Chlorinated polyethene (CPE) is a versatile material frequently employed across various industries. This article explores the fundamental aspects of CPE, including its chemical composition, properties, applications, manufacturing process, advantages, disadvantages, and much more. Understanding CPE is essential for professionals looking to optimize material selection for specific projects, from automotive to construction applications. By examining these factors in detail, this article aims to equip readers with the knowledge needed to make informed decisions about chlorinated polyethene.
1. Introduction to Chlorinated Polyethene
What’s the real story? Chlorinated polyethene is a type of synthetic polymer that is derived from polyethylene through chlorination. This process alters the chemical composition of polyethylene, providing a range of enhanced properties such as chemical resistance, flame retardancy, and improved thermal stability. CPE is widely recognized for its adaptability and is utilized in several vital applications across diverse industries, including construction, automotive, and manufacturing.
As more industries seek materials that can withstand harsh environments, the demand for CPE has increased significantly. Its unique combination of strength, flexibility, and resistance to degradation makes it a material of choice for various applications . For instance, CPE is routinely used in roofing membranes, pipe coatings, and automotive components due to its durability and performance advantages.
The aim of this section is to give a comprehensive overview of what chlorinated polyethene is, its importance in contemporary material science, and the context within which it operates in the marketplace. By the end of this section, readers will gain foundational knowledge, setting the stage for deeper exploration into the properties and applications of CPE.
Feature | Description |
---|---|
Chemical Structure | Derived from polyethylene through chlorination |
Enhancements | Increased durability and resistance properties |
Common Uses | Roofing, automotive parts, and piping systems |
2. The Chemical Composition of Chlorinated Polyethene
Let’s dive deeper into the chemical details that make chlorinated polyethene special. CPE is essentially created by modifying polyethylene, a widely used plastic known for its versatility and chemical resistance. The chlorination process involves exposing polyethylene to chlorine gas, resulting in a series of chlorination reactions that substitute hydrogen atoms with chlorine atoms. This modification significantly enhances the polymer’s properties.
What does this mean for users? The introduction of chlorine atoms in the polymer backbone not only increases the material’s chemical resistance but also aids in achieving flame retardancy. CPE typically contains a chlorine content ranging from 25% to 45%, depending on the intended application. This range allows manufacturers to tailor the polymer’s properties based on specific needs.
Moreover, CPE displays excellent thermal stability, withstanding temperatures ranging from -40°F to 150°F. This characteristic makes it an ideal choice for environments with extreme temperature fluctuations. In construction, for example, CPE’s chemical inertness proves beneficial for applications that involve exposure to oils, solvents, and other harsh substances.
To put this in perspective, the chlorination process fundamentally alters the molecular structure of polyethylene, maximizing its effectiveness in various applications. Understanding the chemical composition of chlorinated polyethene provides crucial insights that can drive informed material selection in various manufacturing scenarios.
Parameter | CPE Range |
---|---|
Chlorine Content | 25% to 45% |
Thermal Stability | -40°F to 150°F |
Chemical Resistance | High across oils and solvents |
3. Key Properties of Chlorinated Polyethene
Now, let’s explore the distinctive properties of chlorinated polyethene that make it stand out. CPE exhibits a unique combination of mechanical, thermal, and chemical properties, which contribute to its versatility in applications as discussed in‘’Chlorinated Polyethylene – Properties, Uses & Structure”. But here’s the kicker: these properties make CPE an excellent alternative to other materials like PVC and traditional polyethylene.
One of the standout features of CPE is its flexibility. Despite its robust chemistry, CPE remains pliable, allowing it to be easily molded and shaped into various forms. This flexibility makes it practical for applications ranging from automotive components to flexible piping systems. Moreover, CPE also exhibits remarkable tensile strength, enabling it to maintain structural integrity under stress without compromising elasticity.
Another factor to consider is CPE’s outstanding weather resistance. This property makes it suitable for outdoor applications, where exposure to ultraviolet radiation and other environmental factors can degrade less durable materials. CPE can withstand prolonged sunlight without losing its mechanical properties, making it ideal for roofing membranes and other exterior applications.
