In today’s demanding industrial and construction environments, selecting materials that maintain their integrity under harsh outdoor conditions is crucial for project success and long-term reliability. Chlorinated Polyvinyl Chloride (CPVC) has emerged as a preferred solution for numerous outdoor applications due to its exceptional chemical resistance, temperature tolerance, and durability. This comprehensive guide explores how CPVC performs in outdoor settings and provides essential knowledge for engineers, contractors, and facility managers seeking reliable materials for their external installations.
1. Understanding CPVC Material Fundamentals
Chlorinated Polyvinyl Chloride (CPVC) represents an evolution of standard PVC technology, created through a post-production chlorination process that fundamentally transforms the material’s performance characteristics. This specialized polymer contains approximately 65-67% chlorine by weight, compared to the 56-57% found in conventional PVC. The additional chlorination creates a more densely packed molecular structure with stronger carbon-chlorine bonds, resulting in superior heat resistance, chemical resistance, and mechanical properties.
The chemical composition of CPVC gives it distinct advantages over standard PVC, particularly in handling higher temperatures. While conventional PVC typically has a maximum service temperature of around 60°C (140°F), CPVC can withstand continuous exposure to temperatures up to 93°C (200°F). This temperature resistance makes CPVC particularly valuable for outdoor applications where solar heat gain and ambient temperature fluctuations are significant factors.
What’s the real story behind CPVC’s growing popularity? The material’s unique combination of properties addresses multiple challenges faced in outdoor installations. Its inherent flame retardancy—with a limiting oxygen index (LOI) typically above 60%—enhances safety in external applications. Additionally, CPVC offers excellent resistance to many chemicals, making it suitable for industrial environments where chemical exposure is a concern. For infrastructure projects requiring long service life with minimal maintenance, CPVC provides an attractive balance of performance and cost-effectiveness that few alternative materials can match.
For outdoor applications specifically, CPVC’s key performance indicators include UV resistance (when properly formulated with stabilizers), impact resistance across varying temperatures, pressure rating stability under thermal cycling, and long-term hydrostatic strength. These properties must be carefully evaluated when selecting CPVC for outdoor use, as they directly impact system longevity and performance reliability.
Property | CPVC | Standard PVC | Significance for Outdoor Use |
---|---|---|---|
Chlorine Content | 65-67% | 56-57% | Higher chlorine content improves UV resistance |
Max Service Temperature | 93°C (200°F) | 60°C (140°F) | Better performance under solar heat exposure |
Chemical Resistance | Excellent | Good | Enhanced durability in polluted environments |
Tensile Strength | 55-60 MPa | 45-55 MPa | Greater structural integrity under wind loads |
Thermal Conductivity | 0.14 W/m·K | 0.16 W/m·K | Reduced heat transfer in temperature extremes |
2. CPVC in Outdoor Environments: Key Challenges
Ultraviolet radiation represents one of the most significant challenges for CPVC in outdoor applications. When exposed to sunlight, unprotected CPVC can experience photodegradation as UV photons break chemical bonds within the polymer chains. This process typically begins with surface yellowing but can progress to more serious degradation, including embrittlement and microcracking, which compromise the material’s structural integrity and performance.
The mechanism of UV degradation in CPVC involves the absorption of UV energy by certain chemical groups within the polymer, creating free radicals that initiate chain reactions. These reactions can lead to chain scission (breaking of polymer chains) and cross-linking, both of which alter the material’s mechanical properties. While CPVC’s higher chlorine content provides some inherent UV resistance compared to standard PVC, unprotected CPVC will still degrade under continuous outdoor exposure.
But here’s the kicker… Temperature fluctuations compound the UV challenge by introducing thermal expansion and contraction stresses. Outdoor CPVC installations can experience significant temperature variations between day and night, summer and winter. These thermal cycles create mechanical stresses at joints, supports, and transitions between materials with different expansion coefficients. Without proper design accommodations, these stresses can lead to joint failures, alignment issues, or even fractures over time. In regions with extreme temperature variations, such as desert environments or areas with severe winters, these thermal effects become particularly critical design considerations.
