Chlorinated Polyvinyl Chloride (CPVC) has revolutionized modern construction, industrial applications, and plumbing systems worldwide. This enhanced thermoplastic offers exceptional performance characteristics that make it increasingly preferred over traditional materials in demanding applications. This comprehensive guide explores the fundamental aspects of CPVC, from its composition and manufacturing to practical applications and installation best practices.
1.Introduction to Chlorinated Polyvinyl Chloride
Chlorinated Polyvinyl Chloride, commonly known as CPVC, represents a significant advancement in thermoplastic technology. This specialized material is produced through the chlorination of polyvinyl chloride (PVC) resin, a process that fundamentally transforms its performance capabilities. The additional chlorination increases the chlorine content from approximately 57% in standard PVC to around 63-69% in CPVC.
What’s the real story behind this seemingly minor molecular modification? This chemical transformation creates remarkable enhancements in thermal stability, chemical resistance, and mechanical properties that standard PVC simply cannot match. The additional chlorine atoms strengthen the molecular bonds, requiring significantly more energy to break them.
CPVC’s commercial development began in the 1950s, but it wasn’t until the 1970s that it gained widespread adoption. The material’s exceptional heat resistance made it an attractive alternative to copper piping in hot water applications, addressing corrosion issues while offering cost advantages.
When comparing CPVC to standard PVC, the differences become immediately apparent in performance metrics. While both share a similar base structure, CPVC’s additional chlorine content allows it to withstand temperatures up to 200°F (93°C), significantly higher than PVC’s maximum rating of 140°F (60°C).
Property | CPVC | Standard PVC | Advantage |
---|---|---|---|
Maximum Temperature | 200°F (93°C) | 140°F (60°C) | CPVC offers 60°F higher temperature resistance |
Chlorine Content | 63-69% | ~57% | Higher chlorine content improves chemical resistance |
Chemical Resistance | Excellent | Good | CPVC resists more aggressive chemicals |
Pressure Rating at 73°F | 400 psi (2″ pipe) | 315 psi (2″ pipe) | CPVC provides higher pressure capacity |
Cost | Moderate | Lower | PVC is more economical for cold applications |
2.The Manufacturing Process of CPVC
The production of CPVC begins with high-quality PVC resin as the foundational material. This resin consists of fine particles that provide optimal surface area for the subsequent chlorination reaction. The manufacturing process involves several carefully controlled stages to ensure consistent quality and performance.
The chlorination process itself represents the defining step in CPVC production. During this critical phase, the PVC resin is exposed to chlorine gas in a specialized reaction chamber under precisely controlled conditions. As the reaction progresses, chlorine atoms bond to the PVC polymer chains, replacing hydrogen atoms and creating the enhanced CPVC molecular structure.
Here’s something you might not know about this process: temperature control during chlorination is absolutely critical—too high, and the polymer chains may degrade; too low, and the reaction may be incomplete or inconsistent. Modern manufacturing facilities employ sophisticated monitoring systems to maintain optimal conditions throughout the chlorination process.
Following chlorination, the material undergoes compounding, where stabilizers, modifiers, colorants, and other additives are incorporated to enhance specific properties. These additives can improve UV resistance, impact strength, processability, and long-term stability of the final product.
Quality control measures are extensive throughout CPVC manufacturing. Manufacturers regularly test samples for chlorine content, molecular weight distribution, thermal stability, and mechanical properties. Advanced techniques such as infrared spectroscopy help ensure that each batch meets rigorous performance standards.
Manufacturing Stage | Process Details | Quality Control Measures |
---|---|---|
Raw Material Selection | High-quality PVC resin with optimal particle size | Particle size analysis, purity testing |
Chlorination | Exposure to chlorine gas under controlled conditions | Chlorine content verification, reaction monitoring |
Compounding | Addition of stabilizers, modifiers, and colorants | Additive distribution testing, thermal stability checks |
Extrusion/Molding | Formation into pipes, fittings, or sheets | Dimensional accuracy, surface quality inspection |
Final Testing | Performance verification | Pressure testing, impact resistance, chemical compatibility |
3.Key Properties and Characteristics of CPVC
CPVC’s enhanced molecular structure grants it several superior performance characteristics that make it suitable for applications where standard PVC or other materials would quickly fail. These properties have established CPVC as a material of choice in numerous demanding environments.
Temperature resistance is perhaps CPVC’s most notable advantage in practical applications. With the ability to handle continuous operating temperatures up to 200°F (93°C), CPVC can safely transport hot water and other heated substances that would quickly degrade standard PVC. But here’s the kicker: unlike metal pipes that conduct heat rapidly, CPVC’s low thermal conductivity (about 1/300th that of copper) provides natural insulation, reducing heat loss in hot water lines.
