1. What is CSM Rubber, also known as Hypalon Rubber?
CSM rubber, or chlorosulfonated polyethylene, is a synthetic rubber that was once marketed under the brand name Hypalon. It’s not a trendy polymer, and you probably won’t find it on a supermarket shelf—but in industrial and construction applications, it’s a material that just won’t quit. CSM stands for performance, especially in places where durability under fire, UV, ozone, and harsh chemicals matters.
But here’s the kicker… Even though DuPont discontinued Hypalon in 2010, the material didn’t vanish. It lives on through other global manufacturers producing the same chemical structure under different brand names. At its core, CSM is polyethylene that has been chemically modified with chlorine and sulfonic acid groups. This transformation gives it remarkable resistance to aging, UV, and ozone—traits not easily found in other elastomers.
What sets it apart? It combines the strength of thermoplastics with the flexibility of rubber. The polar groups introduced during chlorosulfonation allow cross-linking, which means the rubber doesn’t just stretch—it stretches and bounces back again and again without breaking down. Whether it’s coating cable insulation, sealing rooftop membranes, or withstanding chemical splash in a factory, CSM thrives where others break.
Let’s make this clear with some comparisons:
Property | CSM (Hypalon) | EPDM | CR (Neoprene) |
---|---|---|---|
UV/Ozone Resistance | Excellent | Very Good | Good |
Oil Resistance | Moderate | Poor | Good |
Weather Durability | Excellent | Very Good | Moderate |
Heat Resistance | Up to 150°C | Up to 120°C | Up to 130°C |
Chemical Resistance | High | Moderate | Moderate |
Ready for the good part? CSM isn’t just tough—it’s chemically designed to be consistent. That means fewer surprises during production, longer service life, and lower maintenance costs. In critical applications, you’re not buying rubber—you’re buying reliability.
2. Why Was Hypalon Discontinued by DuPont?
When DuPont pulled the plug on Hypalon in 2010, many in the industry were left scrambling. It wasn’t about product failure, nor was there a sudden decline in demand. Instead, it was a calculated internal strategy shift paired with environmental regulation pressures that made continued production in the U.S. less attractive for DuPont.
Here’s what most people missed. Hypalon production was resource-intensive. The process used solvents and chlorinated chemicals, which, under tightening EPA and global standards, became harder to justify economically. Rather than investing in greener tech or moving overseas, DuPont chose to retire the brand. That decision left a vacuum in several industries—particularly roofing, automotive sealing, and wire insulation—where Hypalon had been a preferred material for decades.
So, what happened next?
Other manufacturers around the world stepped up. Companies in China, Japan, and parts of Europe began offering CSM compounds under different trade names. These were chemically identical to Hypalon but without the branding. The global supply never truly disappeared—it just decentralized.
What’s the real story? Hypalon’s end at DuPont didn’t signal the death of CSM. It only shifted production to other suppliers better positioned to manage cost, regulation, and volume.
Reason for Discontinuation | Explanation |
---|---|
Environmental Pressure | Solvent-heavy process under regulation scrutiny |
Strategic Exit | DuPont realigned business focus |
Operational Costs | High investment needed for modern compliance |
Market Alternatives | Rise of EPDM, TPO, and newer elastomers |
CSM lives on—strong, stable, and still available from multiple reputable producers. If your supplier says “Hypalon is no more,” they’re not wrong. But if they say “CSM is no more,” you might want to shop around.
3. Who Still Produces CSM Today?
Now let’s set the record straight. Hypalon was just a brand. CSM as a material never left the market. Today, several global manufacturers produce chlorosulfonated polyethylene rubber to the same or better specs than DuPont ever did. So, who’s behind the curtain now?
You might be surprised by the answer. China leads the pack, with several medium-to-large factories supplying industrial-grade CSM to export markets. Japan still maintains limited but high-quality production, while European chemical firms manufacture niche-grade CSM for advanced applications. The key difference now is branding. Instead of seeing “Hypalon,” you’ll see codes like D4035, D6035, or product names you’ve never heard before—yet they offer the same performance.
It’s not just about availability. It’s about who you trust to deliver consistent quality. Not all CSM is created equal. Some suppliers stretch the definition, mixing in fillers or skipping stabilization additives to cut cost. Others offer tight QC systems, batch traceability, and REACH-compliant production. If you’re sourcing from Asia, always ask for a COA, test sheet, and application sample.
So which producers matter?
Region | Notable Producers | Quality Focus |
---|---|---|
China | DXD Group | Export-grade |
Japan | Tosoh Corporation | Specialty grades |
Europe | Lanxess (limited) | High-purity compounds |
India | Local compounders | Moderate consistency |
But here’s the catch… Many end users think Hypalon is extinct and switch to EPDM or TPO, losing out on performance. The smart buyers? They work directly with specialized manufacturers who’ve mastered the same chemistry and maintained the same quality—all without the DuPont logo.
