In today’s demanding industrial and construction environments, material selection can make the difference between project success and costly failure. Among the diverse array of thermoplastics available to engineers and contractors, Chlorinated Poly Vinyl Chloride (CPVC) stands out for its exceptional performance characteristics and versatility. This high-performance thermoplastic has revolutionized numerous applications, from industrial process piping to residential plumbing systems, offering solutions where traditional materials fall short. This comprehensive guide explores the essential aspects of CPVC, providing professionals with the knowledge needed to make informed decisions about this increasingly important material.
1. Introduction to Chlorinated Poly Vinyl Chloride (CPVC)
Chlorinated Poly Vinyl Chloride, commonly abbreviated as CPVC, represents a significant advancement in thermoplastic technology. At its core, CPVC is a specialized thermoplastic material derived from polyvinyl chloride (PVC) through a post-production chlorination process. This process increases the chlorine content of the polymer from approximately 57% in standard PVC to around 63-69% in CPVC. This seemingly modest chemical modification dramatically transforms the material’s performance characteristics, particularly its temperature resistance, chemical durability, and mechanical properties. The resulting thermoplastic offers exceptional performance in applications where standard PVC would quickly degrade or fail, opening new possibilities across multiple industries.
But here’s the kicker… While CPVC might appear to be just another plastic variant to the uninitiated, its development represents one of the most significant innovations in thermoplastic history. The material’s journey began in the 1950s when researchers sought to overcome the temperature limitations of standard PVC. By the 1960s, commercial production of CPVC was underway, with early applications focused on industrial piping systems where corrosion resistance and temperature tolerance were paramount. The subsequent decades saw continuous refinement of CPVC formulations and manufacturing processes, expanding its applications and improving its performance characteristics. Today’s CPVC products bear little resemblance to their early predecessors, incorporating advanced stabilization packages, processing aids, and performance enhancers that extend service life and reliability.
Within the broader thermoplastics industry, CPVC occupies a unique position. It bridges the gap between commodity plastics like PVC and high-performance engineering thermoplastics such as PEEK or PVDF. This middle ground makes CPVC particularly valuable in applications where the cost of premium engineering plastics cannot be justified, but the performance limitations of standard thermoplastics cannot be accepted. The material competes not only with other thermoplastics but also with traditional materials like copper, stainless steel, and various alloys in many applications. Its growth trajectory remains strong, with global CPVC consumption increasing steadily as more industries recognize its advantages and new applications emerge. The material’s balance of performance, processability, and cost-effectiveness ensures its continued relevance in an increasingly competitive materials landscape.
Property | CPVC | Standard PVC | Significance |
---|---|---|---|
Chlorine Content | 63-69% | 56-57% | Higher chlorine content improves temperature resistance |
Maximum Service Temperature | 200°F (93°C) | 140°F (60°C) | Enables hot water and higher temperature applications |
Chemical Resistance | Excellent | Good | Withstands more aggressive chemicals and environments |
Tensile Strength | 55-60 MPa | 45-55 MPa | Greater structural integrity under stress |
Glass Transition Temperature | 239-275°F (115-135°C) | 180°F (82°C) | Maintains rigidity at higher temperatures |
2. The Chemical Structure and Properties of CPVC
The molecular architecture of CPVC provides the foundation for its exceptional performance characteristics. At the most fundamental level, CPVC consists of a carbon backbone with alternating chlorine atoms and hydrogen atoms attached. The chlorination process that transforms PVC into CPVC introduces additional chlorine atoms, replacing some of the hydrogen atoms along the polymer chain. This substitution is not uniform but occurs randomly along the chain, creating an amorphous polymer structure. The increased chlorine content—reaching up to 69% by weight in some formulations—significantly alters the material’s physical and chemical behavior by changing the electron density distribution and increasing the steric hindrance between polymer chains.
What’s the real story? The transformation from PVC to CPVC through chlorination fundamentally changes how the polymer responds to thermal energy. The additional chlorine atoms increase the energy required to initiate chain movement, effectively raising the glass transition temperature (Tg) from approximately 82°C for PVC to between 115-135°C for CPVC. This higher Tg translates directly to improved heat resistance, allowing CPVC to maintain its structural integrity and mechanical properties at temperatures that would cause standard PVC to soften and deform. Additionally, the chlorination process affects the polymer’s solubility parameters, altering its compatibility with solvents, adhesives, and other chemicals. This change in solubility behavior necessitates specialized solvent cements for joining CPVC components, distinct from those used with standard PVC.