Chemical resistance represents another defining characteristic of CPVC that sets it apart from alternatives. The material demonstrates excellent resistance to many acids, bases, salts, and aliphatic hydrocarbons. This chemical inertness makes CPVC ideal for transporting aggressive industrial chemicals and for use in corrosive environments where metals would rapidly deteriorate.
Mechanical strength and durability factors also distinguish CPVC from alternatives in long-term performance. The material offers high tensile strength (approximately 55-80 MPa), good flexural modulus, and excellent creep resistance under load. These properties ensure that CPVC components maintain their structural integrity over decades of service.
Fire resistance represents another significant advantage of CPVC in safety-critical applications. The material has an oxygen index of around 60%, meaning it requires high oxygen concentrations to sustain combustion. When exposed to flame, CPVC tends to char rather than melt and drip, limiting fire spread.
Property | CPVC Value | Significance in Applications |
---|---|---|
Maximum Operating Temperature | 200°F (93°C) | Enables hot water distribution and heated chemical transport |
Tensile Strength | 55-80 MPa | Provides structural integrity under pressure and external loads |
Thermal Conductivity | 0.14 W/m·K | Offers natural insulation, reducing heat loss and condensation |
Oxygen Index | ~60% | Enhances fire safety through self-extinguishing properties |
Chemical Resistance | pH 1-13 | Allows transport of acidic and basic solutions without degradation |
4.Common Applications and Uses of CPVC
CPVC’s unique combination of properties has led to its adoption across numerous industries and applications, with plumbing systems representing one of its most widespread and successful implementations. The material’s versatility continues to expand its market presence.
In plumbing and water distribution systems, CPVC has become a standard material for both residential and commercial buildings worldwide. This is where it gets interesting: CPVC plumbing systems don’t experience the pinhole leaks, scale buildup, or green staining common with copper pipes, resulting in cleaner water and longer service life. The material’s natural insulation properties also reduce condensation on cold water lines and minimize heat loss in hot water distribution.
Industrial applications leverage CPVC’s chemical resistance and temperature stability for critical processes. The material is commonly used for chemical processing equipment, including pipes, valves, pumps, and tanks that handle corrosive substances. In semiconductor manufacturing, ultra-pure CPVC components help maintain the integrity of sensitive processes where even minute contamination could be catastrophic.
Fire sprinkler systems represent another critical application where CPVC excels in protecting lives and property. The material’s flame resistance, reliability, and cost-effectiveness have made it the preferred choice for many residential and light commercial fire protection installations. CPVC fire sprinkler systems can be installed more quickly than metal alternatives, reducing construction costs while maintaining strict compliance with life safety codes.
Hot and cold water distribution in buildings benefits from CPVC’s thermal insulation properties in multiple ways. Want to know the best part? This insulating quality reduces condensation on cold water lines, minimizing the risk of water damage to surrounding building materials. In healthcare facilities, CPVC’s smooth interior surface resists biofilm formation, helping maintain water quality in critical care environments.
Application | CPVC Advantages | Common Alternatives | Key Differentiators |
---|---|---|---|
Hot Water Plumbing | Temperature resistance to 200°F, no corrosion | Copper, PEX | Lower cost, no scaling, better insulation |
Chemical Processing | Excellent chemical resistance, no contamination | Stainless steel, lined steel | Lower cost, lighter weight, easier installation |
Fire Sprinkler Systems | Self-extinguishing, corrosion resistant | Steel, copper | Faster installation, no corrosion concerns |
Semiconductor Processing | Ultra-pure options, no particle shedding | PFA, PVDF | Cost-effective for many applications |
Industrial Waste Lines | Chemical resistance, long service life | Stainless steel, fiberglass | Lower cost, easier modifications |
5.Advantages of CPVC Over Alternative Materials
When comparing CPVC to alternative materials like copper, steel, or other plastics, several advantages become apparent that explain its growing market share across multiple industries. These benefits extend beyond initial material costs to include installation efficiency and long-term performance.
Cost-effectiveness represents a primary benefit, particularly when compared to metals in both material and installation expenses. CPVC material costs are generally 30-50% lower than copper and stainless steel, and these savings extend to installation as well. Let me explain why this matters: in large commercial projects, these combined savings can reduce total installed costs by 30-60% compared to metallic systems, creating significant project budget advantages.
Longevity and lifecycle considerations further strengthen CPVC’s value proposition in long-term facility planning. With proper installation, CPVC systems routinely last 50+ years without degradation in performance. The material doesn’t corrode, scale, or pit like metal pipes, maintaining consistent flow rates throughout its service life. This durability translates to fewer repairs, replacements, and associated costs over the building lifecycle.
Installation ease and flexibility provide additional advantages that accelerate construction schedules. CPVC can be cut with simple hand tools and joined using solvent cement welding, a process that creates bonds stronger than the pipe itself. The truth is, this joining method is not only faster than traditional metal pipe connections but also more reliable when properly executed. The material’s lighter weight reduces worker fatigue and enables faster installation.
