The article titled “Exploring Chlorosulfonated Polyethylene Synthetic Rubber” delves into this versatile material that has emerged as a key player in various industrial applications. Chlorosulfonated polyethylene (CSPE) synthetic rubber is renowned for its unique properties, which make it highly suitable for demanding environments. This article will take you through its chemical composition, manufacturing processes, properties, various applications, challenges faced by manufacturers, and current market trends. By the end, you will gain a comprehensive understanding of CSPE and its relevance in modern-day applications.
1. Introduction to Chlorosulfonated Polyethylene Synthetic Rubber
Chlorosulfonated polyethylene synthetic rubber is a synthetic elastomer that results from the chlorosulfonation of polyethylene. It possesses excellent weather resistance, chemical stability, and high elasticity. But here’s the kicker: its unique properties grant it a competitive advantage in applications ranging from construction to automotive industries.
Developed in the 1960s, CSPE has gained traction due to its superior performance characteristics compared to conventional rubber materials. Its chemical structure, enriched with chlorine and sulfur, grants it an impressive thermal stability and resistance against a variety of chemicals. This makes it ideal for use in various harsh environments where other materials may falter.
In this introductory section, we will explore how CSPE stands out within the realm of synthetic rubbers. Understanding the essential characteristics and the rationale behind its global adoption provides context for the deeper discussions to follow regarding its applications and implications.
2. Chemical Composition of CSPE
To grasp the capabilities of chlorosulfonated polyethylene synthetic rubber, it is essential to understand its chemical composition. CSPE is derived from polyethylene, a polymer formed from the polymerization of ethylene. What’s the real story? The magic happens when polyethylene undergoes chlorosulfonation.
During chlorosulfonation, chlorine and sulfur dioxide gases are introduced to the polyethylene, resulting in a chain of sulfonate groups and chlorine atoms incorporated into the main polymer structure. This chemical modification enhances the polymer’s properties, providing improved thermal stability and chemical resistance.
For example, CSPE exhibits a glass transition temperature that allows it to maintain flexibility in colder conditions while not losing structural integrity in elevated temperatures. Additionally, the enhanced cross-linking in the polymer network contributes to its resilience against mechanical stresses.
The concentration of chlorine in CSPE typically ranges between 25% and 35%, which significantly impacts its physical properties. The addition of these halogen atoms introduces polar characteristics, improving compatibility with various fillers and substrates. This understanding of its chemical makeup forms the basis for its wide-ranging industrial applications.
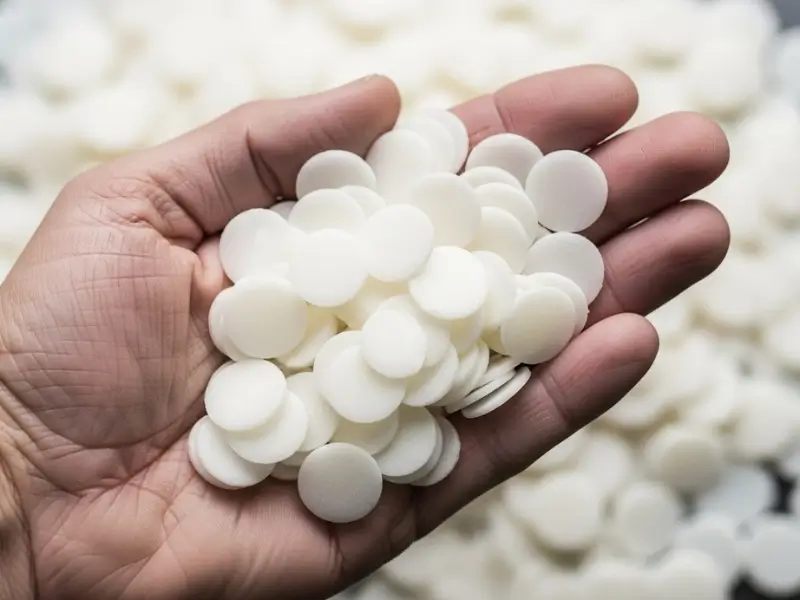
3. Manufacturing Process of CSPE
Now let’s take a closer look at the manufacturing process of chlorosulfonated polyethylene. The journey begins with the preparation of polyethylene, which is the primary raw material. Different grades of polyethylene can be used, depending on the desired final properties of the CSPE.
The initial stage of the manufacturing process calls for the rectification of polyethylene before chlorosulfonation occurs. During chlorosulfonation, the polyethylene is exposed to a gaseous mixture of chlorine and sulfur dioxide under controlled temperatures and pressures. Here’s where it gets interesting—this reactive environment encourages the incorporation of chlorine and sulfonate functional groups into the polymer chain.