4. What Are the Key Properties of CSM Rubber?
Let’s get into the heart of why CSM rubber is still a go-to choice for so many industrial buyers. At first glance, it looks like any other black rubber. But don’t be fooled. CSM is a chemical powerhouse wrapped in a flexible shell. Its molecular structure gives it a set of physical and chemical properties that outperform many general-purpose rubbers—especially when you throw in ozone, UV, oil, acid, and aging stress.
This is where it gets interesting… The chlorosulfonation process transforms basic polyethylene into something extraordinary. Chlorine and sulfonic acid groups anchor onto the polymer backbone. These groups create polarity, which in rubber chemistry means tighter cross-linking, stronger bonds, and higher resistance to degradation.
Let’s break down the properties that make CSM a material of choice in extreme conditions:
- UV and Ozone Resistance: CSM shrugs off sunlight and atmospheric ozone like it’s nothing. This makes it perfect for rooftop applications and outdoor equipment.
- Chemical Resistance: It stands up to acids, bases, and oxidizing agents better than EPDM or CR. In environments where chemical splash is routine, CSM holds its shape and performance.
- Heat Aging Resistance: CSM keeps its integrity at elevated temperatures—typically up to 150°C. It resists hardening or cracking under prolonged thermal exposure.
- Abrasion and Impact Resistance: While not as tough as NBR in oil applications, CSM still offers decent mechanical strength, especially when reinforced.
- Water Resistance: CSM resists hydrolysis and doesn’t swell or break down in moist environments.
Here’s a side-by-side summary of these strengths:
Property | CSM (Hypalon) | EPDM | CR (Neoprene) |
---|---|---|---|
UV Resistance | Excellent | Very Good | Good |
Ozone Resistance | Excellent | Very Good | Good |
Acid/Alkali Resistance | Excellent | Moderate | Moderate |
Oil Resistance | Moderate | Poor | Good |
Temperature Limit (°C) | 150 | 120 | 130 |
Flame Retardancy | High | Low | Medium |
But here’s the kicker… CSM not only survives these stressors—it does so for decades. In roofing, for instance, CSPE membranes have demonstrated 30+ year lifespans with minimal cracking or peeling. In wire insulation, it helps keep cabling systems safe in mines, ships, and outdoor facilities without needing frequent replacement.
While it’s not the cheapest elastomer on the market, CSM pays off in reduced maintenance, fewer failures, and extended product life. That’s why engineers specify it when performance trumps price.
5. How Does CSM Compare with Other Rubbers Like EPDM and CR?
On paper, CSM seems like an overachiever. But how does it actually compare when you put it side by side with other popular rubbers like EPDM or neoprene (CR)? These materials often compete in similar applications—especially roofing, automotive, marine, and insulation. Each has its own strengths, but CSM consistently proves why it’s the material of choice when conditions get rough.
But here’s the kicker… It’s not just about one property—like UV resistance or chemical durability. It’s about balance. CSM doesn’t just win in one category. It holds its own across a wide range of performance metrics, giving engineers and procurement teams a multi-functional material with fewer compromises.
Let’s start with EPDM, a synthetic rubber widely used for seals and weatherstrips. EPDM is cheaper and more flexible at low temperatures, but it can’t handle oils or oxidizing chemicals. Its flame resistance is poor, and it degrades faster when exposed to industrial fumes or acid rain.
Now look at CR (neoprene). It’s oil-resistant and has decent mechanical strength, but it struggles with long-term UV or ozone exposure. CR also tends to harden over time when left outside—making it less ideal for long-service outdoor use.
In contrast, CSM combines UV durability, acid resistance, and moderate oil resistance, giving it an edge in mixed-environment conditions like marine cable sheathing, industrial gaskets, and heavy-duty roofing. It won’t win on price. But it delivers consistency, lifespan, and reduced replacement cycles.
Here’s a quick performance breakdown:
Feature | CSM (Hypalon) | EPDM | CR (Neoprene) |
---|---|---|---|
Weather Resistance | Excellent | Very Good | Moderate |
Chemical Resistance | High | Moderate | Moderate |
Oil Resistance | Moderate | Poor | High |
Cost | High | Low | Moderate |
Lifespan (outdoor) | 20–30 years | 10–15 years | 5–10 years |
Here’s the real story. While EPDM may win for cost-sensitive weatherstripping, and CR might be ideal for oil-contact applications, CSM dominates where you need multiple resistances in one formulation. It’s the all-rounder that keeps your product running—whether it’s on a rooftop, in a corrosive lab, or under the hood of a truck.
If your application involves sunlight, acid, heat, and the occasional splash of oil, picking CSM over the others could mean the difference between a 10-year headache and a 30-year solution.
6. What Are the Most Common Applications of CSM?
If you’ve made it this far, you’re probably thinking, “So where does this rubber actually go?” The answer? Almost everywhere—if durability, chemical resistance, and outdoor exposure are part of the job description. CSM is not just a technical spec on a datasheet. It’s the backbone material in some of the most demanding industries on earth.