Moisture exposure presents another critical challenge for outdoor CPVC systems. While CPVC itself is highly resistant to water absorption, moisture can impact system integrity through several mechanisms. Rainwater can carry pollutants that may affect the material surface over time. Freeze-thaw cycles can create mechanical stresses, particularly if water penetrates joints or fittings. In coastal environments, salt spray introduces additional corrosion concerns, while in industrial areas, acid rain may accelerate material aging. System designers must consider these location-specific moisture challenges when specifying CPVC for outdoor applications.
3. CPVC Outdoor Application Scenarios
Outdoor water treatment and distribution systems represent one of the most common applications for CPVC materials. In these settings, CPVC pipes and fittings transport potable water, process water, and chemical solutions while withstanding environmental stressors. Water treatment facilities utilize CPVC for chemical feed lines, filter systems, and storage tank connections where its chemical resistance prevents contamination and ensures consistent water quality. Municipal water distribution networks increasingly incorporate CPVC for service lines and connection points due to its corrosion resistance and long service life.
Chemical processing and industrial facilities leverage CPVC’s exceptional chemical resistance for outdoor piping systems that transport aggressive fluids. These installations often involve exposure to both harsh chemicals and environmental elements, creating demanding service conditions. CPVC excels in applications such as chemical transfer lines, effluent treatment systems, and cooling water circuits where metallic alternatives would rapidly corrode. The material’s ability to maintain its properties across a wide temperature range makes it particularly valuable for outdoor industrial applications in variable climates.
This is where it gets interesting… Building exterior applications have emerged as an innovative use case for CPVC materials. Rainwater management systems, including gutters, downspouts, and collection tanks, benefit from CPVC’s weather resistance and low thermal conductivity. Some architectural applications incorporate CPVC for exterior trim elements, decorative features, and protective coverings where its durability and weather resistance offer advantages over traditional materials. These applications often leverage CPVC’s formability and joining methods to create custom solutions for specific architectural requirements.
Agricultural and irrigation systems represent another significant outdoor application for CPVC. From main distribution lines to field laterals and emitter systems, CPVC provides reliable water delivery in challenging agricultural environments. The material’s resistance to fertilizers, pesticides, and soil chemicals prevents degradation that would affect water quality or system performance. Additionally, CPVC’s smooth interior surface minimizes friction losses and energy consumption while reducing the buildup of mineral deposits that can restrict flow in irrigation systems.
Application Sector | Specific CPVC Uses | Key Performance Requirements |
---|---|---|
Water Treatment | Chemical feed lines, filter systems, storage connections | Chemical resistance, pressure rating, UV stability |
Industrial Facilities | Chemical transfer, effluent systems, cooling circuits | Temperature resistance, chemical compatibility, joint integrity |
Building Exteriors | Rainwater systems, architectural elements, protective covers | Weather resistance, aesthetic stability, dimensional stability |
Agricultural Systems | Irrigation mains, field laterals, chemical injection | Soil chemical resistance, pressure consistency, UV durability |
Marine Environments | Dock utilities, desalination systems, aquaculture | Salt spray resistance, biofouling resistance, impact strength |