Once the chlorosulfonation process is completed, the resulting product undergoes several purification steps to remove unattached chlorines and ensure a high purity level. The kemelization of the CSPE involves drying, milling, and compounding with additives such as stabilizers, plasticizers, and fillers to achieve the desired product characteristics. The final outcome is a high-quality synthetic rubber product that exhibits excellent tensile strength, better strain response, and resistance to harsh environments.
Understanding the manufacturing process sheds light on how manufacturers can influence the final properties of CSPE. The ability to adjust parameters during chlorosulfonation allows for customization to meet specific industry requirements.
4. Properties of Chlorosulfonated Polyethylene
The properties of chlorosulfonated polyethylene synthetic rubber are a primary reason for its widespread use across various industries. CSPE is known for its remarkable resistance to heat, ozone, chemicals, and weather conditions. But what’s the impact of these properties? They culminate in reliability and durability for end-users.
One of the standout properties is its ability to function effectively in extreme temperatures, ranging from -40°F to 250°F. This broad range ensures that CSPE maintains its flexibility and integrity when exposed to fluctuating temperature conditions. Unlike other rubber materials that can become brittle in cold climates or lose shape in heat, CSPE remains dependable, making it suitable for automotive seals and construction applications.
Additionally, CSPE exhibits excellent electrical insulating properties, making it an ideal choice in the electrical industry for applications in wire and cable insulation. Versatility extends to its compatibility with various types of fillers, allowing manufacturers to tailor the mechanical properties of the final product according to specific needs.
Furthermore, CSPE is accompanied by UV resistance properties, which helps to enhance its performance in outdoor applications. The material’s resistance against harsh environmental conditions ensures longevity and reduces the frequency of replacements. Recognizing these key properties helps stakeholders appreciate CSPE’s role in industrial applications.
5. Applications of CSPE
Chlorosulfonated polyethylene’s versatility means it is employed in a wide range of applications across diverse industries. Once you see how many fields utilize CSPE, you might be amazed at its influential role in everyday products.
In the construction sector, CSPE is frequently used for roofing membranes, thanks to its resistance to UV radiation and weather conditions. This ensures that buildings are protected from water infiltration and external elements. Moreover, it’s also prevalent in automotive applications, especially in manufacturing seals, gaskets, and hoses that require highly durable and flexible materials.
Electrical applications benefit significantly from CSPE as well, where it provides excellent insulation for wiring and cables, ensuring safety and performance in harsh environments. Essentially, the automotive and construction sectors are the largest consumers of CSPE, but the usage has extended into the production of durable fabrics, conveyor belts, and even inflatable products.
Ready for the good part? The versatility of CSPE allows it to cross into niche markets too, such as in the manufacturing of medical tubing and linings due to its resistance to a broad spectrum of chemicals.
Thus, as industries continue to evolve, the applications of chlorosulfonated polyethylene synthetic rubber expand accordingly, confirming its status as an indispensable material in modern manufacturing.
6. Advantages of Using CSPE
Several notable advantages make chlorosulfonated polyethylene synthetic rubber a preferred choice among industries. For starters, CSPE’s resistance to oils, chemicals, and moisture sets it apart from many traditional rubber materials. This creates unparalleled durability for products exposed to aggressive substances.
Compared to alternatives like natural rubber or standard synthetics, CSPE often requires less maintenance, thereby resulting in cost savings down the line. The longevity of CSPE products leads to reductions in replacement frequency, contributing to lower overall operational costs for industries dependent on reliable materials.
Moreover, its excellent thermal stability means fewer instances of material failure due to heat or cold exposure. This means added safety and reliability, particularly in applications involving critical components that withstand extreme conditions.
Another significant advantage lies in its versatility. CSPE can be compounded with various fillers, allowing manufacturers to customize its properties to fit specific applications better. This adaptability is a game-changer, making it suitable for industries that have unique or stringent requirements.
But here’s the kicker: sustainability is emerging as a focal point in manufacturing, and CSPE fits the bill. It can often be recycled or reused in various applications, contributing to a circular economy that minimizes material waste. Overall, the compelling advantages of CSPE align with the evolving demands of modern industry.
7. Common Challenges with CSPE
While chlorosulfonated polyethylene synthetic rubber offers a wide range of benefits, it is not without its challenges. Understanding these challenges is crucial for manufacturers and end-users alike.
One of the primary challenges faced by manufacturers involves the production costs associated with CSPE. The manufacturing process is more intricate compared to standard rubber, requiring specialized equipment and expertise. These factors can drive up the initial costs, which may deter smaller companies from considering CSPE as a material option.
Another challenge concerns the technical requirements for processing CSPE. The specific conditions required during chlorosulfonation must be precisely controlled, as any deviations can lead to subpar product quality. This demand for precision means that manufacturers need to invest in quality control mechanisms to maintain consistency.