Additionally, CPE’s flame-retardant properties make it a preferred option in industries where fire safety is paramount. It can help to mitigate material flammability, providing a better safety profile for consumers. Overall, these advantageous properties position chlorinated polyethene as a leading choice for a wide range of applications across various sectors.
Property | Description |
---|---|
Flexibility | Offers high adaptability in applications |
Weather Resistance | Durable under UV exposure |
Flame Retardancy | Reduces flammability risks |
4. Applications of Chlorinated Polyethene
What’s the real opportunity here? Chlorinated polyethene has found utility in several critical applications across different industries. This is where it gets interesting… The versatility of CPE allows it to function effectively in varied environments, from construction to automotive and beyond.You can find more real-world examples in”What Is Chlorinated Polyethylene Used For?”
In construction, CPE is commonly used as a waterproofing material. Its durability and chemical resistance make it ideal for roofing systems that must endure harsh weather conditions, including rain, wind, and UV radiation. Large-scale projects often rely on CPE membranes to protect buildings and ensure their integrity over time.
Another significant application of chlorinated polyethene is in electrical cable jacketing. CPE’s flexibility, combined with its flame-retardant properties, offers excellent protection for electrical components in diverse environments. This application is particularly crucial in areas like automotive manufacturing, where cables must withstand challenging conditions.
Additionally, CPE is often utilized in the production of automotive parts, where its chemical and thermal stability are critical. For instance, CPE is commonly employed for seals, gaskets, and hoses due to its ability to resist degradation when exposed to fluids, heat, and various chemicals.
Overall, the application of chlorinated polyethene in different sectors showcases its adaptability and effectiveness, ultimately cementing its significance in current manufacturing practices.
Industry | Application | Benefits |
---|---|---|
Construction | Waterproofing membranes | Resilient against weather and UV damage |
Automotive | Electrical cable jacketing | Flexibility and flame resistance |
Manufacturing | Seals and gaskets in machinery | Chemical and thermal durability |
5. Manufacturing Process of Chlorinated Polyethene
Let’s take a closer look at how chlorinated polyethene is made. Understanding the manufacturing process provides essential insights into the quality and performance of the final product. It all begins with the chlorination of polyethylene; the method of chlorination used can significantly affect the properties of the resulting CPE.
Essentially, the chlorination of polyethylene can be accomplished through two main methods: gas-phase chlorination and solution-phase chlorination. In gas-phase chlorination, polyethylene is exposed to chlorine gas at high temperatures, allowing the chlorine to penetrate the polymer chains. On the other hand, solution-phase chlorination involves dissolving polyethylene in a solvent and saturating it with chlorine gas, which provides more controlled chlorination.
In both scenarios, it’s crucial that manufacturers adhere to strict safety measures. Chlorination can produce hazardous byproducts, so rigorous monitoring and filtration systems must be in place. Quality control is also vital throughout the manufacturing process to ensure that the resulting chlorinated polyethene meets industry standards and customer specifications.
Finally, CPE is often subjected to additional processing steps, such as blending with additives to improve performance characteristics or coloring agents for aesthetic purposes. This multifaceted manufacturing process enables the production of tailored CPE formulations that can meet specific application needs.
Method | Description | Applications |
---|---|---|
Gas-phase Chlorination | Exposes polyethylene to chlorine gas | Used for rapid production |
Solution-phase Chlorination | Involves dissolving polyethylene in solvent | Allows for controlled chlorination |
Quality Control | Monitoring during production | Ensures compliance with industry standards |
6. Advantages of Chlorinated Polyethene
What makes chlorinated polyethene a preferred choice among manufacturers? The advantages of CPE are numerous and significant. First and foremost, its improved usability and performance make it stand out in various applications. CPE exhibits high chemical resistance, which protects it from degradation in environments where standard polyethylene might fail.
In the automotive sector, for instance, CPE’s resilience against fuels and oils enhances the lifespan of components such as seals and gaskets. This durability translates into reduced maintenance costs over time, as replacements and repairs are less frequent compared to traditional materials.