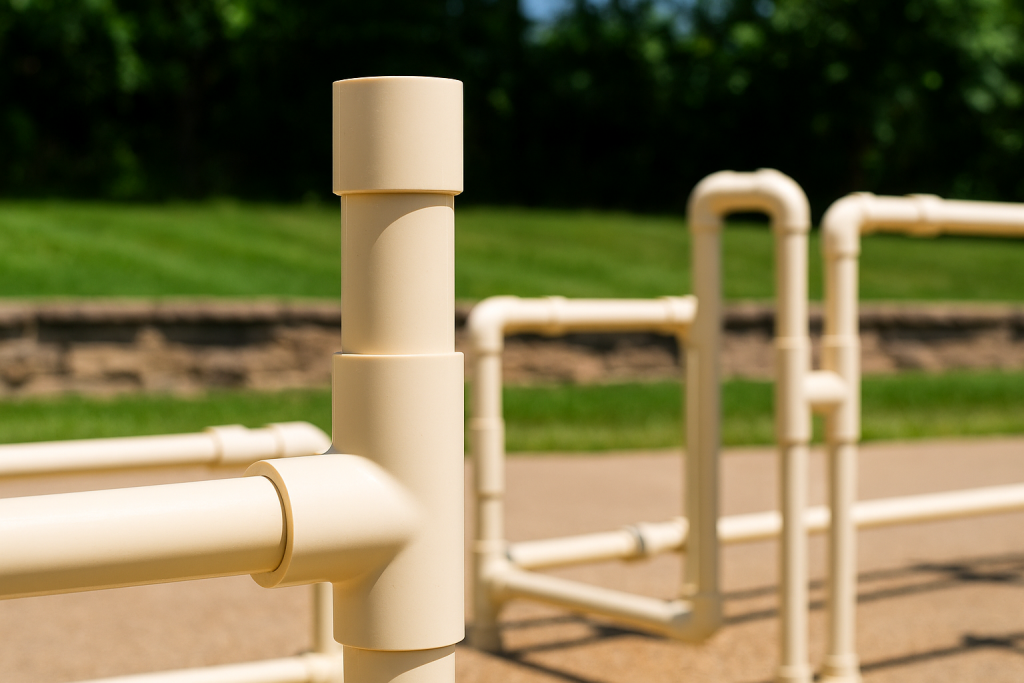
4. Enhancing CPVC Outdoor Durability
UV stabilizers represent the primary defense mechanism for protecting CPVC in outdoor applications. These specialized additives work through several mechanisms to prevent or slow UV degradation. UV absorbers, such as benzotriazoles and benzophenones, function by capturing UV photons and converting their energy into harmless heat before they can damage the polymer structure. These molecules essentially act as sacrificial shields, absorbing harmful radiation that would otherwise impact the CPVC backbone.
Special stabilizer provide another critical protection layer in UV-resistant CPVC formulations. Rather than absorbing UV radiation directly, it interrupt the degradation cycle by neutralizing free radicals formed during initial photodegradation. This mechanism prevents the propagation of chain reactions that would otherwise accelerate material breakdown.
Ready for the good part? Advanced formulation technologies now combine multiple protection mechanisms to create CPVC compounds specifically engineered for outdoor durability. These formulations typically work together to address different aspects of environmental aging. Some cutting-edge formulations incorporate nanomaterials that provide enhanced UV screening without compromising material transparency or mechanical properties. These advanced additives can extend the service life of outdoor CPVC installations by many years compared to standard formulations.
Surface treatments and coatings offer additional protection options for CPVC in particularly challenging environments.Some specialized coatings incorporate reflective pigments that reduce solar heat gain, helping to minimize thermal stresses in the underlying CPVC material. These surface treatments are particularly valuable for applications where appearance is important or where extreme environmental conditions exceed the capabilities of even stabilized CPVC formulations.
Protection Strategy | Mechanism | Effectiveness | Best Applications |
---|---|---|---|
UV Absorbers | Convert UV energy to heat | High initial, decreases over time | Moderate UV exposure areas |
HALS Stabilizers | Neutralize free radicals | Long-lasting, regenerative | High UV intensity regions |
Antioxidants | Prevent oxidative degradation | Moderate, synergistic with others | All outdoor applications |
Reflective Coatings | Reflect UV radiation | Very high while intact | Direct sunlight exposure |
Physical Barriers | Block UV completely | Excellent where applicable | Critical components, joints |
5. Installation Best Practices for Outdoor CPVC
Proper material handling and storage represent the first critical steps in ensuring CPVC outdoor installation success. CPVC products should be stored in covered areas protected from direct sunlight prior to installation. Extended UV exposure during storage can initiate degradation before the system is even installed. Materials should be kept clean and protected from physical damage, as scratches and abrasions can create stress concentration points that accelerate aging. Additionally, proper inventory rotation ensures that materials don’t exceed their recommended shelf life before installation.
Connection methods require special consideration for outdoor CPVC installations. Solvent cement joints remain the most common joining technique, but outdoor applications demand specific attention to temperature and humidity conditions during installation. Solvent welding should be performed within the manufacturer’s recommended temperature range, typically 40°F to 110°F (4°C to 43°C), with adjustments to cure times based on ambient conditions. Some installations benefit from specialized solvent cements formulated with additional UV stabilizers to protect the vulnerable joint areas.