Additionally, while CSPE is chemically stable, its performance can be affected by extreme environmental conditions if not properly formulated. Stakeholders must ensure that the specific grades of CSPE being utilized are appropriate for the intended application to avoid unexpected failures.
To overcome these challenges, it’s vital for manufacturers to invest in research and development. Innovations in production processes, materials handling, and quality control can assist in alleviating these issues, allowing CSPE to reach its full potential in various applications.
8. Quality Control Measures in CSPE Production
Quality control is essential in the production of chlorosulfonated polyethylene to ensure that the final product meets industry standards and performs reliably. After all, the performance of materials is only as good as the processes behind their manufacture.
The first step in effective quality control begins with the selection of raw materials. The quality of polyethylene and the chemicals used during chlorosulfonation must be scrutinized. Continuous monitoring of supplier performance can help ensure that only high-quality materials enter the production line.
During the production process itself, various tests can be implemented to ascertain quality. Regular sampling and testing at multiple stages, including initial chlorosulfonation and finally, the finished product, helps to identify potential issues early on. Techniques such as spectroscopy and rheological testing can be employed to evaluate the physical and chemical properties of CSPE.
Post-production, rigorous testing of the final products is crucial, including assessments of tensile strength, elasticity, and resistance to chemicals and temperatures. Utilizing internationally recognized certification standards, such as ISO and ASTM, enhances credibility and customer confidence in the product.
The effective implementation of quality control measures ensures that chlorosulfonated polyethylene maintains its high-performance reputation. It not only safeguards the manufacturer’s interests but also assures customers of the reliability and safety of the products they utilize.
9. Environmental Impact of CSPE
As industries become increasingly focused on sustainability, understanding the environmental impact of chlorosulfonated polyethylene is crucial. The production and disposal of synthetic materials like CSPE can have significant environmental ramifications.
Firstly, the chlorosulfonation process involves the use of chlorine and sulfur dioxide, which can produce harmful emissions if not properly managed. It’s essential for manufacturers to implement effective emission control systems to minimize pollutants released into the atmosphere.
Moreover, the concern for plastics and synthetic rubber ends at disposal. While CSPE is durable, this longevity poses challenges in waste disposal, as it does not decompose easily in nature. The implementation of recycling programs aimed at repurposing CSPE can significantly reduce landfill waste and promote a circular economy.
Additionally, manufacturers are increasingly investing in sustainable practices, focusing on using renewable energy sources during the production process, which can reduce overall environmental impacts. By adopting greener processes and materials, CSPE manufacturers can align themselves with global sustainability goals.
It’s clear that while chlorosulfonated polyethylene offers unique advantages, the focus on environmental stewardship is essential for its long-term viability in the market.
10. Innovations in CSPE Technology
The field of synthetic rubber is constantly evolving, and chlorosulfonated polyethylene is no exception. Innovations in CSPE technology are redefining its applications and performance characteristics. Are you ready for the transformation?
One notable advancement involves the incorporation of bio-based additives that enhance the mechanical properties of CSPE while reducing its environmental footprint. These additives can improve flexibility, tensile strength, and chemical resistance, while also aligning with sustainability initiatives.
Another area of innovation lies in the development of specialized grades of CSPE formulated for niche applications, such as fuel resistance for use in the automotive industry. This customization enables manufacturers to address specific performance challenges faced by their clients.
Moreover, advancements in software modeling and simulation are enabling manufacturers to predict the behavior of CSPE products before they are physically made. This allows producers to optimize formulations for targeted applications, subsequently reducing waste and increasing efficiency in production.
Looking ahead, ongoing research into nanotechnology might provide avenues for enhancing the properties of CSPE significantly. These innovations hold the potential to expand the capabilities of CSPE, broadening its application scope across multiple sectors.
11. Comparison of CSPE with Other Rubber Materials
When selecting materials for specific applications, understanding how chlorosulfonated polyethylene stacks up against other rubber materials is critical. What’s the comparison revealing? CSPE demonstrates clear advantages in several key areas.
Compared to natural rubber, CSPE provides superior chemical resistance and environmental stability, making it more suitable for demanding applications. While natural rubber excels in elasticity, it suffers under harsh environmental conditions and chemical exposure, which can lead to rapid degradation.
When comparing CSPE with some synthetic rubbers, CSPE generally emerges as a more cost-effective alternative. Its durability and low maintenance needs can drive down long-term costs, even when its initial prices may be higher.
Another noteworthy comparison is with EPDM (ethylene propylene diene monomer) rubber. EPDM is well-regarded for its weather resistance, and while CSPE rivals it in this area, CSPE offers additional benefits such as superior oil and chemical resistance, thereby attracting specific applications across different industries.