Another major advantage is its excellent thermal properties. Withstanding a broader range of temperatures compared to other polymers allows CPE to thrive in diverse environments. This feature is particularly critical in construction and electrical applications where material failure due to changing temperatures could have dire consequences.
Additionally, the flame-retardant properties of CPE add an essential layer of safety, which is increasingly important across various industries. As regulatory demands for fire safety increase, CPE provides a solution that meets the necessary standards while maintaining performance attributes.
Overall, the advantages of chlorinated polyethene position it as a leading material in industrial applications, making it an excellent investment for manufacturers looking to enhance product quality and reliability.
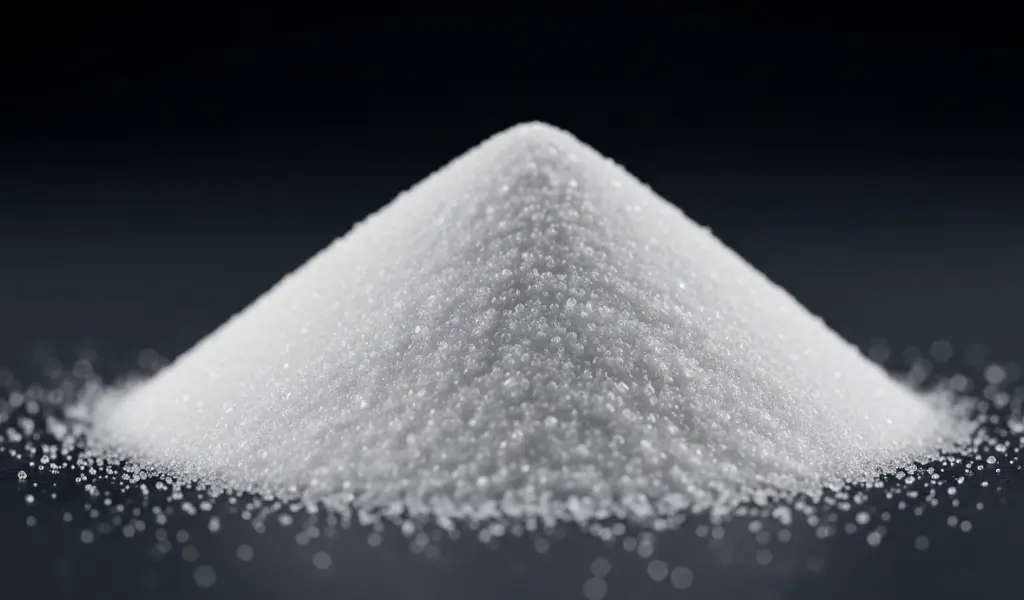
Advantage | Benefit | Impact |
---|---|---|
Chemical Resistance | Protects against degradation | Reduces replacement costs |
Thermal Stability | Endures temperature variations | Enhances performance in varied environments |
Flame Retardant Properties | Improves safety in applications | Meets regulatory safety standards |
7. Disadvantages and Limitations of Chlorinated Polyethene
While chlorinated polyethene offers a wealth of benefits, it is also important to acknowledge its limitations. But here’s the kicker: understanding these drawbacks is critical for making informed decisions. One of the primary concerns is processing challenges. CPE can be more difficult to work with than standard polyethylene due to its increased viscosity during manufacturing.
This characteristic can lead to complications in various fabrication processes, such as molding and extrusion. Manufacturers must invest in specialized equipment or adjust their processes to accommodate CPE, which can increase production costs.
Another limitation is related to environmental concerns. While CPE is more durable, the chlorination process can involve hazardous materials and byproducts, which necessitate careful management and disposal. As regulatory scrutiny surrounding chemical processes continues to tighten, companies must be proactive in adhering to environmental standards, which can pose challenges.
Lastly, CPE’s performance may diminish under extreme conditions, particularly at temperatures exceeding its recommended limits or in the presence of certain solvents. Although it generally performs better than traditional polyethylene, understanding these boundaries ensures effective application and material selection.
In summary, while chlorinated polyethene boasts several advantages, it is essential to weigh these against its limitations to ensure that the material meets the specific demands of each application.