Environmental impact and sustainability factors are increasingly important considerations in material selection. CPVC production requires less energy than metal pipe manufacturing, and its lighter weight reduces transportation-related carbon emissions. The material’s exceptional durability means fewer replacements and less waste over time. Additionally, CPVC’s energy-efficient insulating properties reduce operational carbon footprint throughout the building lifecycle.
Comparison Factor | CPVC | Copper | Steel | PVC |
---|---|---|---|---|
Material Cost | Moderate | High | Moderate-High | Low |
Installation Labor | Low | High | Very High | Low |
Expected Lifespan | 50+ years | 25-40 years | 30-50 years | 40+ years |
Corrosion Resistance | Excellent | Poor-Moderate | Poor | Excellent |
Heat Loss | Low | High | High | Low |
Weight (2″ pipe per 10ft) | ~3.5 lbs | ~20 lbs | ~35 lbs | ~3 lbs |
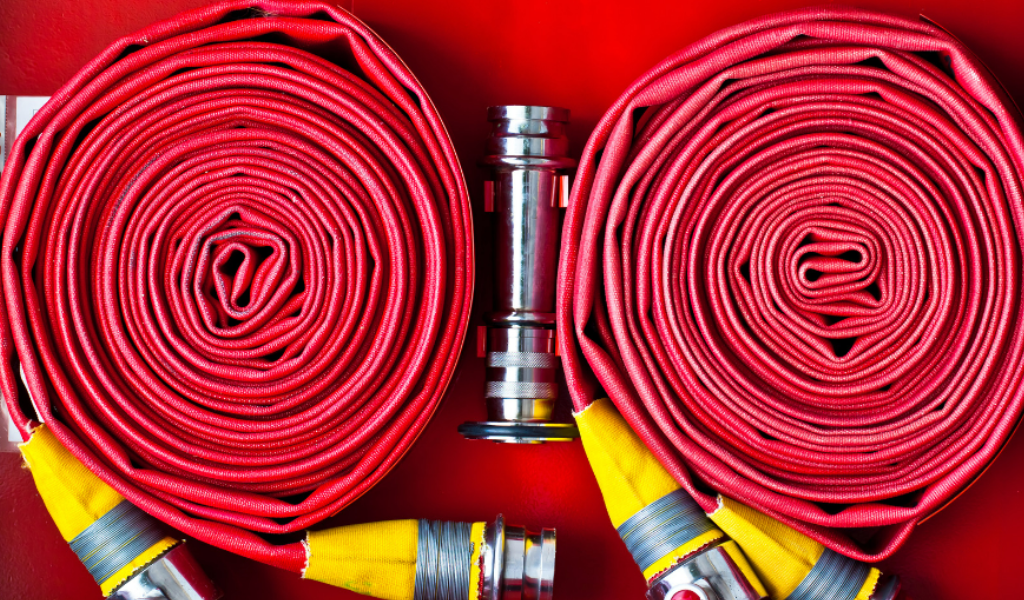
6.Limitations and Challenges of CPVC
Despite its many advantages, CPVC does have certain limitations that must be considered when selecting materials for specific applications. Understanding these constraints ensures appropriate material selection and proper system design.
Temperature and pressure limitations define the operational boundaries for CPVC systems in practical applications. While its heat resistance exceeds PVC, CPVC is still limited to applications below 200°F (93°C), making it unsuitable for steam or other high-temperature processes. Ready for the good part? Pressure ratings decrease as temperature increases, requiring careful system design to ensure safety margins are maintained. At maximum temperature (200°F), pressure ratings may decrease by 50-80% compared to ambient temperature ratings.
UV sensitivity presents challenges for outdoor applications that require additional protection measures. When exposed to sunlight, CPVC can experience photodegradation that compromises its mechanical properties over time. This limitation necessitates protective measures such as painting, wrapping, or installing CPVC components within protective enclosures when used outdoors. The degradation process begins with surface discoloration but can progress to crazing and eventual cracking if left unprotected.
Compatibility issues with certain chemicals and materials require careful planning during system design and installation. CPVC can be damaged by contact with petroleum-based products, including some thread sealants, fire-stop materials, and insecticides. Here’s where most people get it wrong: assuming all plastic-compatible products work with CPVC. Manufacturers provide chemical compatibility guides that should be strictly followed to avoid these issues.
Installation considerations include thermal expansion management, as CPVC expands and contracts with temperature changes more than metals do. CPVC expands approximately 1 inch per 50 feet of pipe per 50°F temperature increase—about three times the expansion rate of copper. Proper support spacing, expansion loops, and offset configurations are essential to accommodate this movement and prevent stress on the system.