The physical and chemical properties that define CPVC make it uniquely suited for demanding applications. Its heat distortion temperature typically exceeds 100°C, allowing it to handle hot water and other heated fluids without deformation. The material exhibits excellent resistance to acids, bases, salts, and aliphatic hydrocarbons, though it can be attacked by some ketones, esters, and aromatic hydrocarbons. Mechanically, CPVC offers good tensile strength (typically 55-60 MPa), moderate impact resistance (though less than some other thermoplastics), and excellent long-term hydrostatic strength, critical for pressure piping applications. Its inherent flame retardancy—with a limiting oxygen index (LOI) often exceeding 60%—provides safety advantages in many installations. The material also features low thermal conductivity, reducing heat loss in hot fluid applications and minimizing condensation on cold surfaces. These properties, combined with good processability and reasonable cost, have established CPVC as a material of choice across diverse applications where performance under stress is non-negotiable.
Property | Value for CPVC | Practical Implication |
---|---|---|
Glass Transition Temperature | 115-135°C | Maintains rigidity in hot water applications |
Limiting Oxygen Index | >60% | Self-extinguishing, enhances fire safety |
Thermal Conductivity | 0.14 W/m·K | Reduces heat loss, energy efficient |
Specific Gravity | 1.5-1.6 | Heavier than water, lighter than metals |
Coefficient of Linear Thermal Expansion | 6.7 × 10^-5 cm/cm/°C | Requires accommodation for thermal expansion |
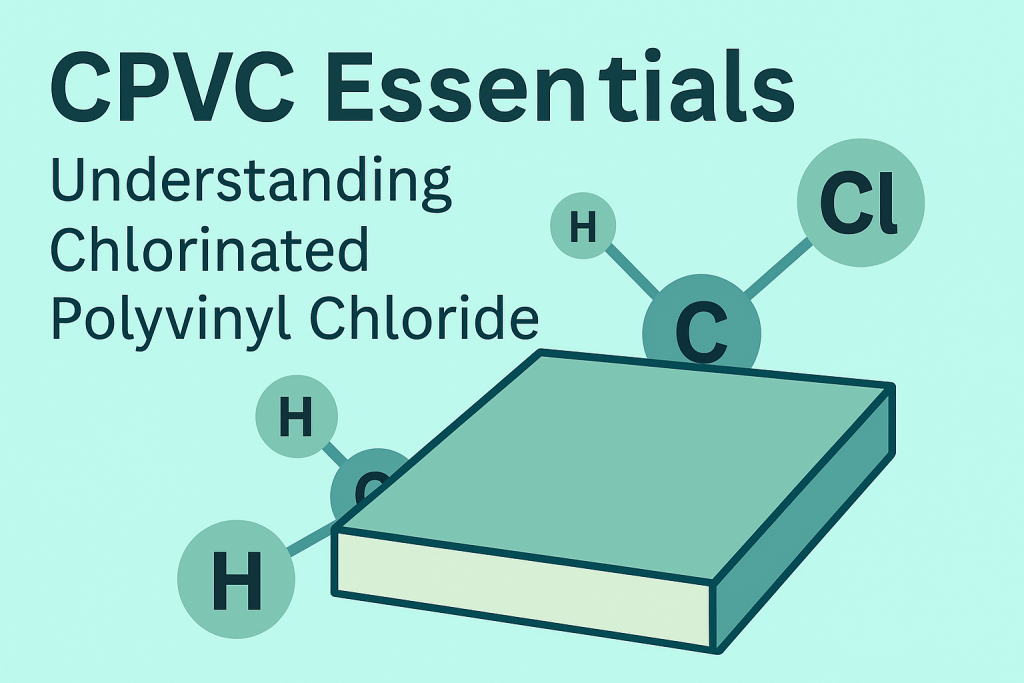
3. Manufacturing Process of CPVC
The journey from raw materials to finished CPVC products involves sophisticated chemical processes and precision manufacturing techniques. The production begins with standard PVC resin, typically produced through suspension polymerization of vinyl chloride monomer (VCM). This base PVC resin serves as the starting material for the chlorination process. Additional raw materials include the chlorinating agents (usually chlorine gas or liquid chlorine), reaction initiators, and various catalysts that facilitate the chlorination reaction. The quality of these starting materials significantly influences the properties of the final CPVC compound, with manufacturers carefully selecting PVC resins with specific molecular weights and particle characteristics to optimize the chlorination process and subsequent processing.