Limitation | Description | Considerations |
---|---|---|
Processing Challenges | Increased viscosity can complicate manufacturing | May require specialized equipment |
Environmental Concerns | Chlorination process can produce hazardous byproducts | Necessitates compliance with regulations |
Performance Limitations | May fail under extreme conditions | Understanding boundaries is crucial |
8. Where to Use Chlorinated Polyethene
So, where is chlorinated polyethene most effectively utilized? The specific applications of CPE highlight its adaptability and extensive utility across numerous industries. Chlorinated polyethene frequently finds use in the construction sector, particularly in waterproofing and roofing applications. Its durability, alongside chemical resistance, ensures long-lasting performance even in harsh conditions.
In the automotive industry, CPE is often employed in critical components like hoses, gaskets, and seals, where its elasticity and resistance to chemicals are invaluable. The automotive sector has recognized the value of CPE, especially in areas subjected to continuous movement or exposure to fluids.
Furthermore, CPE has become a mainstay in electrical cable insulation. Its flame-retardant properties make it an exceptional choice for applications requiring high safety standards. By ensuring the protection of electrical components, CPE enhances safety and operational efficiency in electrical systems.
Additionally, CPE finds applications in the manufacturing of consumer goods, particularly in products that require resilience and reliability under environmental stress. Examples include protective covers or flexible tubing in various industrial contexts.
Overall, the versatility of chlorinated polyethene lends itself to a myriad of applications, demonstrating its robust performance and adaptability.
Sector | Application | Key Characteristics |
---|---|---|
Construction | Waterproofing in roofs | Durable and weather-resistant |
Automotive | Hoses, gaskets, and seals | Chemical resistant and flexible |
Electrical | Cable insulation | Flame-retardant properties |
9. Regulatory Compliance for Chlorinated Polyethene
Navigating regulatory compliance can be complex, especially for chemicals like chlorinated polyethene. But here’s the kicker: understanding these regulations is crucial for manufacturers and users alike. CPE must adhere to various safety and environmental standards, which vary from region to region.
The regulatory landscape often focuses on the safety of materials used in construction, automotive, and electrical applications. In the U.S., for instance, the Environmental Protection Agency (EPA) monitors the use of chlorine in manufacturing, enforcing regulations that limit toxic byproducts and environmental impact.
Furthermore, CPE used in building products must meet guidelines set by organizations like the American Society for Testing and Materials (ASTM) and Underwriters Laboratories (UL). Adherence to these standards assures consumers that products meet required safety levels, thus enhancing market acceptance.
Internationally, regulatory compliance can vary significantly. In Europe, for example, manufacturers must comply with the REACH regulation, which governs chemical registration, evaluation, authorization, and restriction to ensure chemical safety.
To achieve compliance, companies often need to perform thorough assessments of their materials, documentation, and reporting. Striving for compliance not only supports consumer safety but also fortifies a company’s reputation in the marketplace.
Regulation | Jurisdiction | Key Focus Area |
---|---|---|
EPA Guidelines | United States | Environmental impact and safety |
ASTM Standards | Various | Material testing and performance |
REACH Regulation | European Union | Chemical safety and consumer protection |
10. Future Trends in Chlorinated Polyethene
What lies ahead for chlorinated polyethene in the evolving marketplace? The future of CPE is promising, bolstered by several emerging trends and innovations that suggest continued growth and adaptation. With the material science sector pushing for sustainability, CPE is expected to undergo further development to improve its environmental footprint.
One significant trend is the growing emphasis on bio-based alternatives. Manufacturers are exploring methods to produce CPE using renewable resources, which could reshape its production landscape. As consumers become increasingly environmentally conscious, such initiatives may lead to a more sustainable industry while retaining the advantageous properties of traditional CPE.
Additionally, technological advancements in production techniques, including improved chlorination methods and enhanced processing capabilities, will allow for more efficient manufacturing. These innovations can enhance the quality of CPE while reducing production costs, which is beneficial for manufacturers and consumers alike.