Understanding the distinct characteristics of CSPE compared to other rubber materials aids manufacturers in making informed decisions regarding material selection based on specific requirements and applications.
12. Market Trends and Demand for CSPE
The market for chlorosulfonated polyethylene synthetic rubber is experiencing significant growth, driven by various trends across multiple sectors. Are you curious about what’s fueling this demand?
One of the key factors contributing to the increased demand is the expansion of the automotive industry. As vehicles become more advanced, the need for high-performance sealing materials like CSPE is surging. Its excellent elasticity and resistance to wear make it a top choice for automotive applications.
In addition, the construction sector is witnessing a robust growth trajectory. CSPE is increasingly being specified for roofing systems, membranes, and other durable building materials. The growing focus on sustainability and energy efficiency in buildings is also driving its adoption.
Another trend influencing the CSPE market is the rising consumer demand for environmentally friendly products. Manufacturers are responding by developing CSPE products that incorporate sustainable practices and materials, boosting their market appeal.
Moreover, as emerging economies invest in infrastructure and industrialization, the demand for CSPE is expected to grow. This trend highlights the importance of staying agile and responsive to market needs, paving the way for future innovations within the CSPE sector.
13. Case Studies of CSPE Applications
Examining real-world applications of chlorosulfonated polyethylene helps to illuminate its practical benefits. Let’s dive into some case studies that highlight its use in various industries.
In the construction industry, a notable project involved the use of CSPE roofing membranes in a large industrial complex. The durability and weather resistance of CSPE ensured that the roofing system maintained integrity throughout extreme weather conditions, significantly reducing maintenance costs over the lifespan of the building.
Another interesting example can be found in the automotive sector, where a major car manufacturer integrated CSPE seals in their electric vehicle line. The application of CSPE helped ensure optimal performance by preventing leaks and maintaining reliability even under high-performance scenarios.
In the electrical industry, an innovative cable manufacturer adopted CSPE for their insulating jackets. By utilizing CSPE, they achieved enhanced electrical properties and extended service life compared to traditional materials.
These case studies reflect CSPE’s versatility and effectiveness across different applications, demonstrating its value in addressing specific challenges faced by various industries.
14. Myths and Misconceptions about CSPE
As with any material, various myths and misconceptions surround chlorosulfonated polyethylene. Understanding these myths is crucial for stakeholders to make informed decisions. One prevalent myth is that CSPE is a high-cost alternative that offers no significant benefits over traditional rubber materials.
In reality, while the initial costs might be higher, CSPE’s durability and low maintenance needs can lead to lower total costs in the long term.
Another misconception is that CSPE is not environmentally friendly. In contrast, many manufacturers are implementing sustainable practices to minimize environmental impact through recycling and responsible disposal methods.
Additionally, some may believe that CSPE isn’t suitable for high-temperature applications. However, CSPE can effectively function in a range of temperatures, providing reliable performance in various operating conditions.
Addressing these myths through education and awareness can enhance understanding and acceptance of CSPE, encouraging its broader adoption across industries.
15. Conclusion
In conclusion, chlorosulfonated polyethylene synthetic rubber is a standout material in the realm of elastomers, renowned for its exceptional properties and versatility. Throughout this article, we’ve explored its chemical composition, manufacturing processes, numerous applications, and advantages. The insights gathered create a comprehensive picture of how CSPE is redefining standards across various sectors.
Looking ahead, the growth of CSPE within established and emerging markets promises further innovations and applications. As industries increasingly prioritize sustainability and high-performance materials, the significance of chlorosulfonated polyethylene will only strengthen. This makes it essential for industry professionals to stay informed about the dynamics surrounding this remarkable material.
FAQ Section
Q1: What is chlorosulfonated polyethylene synthetic rubber?
Chlorosulfonated polyethylene synthetic rubber is a synthetic elastomer known for its chemical resistance, durability, and flexibility, used in various industrial applications.
Q2: How is chlorosulfonated polyethylene manufactured?
CSPE is produced by chlorosulfonating polyethylene through a controlled reaction with chlorine and sulfur dioxide, followed by purification and compounding processes.
Q3: What are the primary applications of CSPE?
CSPE is widely used in construction, automotive components, electrical insulation, and various durable consumer products due to its outstanding performance characteristics.
Q4: What advantages does CSPE have over other synthetic rubbers?
CSPE offers superior chemical resistance, thermal stability, and lower long-term maintenance costs compared to traditional synthetic rubbers such as natural rubber and EPDM.
Q5: What environmental concerns are associated with CSPE?
Concerns include emissions during production and challenges in waste disposal. However, sustainable practices, recycling, and responsible production methods can mitigate these impacts.