This is where it gets interesting… The chlorination of PVC can follow several different methodologies, each with distinct advantages and limitations. The solution method involves dissolving PVC resin in a chlorinated solvent such as carbon tetrachloride or chlorobenzene, then introducing chlorine gas while the solution is exposed to ultraviolet light, which acts as an energy source to initiate the substitution reaction. The fluidized bed method suspends PVC particles in a stream of nitrogen gas, creating a fluid-like bed of particles that are then exposed to chlorine gas under controlled temperature and UV radiation. The slurry method, perhaps the most common, disperses PVC resin in an inert chlorinated solvent and introduces chlorine gas under carefully controlled conditions. Each method produces CPVC with slightly different chlorine distribution patterns and physical properties, allowing manufacturers to tailor the material for specific applications.
Following the chlorination process, the raw CPVC resin undergoes compounding—a critical step that transforms the base polymer into a processable material with application-specific properties. During compounding, manufacturers incorporate various additives, including heat stabilizers to prevent degradation during processing and service, impact modifiers to improve toughness, processing aids to enhance flowability, UV stabilizers for outdoor applications, pigments for color, and fillers to modify physical properties or reduce cost. The precise formulation varies significantly depending on the intended application, with industrial piping grades typically prioritizing chemical resistance and temperature performance, while plumbing grades might emphasize long-term hydrostatic strength and potable water safety.
Quality control measures permeate every stage of CPVC production, ensuring consistency and reliability in the final product. Manufacturers employ sophisticated analytical techniques to monitor chlorine content, molecular weight distribution, and residual impurities in the base resin. During compounding, rheological testing assesses flow characteristics, while thermal analysis confirms proper stabilization. Finished products undergo rigorous testing for mechanical properties, pressure ratings, and chemical resistance according to industry standards such as ASTM D1784 for material classification and ASTM F441 for pressure pipe. Many manufacturers implement statistical process control (SPC) methodologies to identify and address variations before they affect product quality. For applications involving potable water, additional testing ensures compliance with health and safety standards such as NSF/ANSI 61. This comprehensive quality assurance framework ensures that CPVC products deliver consistent performance across their intended service life, even under challenging conditions.
4. Key Performance Characteristics of CPVC
The temperature resistance of CPVC stands as one of its defining advantages, particularly when compared to standard PVC and many other thermoplastics. With a maximum recommended service temperature of approximately 200°F (93°C) for pressure applications, CPVC can handle hot water and heated industrial fluids that would quickly degrade standard PVC, which is typically limited to 140°F (60°C). This enhanced thermal performance stems directly from the material’s higher chlorine content and resulting increased glass transition temperature. The practical implications of this temperature resistance are far-reaching, enabling CPVC to serve in hot water distribution systems, heated chemical processing lines, and industrial applications where elevated temperatures are unavoidable. Even more impressive is CPVC’s ability to maintain its pressure-bearing capability at elevated temperatures, with properly designed systems rated for continuous operation at temperatures approaching its maximum service temperature.
Ready for the good part? CPVC’s chemical resistance profile makes it an exceptional performer in corrosive environments that would rapidly deteriorate many metals and other plastics. The material exhibits excellent resistance to a wide range of acids, including strong mineral acids like sulfuric and hydrochloric acid, as well as organic acids commonly found in industrial processes. It similarly withstands most alkalis, salts, aliphatic hydrocarbons, and alcohols, even at elevated concentrations and temperatures. This broad chemical compatibility enables CPVC to transport aggressive chemicals in industrial settings, handle chlorinated water in treatment facilities, and resist degradation from cleaning chemicals in commercial buildings. However, it’s important to note that CPVC does have chemical limitations—certain ketones, esters, and aromatic hydrocarbons can attack the material, causing swelling, softening, or stress cracking. Manufacturers typically provide detailed chemical resistance guides that account for concentration, temperature, and exposure duration to help engineers select appropriate materials for specific chemical environments.