Furthermore, the application of smart material technology is another exciting frontier. Incorporating sensors or responsive features into CPE could lead to its use in innovative applications that require dynamic performance. This capability would significantly expand the material’s versatility and functionality.
Overall, the future of chlorinated polyethene is set for growth, driven by sustainability initiatives, advancements in technology, and expanding applications that cater to modern needs.
Trend | Description | Potential Impact |
---|---|---|
Bio-based Alternatives | Development of renewable resource-based CPE | More sustainable products |
Technological Advancements | Improved methods for production | Increased efficiency and lower costs |
Smart Material Technology | Integration of responsive features | Expanded functionalities and applications |
11. Comparing Chlorinated Polyethene to Other Materials
Now, let’s compare chlorinated polyethene with alternative materials to highlight its strengths and weaknesses. What are the essential differences? When juxtaposing CPE with materials like PVC and traditional polyethylene, several notable distinctions emerge.
First, the chemical resistance of chlorinated polyethene often surpasses that of PVC. This characteristic allows CPE to remain functional in applications with aggressive substances, such as acids and solvents.For a closer comparison, see”How Chlorinated Polyethene Compares to PVC?” As such, CPE becomes a more favorable choice in industries where long-term stability against chemical exposure is critical.
In terms of flexibility, CPE generally maintains a superior level compared to traditional polyethylene and some variations of PVC. The enhanced elasticity of CPE enables it to perform well in applications requiring bending or stretching, making it preferable in dynamic environments.
However, while CPE offers many advantages, it can be more expensive to produce and process when compared to PVC. This potential cost disadvantage may lead manufacturers to select PVC for applications where high chemical resistance is not paramount.
In summary, chlorinated polyethene presents unique advantages reclaiming market share across several sectors while still facing competition from other widely used materials.
Material | Chemical Resistance | Flexibility | Cost |
---|---|---|---|
Chlorinated Polyethene (CPE) | High | Superior | Higher production costs |
PVC | Moderate | Limited | More cost-effective |
Polyethylene | Low | Good but not as robust | Generally lowest production costs |
12. Chlorinated Polyethene and Environmental Impact
As the conversation around sustainability grows, evaluating the environmental impact of chlorinated polyethene becomes increasingly important. What’s the takeaway? Chlorinated polyethene’s production and disposal processes can raise concerns regarding environmental sustainability, but proactive efforts are being made to address these issues.
The chlorination process inherently involves chemicals that can produce hazardous byproducts, which necessitates careful management and adherence to safety regulations. This concern highlights the importance of responsible manufacturing practices to minimize ecological footprints.
Moreover, the recyclability of CPE is a critical consideration. Unlike some plastics that can be easily processed and recycled, CPE can face challenges in recycling due to its chemical composition. However, advancements in recycling technologies and methodologies are emerging, showing promise in allowing CPE recycling in the future.
Additionally, the development of bio-based alternatives to CPE could significantly reduce its environmental impact. By focusing on sustainable sourcing, manufacturers can create greener options without sacrificing performance.
In conclusion, while chlorinated polyethene presents some environmental concerns, ongoing advancements and efforts towards sustainability can reshape its lifecycle and usage for a more positive outcome.
Environmental Concern | Issue | Solution |
---|---|---|
Hazardous Byproducts | Chemicals produced during chlorination | Implement strict safety measures |
Recycling Challenges | Difficulty in processing CPE for recycling | Invest in new recycling technologies |
Bio-based Alternatives | Limited sustainable options | Research and develop eco-friendly versions |
13. User Experiences with Chlorinated Polyethene
Let’s gather insights from users dealing with chlorinated polyethene. Anecdotal experiences can provide valuable lessons about its effectiveness and challenges. What do the users say? Professionals in various industries often report high satisfaction levels when using CPE, particularly in construction and automotive applications.
In the construction industry, many contractors have praised CPE’s performance in roofing applications. Users appreciate the effectiveness of CPE membranes in providing long-lasting waterproofing, noting that they withstand harsh weather conditions without significant degradation. Users have reported that the durability of CPE often translates into reduced maintenance costs and fewer replacements over time.