Limitation | Impact | Mitigation Strategy |
---|---|---|
Temperature Ceiling | Cannot be used above 200°F (93°C) | Use alternative materials for higher temperature applications |
UV Sensitivity | Degradation with sun exposure | Paint, wrap, or shield from direct sunlight |
Chemical Compatibility | Damage from petroleum products, solvents | Use manufacturer-approved materials, check compatibility charts |
Thermal Expansion | 3x expansion rate of copper | Install proper expansion loops and supports |
Cold Weather Brittleness | Increased risk of impact damage | Handle with care in cold conditions, protect from freezing |
7.Installation Best Practices for CPVC Systems
Successful CPVC installations depend on following established best practices throughout the process, beginning with proper cutting and joining techniques that ensure system integrity. These practices have been refined through decades of field experience and manufacturer research.
Cutting CPVC requires tools that produce clean, square cuts without creating stress points or debris that could compromise joint integrity. Fine-toothed saws, wheel cutters, or pipe shears designed specifically for plastic pipe are recommended for optimal results. You might be wondering about the importance of this seemingly minor step—proper deburring prevents material from being scraped away during assembly, which could otherwise collect and obstruct valves or create flow restrictions.
Joining CPVC components typically involves solvent cement welding, a process that chemically fuses the materials together at the molecular level. This process begins with cleaning the joining surfaces, followed by applying a primer (where required by code) and then the appropriate CPVC solvent cement. But here’s the kicker: the chemical bonding creates a joint that’s stronger than the pipe itself when properly executed, but rushing the process or using incorrect materials can lead to catastrophic joint failures.
Support and hanging requirements differ from metal piping systems due to CPVC’s different physical properties and thermal expansion characteristics. Horizontal CPVC pipes generally require more frequent support than metal pipes of equivalent size—typically every 3-4 feet depending on pipe diameter and temperature. Supports should be designed to accommodate the pipe’s movement during thermal expansion and contraction without causing abrasion.
Expansion and contraction considerations are critical for system longevity in variable temperature applications. CPVC expands approximately 1 inch per 50 feet of pipe per 50°F temperature increase. This movement must be accommodated through proper design, including expansion loops, offsets, or expansion joints in longer runs. Failing to account for thermal movement can result in system damage, particularly near fixed points like equipment connections.
Installation Step | Best Practice | Common Mistake to Avoid |
---|---|---|
Cutting | Use fine-toothed saw or wheel cutter | Using dull tools that create rough edges |
Deburring | Remove all internal and external burrs | Skipping deburring, leaving sharp edges |
Solvent Cementing | Apply cement to both surfaces, assemble while wet | Using too little cement or allowing it to dry before assembly |
Support Spacing | 3-4 feet for horizontal runs (size dependent) | Using metal pipe support spacing standards |
Expansion Accommodation | 1″ per 50′ per 50°F temperature change | Failing to include expansion loops in long runs |
FAQ
Q1: What is the difference between PVC and CPVC?
CPVC (Chlorinated Polyvinyl Chloride) is a thermoplastic produced by chlorination of PVC resin. The additional chlorination gives CPVC enhanced properties including higher heat resistance (up to 200°F/93°C compared to PVC’s 140°F/60°C), improved chemical resistance, and greater strength. This makes CPVC suitable for hot water applications where standard PVC would fail.
Q2: How long does CPVC piping typically last?
When properly installed and maintained, CPVC piping systems can last 50+ years. CPVC doesn’t corrode, scale, or pit like metal pipes and maintains its performance properties throughout its service life. Many manufacturers offer warranties of 25-30 years, but the actual lifespan often exceeds these guarantees when used within specified temperature and pressure ratings.
Q3: Is CPVC safe for drinking water applications?
Yes, CPVC is safe for potable water applications. It’s certified to NSF/ANSI Standard 61 for drinking water system components and doesn’t leach harmful chemicals into water. CPVC doesn’t support bacterial growth and doesn’t affect water taste or odor. Its smooth interior surface prevents biofilm formation and maintains water quality over time.
Q4: Can CPVC be used outdoors or underground?
CPVC can be used underground with proper installation practices, but it’s not recommended for direct outdoor exposure without protection. CPVC is susceptible to UV degradation when exposed to sunlight for extended periods. For outdoor or underground applications, CPVC should be properly insulated, painted with UV-resistant coating, or installed in protective conduit to ensure longevity.
Q5: What chemicals or substances are incompatible with CPVC?
CPVC is incompatible with several substances including: petroleum-based products (oils, greases, fuels), certain solvents (acetone, MEK), some adhesives and caulks containing solvents, ammonia-based products, and chlorinated hydrocarbons. Always consult chemical compatibility charts provided by manufacturers before exposing CPVC to chemicals. Incompatible substances can cause stress cracking, softening, or complete failure of CPVC components.