The mechanical strength and durability of CPVC contribute significantly to its long-term performance in demanding applications. The material offers good tensile strength, typically ranging from 55-60 MPa (8,000-8,700 psi), allowing it to withstand internal pressure and external loads. Its flexural modulus—a measure of stiffness—is higher than many other thermoplastics, providing good resistance to deformation under load. While CPVC’s impact resistance is moderate compared to some engineered thermoplastics, modern formulations often incorporate impact modifiers that significantly improve toughness without compromising other properties. Perhaps most important for pressure piping applications is CPVC’s excellent long-term hydrostatic strength, which determines its pressure-bearing capability over decades of service. This property is carefully evaluated through standardized testing, with results used to establish pressure ratings and design factors that ensure safe, reliable performance throughout the material’s service life.
Fire resistance represents another significant advantage of CPVC, particularly in building applications where safety is paramount. The material’s high chlorine content makes it inherently flame retardant, with a Limiting Oxygen Index (LOI) typically exceeding 60%—meaning it requires an oxygen-rich environment to sustain combustion. When exposed to flame, CPVC tends to char rather than melt and drip, potentially limiting fire spread. It also generates less smoke than many other thermoplastics when burned. These characteristics have led to CPVC’s approval for fire sprinkler systems in many jurisdictions, where its combination of corrosion resistance and fire performance offers advantages over traditional metallic systems. However, it’s important to note that specific fire performance can vary based on formulation, and proper installation according to applicable fire codes remains essential for any building material.
Performance Characteristic | Rating | Applications Benefiting from This Property |
---|---|---|
Temperature Resistance | Excellent (up to 200°F/93°C) | Hot water plumbing, industrial process piping, heated chemical transport |
Chemical Resistance | Very Good to Excellent | Chemical processing, water treatment, industrial waste handling |
Pressure Rating at 73°F (23°C) | Up to 1,000 psi (Schedule 80) | High-pressure industrial applications, water distribution |
Fire Performance (LOI) | >60% | Fire sprinkler systems, plenum applications, building safety systems |
Expected Service Life | 50+ years | Infrastructure, building systems, long-term installations |
5. Common Applications of CPVC in Industrial Settings
Industrial piping systems represent one of the most significant applications for CPVC, leveraging the material’s unique combination of temperature resistance, chemical durability, and cost-effectiveness. In chemical processing facilities, CPVC pipes and fittings transport a wide range of corrosive substances that would rapidly deteriorate metallic piping, including acids, bases, salt solutions, and oxidizing agents. The material’s inertness prevents contamination of sensitive process chemicals while eliminating concerns about corrosion-induced leaks or failures. In semiconductor manufacturing, where ultra-pure water and chemicals are essential, CPVC’s smooth interior surface and excellent chemical resistance help maintain the required purity levels. Water treatment plants utilize CPVC for chlorine injection lines, filter feed systems, and chemical distribution networks, benefiting from the material’s resistance to chlorine and other water treatment chemicals that would attack most metals.
But here’s the kicker… High-temperature fluid handling represents a specialized niche where CPVC excels beyond most cost-effective alternatives. With its ability to handle continuous temperatures up to 200°F (93°C) while maintaining pressure ratings and chemical resistance, CPVC serves in applications where standard PVC would quickly fail. Hot deionized water systems in electronics manufacturing, heated chemical transfer lines in processing facilities, and elevated temperature waste streams in industrial operations all benefit from CPVC’s thermal stability. The material’s low thermal conductivity—approximately 1/300th that of copper—reduces heat loss in hot fluid applications, potentially improving energy efficiency in industrial processes. This thermal insulating property also minimizes condensation on cold lines, reducing corrosion risks to surrounding equipment and structures. For facilities with both hot and cold fluid requirements, CPVC’s broad temperature range allows standardization on a single piping material, simplifying inventory management and installation practices.
Corrosive environment applications highlight CPVC’s exceptional durability under challenging conditions. In metal plating operations, where highly aggressive acids and electrolytes are commonplace, CPVC equipment resists degradation while maintaining process purity. Chemical manufacturing facilities utilize CPVC for reactor vessel linings, transfer piping, and storage tank components exposed to corrosive intermediates and products. Mining operations employ CPVC for acid leaching systems, where its resistance to both the chemicals and abrasive slurries provides reliable performance. In marine and coastal industrial facilities, CPVC withstands the corrosive effects of saltwater and salt spray that rapidly attack many metallic components. Wastewater treatment plants rely on CPVC for handling effluent containing residual chemicals, biological materials, and varying pH levels. The material’s broad chemical resistance profile makes it particularly valuable in facilities processing multiple chemicals, where a single material solution simplifies design and reduces the risk of installation errors.