Similarly, automotive professionals often highlight the material’s resilience in automotive parts. Mechanics have noted that replacement parts made from CPE consistently outperform those made from traditional materials, particularly in parts exposed to fluids and heat. This feedback indicates that CPE shapes up as an excellent investment for manufacturers.
However, some users also note that sourcing high-quality CPE can pose challenges. Inconsistent quality among different suppliers can lead to variable performance in applications. Industry professionals recommend diligently vetting suppliers and prioritizing established brands known for reliable material quality.
Overall, user experiences with chlorinated polyethene suggest it is a strong contender within its field, providing reliable performance but requiring attention to sourcing.
User Type | Feedback | Recommendations |
---|---|---|
Contractors | Highly satisfied with CPE in construction | Focus on sourcing from reputable suppliers |
Automotive Professionals | Positive feedback on performance | Invest in quality materials |
End-users | Mixed quality experiences | Verify supplier credibility |
14. Common Mistakes in Material Selection
What errors should professionals avoid when selecting materials like chlorinated polyethene? Understanding common pitfalls is essential for effective material selection. One frequent mistake is prioritizing cost over performance. While chlorinated polyethene may come at a higher initial investment, its longevity and reliability can lead to significant long-term savings. Companies should weigh the total cost of ownership instead of focusing solely on upfront expenditures.
Another common error is failing to assess compatibility with specific applications. Not all formulations of CPE are suitable for every application. Users must thoroughly investigate the chemical and physical requirements of their projects to ensure they select the appropriate material grade for their needs.
Moreover, overlooking environmental concerns can lead to compliance issues. As regulations become stricter, manufacturers must prioritize materials that comply with environmental standards to avoid delays and potential fines. Researching the material’s manufacturing process and lifecycle will help in making compliant choices.
Finally, users may assume that all CPEs perform equally. There are significant variations in quality and performance among different suppliers. Conducting proper evaluations and considering testimonials will guide buyers toward reliable material.
In summary, avoiding these common mistakes can lead to better material selection, ensuring project success and satisfaction.
Mistake | Consequence | Solution |
---|---|---|
Prioritizing Cost | Long-term expenses may increase | Evaluate total cost of ownership |
Incompatibility | Material failures in applications | Conduct thorough assessments |
Ignoring Compliance | Potential legal and financial repercussions | Research and adhere to regulations |
Assuming Uniform Quality | Variable performance between suppliers | Vet suppliers and review testimonials |
15. Conclusion and Key Takeaways
In conclusion, chlorinated polyethene stands as an essential material within various industries thanks to its unique properties and diverse applications. Through our exploration of CPE, we’ve established its capabilities, including chemical resistance, flexibility, and thermal stability.
As industries continue to evolve, the material’s adaptability and performance will make it a primary choice in challenging environments. However, navigating the nuances of production and applications requires understanding the drawbacks and potential issues, especially concerning environmental implications.
For professionals seeking to optimize material selections, chlorinated polyethene offers a comprehensive set of benefits, provided proper attention is given to sourcing and compliance. Overall, employing CPE strategically can lead to enhanced product quality and operational efficiency across many sectors.
FAQ Section
Q1: What is chlorinated polyethene?
Chlorinated polyethene is a synthetic polymer created by chlorinating polyethylene, enhancing its properties like chemical resistance and flexibility, making it suitable for various applications.
Q2: How does the chlorination process work?
The chlorination process modifies polyethylene by replacing hydrogen atoms with chlorine atoms, significantly improving the polymer’s durability and chemical properties.
Q3: Where is chlorinated polyethene commonly used?
Chlorinated polyethene is utilized in roofing, automotive components, electrical insulation, and other industrial applications that require flexibility and chemical resistance.
Q4: What are the environmental concerns associated with chlorinated polyethene?
Environmental concerns include the production of hazardous byproducts during chlorination and challenges related to the recycling of CPE materials which necessitate careful management.
Q5: What common mistakes should be avoided when selecting chlorinated polyethene?
Common mistakes include prioritizing cost over performance, failing to assess compatibility with specific applications, overlooking environmental compliance, and assuming uniform quality across different suppliers.