while elongation at break exceeds 300%, surpassing many specialty rubbers. Shore A hardness scales from 40 to 85, providing design flexibility from soft seals to rigid buffer components. Dynamic mechanical analysis reveals a glass transition near -30°C, ensuring low-temperature flexibility. Abrasion resistance ASTM D5963 values often exceed 100 mm³, making CSM ideal for high‑wear applications like conveyor belting. Compression set numbers under ASTM D395 remain below 20% at 70°C after 22 hours, illustrating excellent resilience. Ready for the good part? Compared to CPE or NBR, CSM retains over 90% of original properties after 500 hours in engine oil. Case studies from a major hose manufacturer show CSM hoses lasting 1.5 million cycles in fatigue tests versus 800k cycles for EPDM equivalents. Designers appreciate how CSM’s mechanical profile aligns with finite‑element simulations, enabling precise life‑prediction models and optimized wall thicknesses.
Property | CSM Typical | NBR Typical |
Tensile Strength | 8–20 MPa | 10–15 MPa |
Elongation at Break | 300–600% | 200–400% |
Hardness (Shore A) | 40–85 | 40–90 |
CSM offers high strength flexibility balance. Data confirms superior fatigue life. Performance models align with test results.
Chemical and Environmental Resistance CSM excels under aggressive chemical exposure. What’s the real story? Many rubbers swell or crack in contact with fuels, acids or ozone. CSM swells less than 20% in ASTM fuel B and resists 1000‑hour ozone exposure at 100 pphm without surface cracking. Acid and alkali immersion tests show weight changes under 5% in 10% HCl or NaOH solutions. Outdoor weathering trials confirm only superficial discoloration after three years in tropical climates. Here’s the deal… These resistances stem from the sulfonated sites that stabilize polymer chains against oxidative attack. A protective microcrystalline phase forms at the surface, deflecting UV photons. For coating applications, CSM basal layers combine with acrylic topcoats for enhanced barrier properties. Ready for the good part? In a real‑world roofing membrane case, CSM formulas outperformed EPDM by retaining 95% of tensile strength after five roofing seasons.
Test Medium | CSM Swell (%) | EPDM Swell (%) |
Fuel B | < 20 | > 100 |
10% HCl | < 5 | > 50 |
Ozone (100 pphm) | 0 (1000 hrs) | 50% cracking |
CSM withstands oils acids UV and ozone. Data proves minimal swelling. Case studies validate long‑term stability.
Conclusion
You’ve seen how chlorosulfonated polyethylene’s unique chemistry underpins unmatched durability elasticity and chemical resistance
But here’s the kicker… that advantage means lower downtime and maintenance costs for your operations
Consider CSM for your next elastomer application and experience proven performance backed by industry standards and decades of field data
Talk with a CSM supplier today to secure material grades tailored for your toughest environments
FAQ
Q1: What is chlorosulfonated polyethylene?
Chlorosulfonated polyethylene (CSM) is a chemically modified polymer offering exceptional chemical resistance and weather stability.
Q2: How does the sulfonation process work?
Sulfonation grafts chlorine and sulfonyl groups onto polyethylene, creating crosslink sites and improved performance.
Q3: What applications suit CSM best?
CSM excels in hoses seals gaskets coatings and any parts exposed to oils UV or ozone.
Q4: How do I choose between CSM and other elastomers?
Compare resistance temperature range mechanical needs and cost among CSM EPDM NBR and CPE options.
Q5: How can I ensure consistent quality?
Implement ASTM ISO testing monitor raw material and use precise compounding curing controls.