What’s the real story behind successful installations? Support system design often determines the long-term performance of outdoor CPVC systems. Supports must accommodate thermal expansion and contraction while preventing excessive stress on the piping. The coefficient of thermal expansion for CPVC is approximately 3.8 × 10^-5 in/in/°F, significantly higher than metals, requiring careful placement of expansion loops, offsets, or expansion joints in longer runs. Support spacing should follow manufacturer guidelines but generally requires closer spacing for outdoor installations subject to wind loads and temperature fluctuations.
Post-installation inspection and testing protocols should be more rigorous for outdoor CPVC systems than for indoor applications. Pressure testing should be conducted according to applicable codes and standards, with test duration extended to account for the effects of temperature variations. Visual inspection should verify proper alignment, adequate support, and appropriate clearances for thermal movement. Documentation of initial installation conditions provides a valuable baseline for future maintenance inspections and helps identify any premature aging or stress-related issues before they lead to failures.
FAQ Section
Q1: What is CPVC material, and how is it suitable for outdoor applications?
CPVC (Chlorinated Polyvinyl Chloride) is a thermoplastic produced by chlorinating polyvinyl chloride resin, increasing its chlorine content to approximately 67% (compared to PVC’s 57%). This molecular structure change gives CPVC higher heat resistance (up to 93°C/200°F), stronger chemical stability, and better mechanical strength. In outdoor applications, CPVC excels through its excellent corrosion resistance, UV resistance (with proper stabilization), weatherability, and long service life. It’s particularly well-suited for outdoor piping systems, water treatment equipment, and industrial facilities that must withstand temperature fluctuations, chemical exposure, and harsh weather conditions.
Q2: How does CPVC combat UV degradation in outdoor settings?
CPVC combats outdoor UV degradation through three primary mechanisms: First, its inherently higher chlorine content provides partial natural protection by absorbing some UV energy; second, commercial CPVC formulations incorporate specialized UV stabilizers (such as benzotriazole UV absorbers and Hindered Amine Light Stabilizers) that absorb harmful UV radiation and neutralize free radicals formed during photodegradation; third, external protection measures like UV-protective coatings, physical barriers, or installation in shaded locations provide additional defense. These combined strategies allow CPVC to maintain long-term performance stability outdoors, though regular inspection and maintenance remain recommended for optimal performance.
Q3: What is the typical service life of outdoor CPVC systems?
Properly designed, installed, and maintained outdoor CPVC systems typically achieve a service life of 20-50 years, depending on various factors. In moderate climate conditions with adequate UV protection, CPVC systems can approach their theoretical maximum lifespan. Key factors affecting actual service life include: local climate conditions (UV intensity, temperature fluctuations, precipitation); installation quality and stress management; effectiveness of protective measures (coatings, barriers); operating conditions (pressure, temperature, chemical exposure); and maintenance program implementation. Regular inspection and preventive maintenance can significantly extend system life, while ignoring early degradation signs may lead to premature failure.
Q4: What advantages and disadvantages does CPVC have compared to other outdoor piping materials?
CPVC’s main advantages over other outdoor piping materials include: excellent chemical corrosion resistance against many acids, bases, and salts; good temperature tolerance (up to 93°C) exceeding most thermoplastics; lightweight design facilitating installation and reducing support requirements; smooth interior walls minimizing friction losses and deposit accumulation; and relatively low material and installation costs. Primary disadvantages include: higher UV sensitivity than metal materials when untreated; lower impact strength than some engineered plastics, especially at low temperatures; higher thermal expansion coefficient than metals, requiring appropriate expansion compensation design; and potential need for additional protective measures in extreme conditions. Selection should be based on specific application environment, performance requirements, and budget constraints.
Q5: How can long-term reliability be ensured for outdoor CPVC installations?
Ensuring long-term reliability for outdoor CPVC installations requires: selecting high-quality CPVC materials specifically formulated for outdoor use with adequate UV stabilizers and antioxidants; strictly following manufacturer recommendations for storage, handling, and installation to prevent pre-installation material degradation; using appropriate connection methods and materials to ensure fully sealed joints without stress concentration; designing proper support systems that accommodate thermal expansion and contraction while preventing excessive bending or stress; applying professional UV-protective coatings or physical barriers, especially for components directly exposed to sunlight; establishing regular inspection schedules to monitor for color changes, surface chalking, or microcracks indicating early degradation; and maintaining complete installation and maintenance records including material batches, installation dates, and repair history.