Specialized industrial equipment components made from CPVC extend beyond simple piping systems to include custom-engineered products for specific applications. Pump components—including housings, impellers, and valves—benefit from CPVC’s chemical resistance and dimensional stability, particularly in chemical transfer applications. Tower packing and column internals for chemical processing leverage the material’s lightweight, corrosion resistance, and temperature tolerance. Heat exchangers for corrosive fluids utilize CPVC tubes and shells to prevent contamination and extend service life. Industrial ventilation systems for corrosive fumes employ CPVC ductwork and scrubber components to resist degradation from acid gases and other aggressive emissions. Electroplating racks and fixtures benefit from the material’s electrical insulating properties and chemical resistance. These specialized applications often involve custom formulations and fabrication techniques tailored to specific operating conditions, demonstrating the versatility of CPVC as an engineering material in industrial settings where performance under extreme conditions is essential.
FAQ Section
Q1: What is Chlorinated Poly Vinyl Chloride (CPVC) and how does it differ from regular PVC?
CPVC is a thermoplastic produced by chlorination of polyvinyl chloride (PVC) resin. The additional chlorination process increases the chlorine content from approximately 57% in PVC to around 63-69% in CPVC. This molecular change significantly enhances temperature resistance (up to 200°F/93°C compared to PVC’s 140°F/60°C), improves chemical resistance, and increases strength and durability. The higher chlorine content alters the material’s properties, making CPVC suitable for applications where regular PVC would fail, particularly in hot water systems, industrial chemical processing, and high-temperature environments.
Q2: How long does CPVC piping typically last when properly installed?
Properly installed CPVC piping systems typically have an expected service life of 50+ years under normal operating conditions. This longevity depends on several factors including proper installation techniques, operating within specified temperature and pressure ratings, chemical compatibility with transported fluids, and environmental conditions. CPVC’s inherent resistance to corrosion, scaling, and pitting contributes significantly to its long-term durability. Many manufacturers offer warranties ranging from 10 to 30 years, though the actual service life often exceeds these warranty periods when installation best practices are followed and the system operates within design parameters.
Q3: Is CPVC safe for drinking water applications?
Yes, CPVC has been used safely in residential and commercial drinking water systems for over 50 years. The material does not support bacterial growth, does not corrode or scale like metal pipes, and maintains water quality over its service life when properly installed and maintained.
Q4: What are the main advantages and disadvantages of using CPVC instead of metal piping?
The main advantages of CPVC over metal piping include: superior corrosion resistance eliminating the need for water treatment or cathodic protection; lighter weight (about 1/6 the weight of copper) reducing installation labor and structural support requirements; lower thermal conductivity providing energy efficiency and reducing condensation; lower material cost compared to copper and stainless steel; and smoother interior surfaces that reduce friction losses and prevent scale buildup. The primary disadvantages include: lower impact resistance, especially at lower temperatures; higher thermal expansion requiring proper accommodation in design; potential for UV degradation when exposed to sunlight; temperature limitations compared to some metals; and potentially higher environmental impact at end-of-life due to limited recycling infrastructure for CPVC compared to metals.
Q5: What special considerations should be taken when installing CPVC in extreme temperature environments?
When installing CPVC in extreme temperature environments, several special considerations are essential: For hot environments, ensure the maximum operating temperature never exceeds the material’s rating (typically 200°F/93°C for pressure applications); provide adequate support with proper spacing to prevent sagging; use expansion loops, offsets, or expansion joints to accommodate thermal expansion (CPVC expands about 1 inch per 50 feet per 50°F temperature increase); and protect from direct UV exposure. For cold environments, be aware that CPVC becomes more brittle below freezing; avoid impact during installation in cold conditions; provide proper insulation to prevent freezing of contained liquids; and consider the transition between temperature extremes which may require special design accommodations. In all cases, follow manufacturer-specific installation guidelines which may have additional requirements for extreme conditions.