Ready for the good part? From electrical infrastructure to watercraft, from heavy machinery to building rooftops, CSM rubber shows up where standard rubbers would wear out, shrink, crack, or delaminate. Here are a few examples to prove the point:
- Cable Sheathing & Insulation: Mines, tunnels, oil rigs—these are not cable-friendly environments. CSM resists oil, UV, and fire, making it ideal for jacketing critical electrical systems.
- Roofing Membranes: CSPE roofing membranes made from CSM have a proven 30-year lifespan in commercial construction. They withstand UV, acid rain, and thermal cycling better than TPO or EPDM.
- Automotive Hoses & Seals: Under-the-hood environments demand resistance to engine heat, fuel splashes, and air pollution. CSM offers a solid mix of chemical and weather resistance, especially in air intake and coolant hoses.
- Industrial Linings & Coatings: Tanks, ducts, and pipes that carry corrosive fluids often use CSM rubber linings due to their chemical resistance and mechanical toughness.
- Marine Uses: Boats and marine infrastructure are always exposed to UV, salt, and ozone. CSM offers the ideal resilience for sealing strips, inflatable boats, and cable jackets in marine-grade performance.
Let’s break these out visually:
Application Sector | CSM Use Case | Reason for Selection |
---|---|---|
Power & Utilities | Cable insulation and sheathing | UV, fire, and chemical resistance |
Construction | Roofing membranes | Long service life, acid rain-proof |
Automotive | Air intake hoses, sealing gaskets | Heat, ozone, and chemical defense |
Chemical Plants | Tank and pipe linings | Acid/alkali protection |
Marine & Boating | Dinghies, cable jackets, seals | Salt water, UV, and aging resistance |
What’s the real story? When clients ask what CSM is “best used for,” the answer is: wherever failure isn’t an option. It’s the material you use when downtime costs money and rework isn’t acceptable.
7. Why Is CSM Ideal for Harsh Outdoor Use?
Not all rubbers are created to face the wrath of the outdoors. Some dry out. Others swell. Many crack under long-term exposure to sun, ozone, acid rain, or industrial exhaust. But CSM—thanks to its chlorosulfonated structure—is built to last in exactly those environments.
But here’s the kicker… It’s not just “resistant” in a lab sense. CSM thrives in 10, 20, even 30-year deployment cycles where other materials disintegrate. Its molecular backbone stays stable under repeated UV exposure, and its cross-linked surface resists oxidation.
Let’s explore why this matters:
- UV Exposure: CSM rubber holds its elasticity even after years in direct sun. It doesn’t fade, crack, or embrittle.
- Ozone Resistance: Many polymers are attacked by atmospheric ozone. CSM is one of the few that is chemically resistant to it, even without antioxidants.
- Acid Rain & Pollution: Roofing and automotive components that get hit with acid rain or smog stay intact longer when made with CSM.
- Temperature Fluctuations: From −30°C to 150°C, CSM remains flexible. It doesn’t shrink excessively or become brittle in cold or hot shifts.
Let’s see the real-world contrast:
Outdoor Stress Factor | CSM Performance | Typical EPDM/CR Performance |
---|---|---|
UV Exposure | No surface cracking | Discoloration, chalking |
Ozone Resistance | Maintains elasticity | Microcracks over time |
Acid Rain Resistance | No swelling or etching | Material degradation |
Freeze/Thaw Cycles | Stable dimensions | Shrinkage or cracking |
So here’s what to consider. If your product needs to face outdoor elements—whether on a factory roof, a transmission line, or a dockyard—CSM gives you the confidence that it won’t need replacing anytime soon. It’s not just about surviving. It’s about outlasting.
8. What Are Typical Grades and Specifications for CSM?
If you’re thinking of sourcing CSM, you’ll need to talk numbers. Different applications demand different hardness, tensile strength, elongation, and cure systems. Whether you’re making extruded profiles or press-cured gaskets, your material spec must match your process and final use.
Let’s break it down. CSM is sold in various grades, generally defined by Mooney viscosity, chlorine content, and physical property targets. Lower viscosity grades (e.g. D4035) are easier to process but may offer lower mechanical performance. Higher grades (e.g. D6035) provide excellent heat resistance and tear strength, ideal for tougher jobs.
Here are some standard parameters:
Grade | Mooney Viscosity | Hardness (Shore A) | Tensile Strength (MPa) | Elongation (%) |
---|---|---|---|---|
D4035 | 40–50 | 60–70 | ≥25 | ≥450 |
D5035 | 50–60 | 65–75 | ≥25 | ≥450 |
D6035 | 60–70 | 70–80 | ≥25 | ≥450 |
What’s the catch? The wrong grade can slow production, cause surface defects, or compromise product life. Always consult with your compounder or supplier before committing. Ask about oil resistance, flame retardancy, and sulfur peroxide cure compatibility.
Want material that cures faster? Go with peroxide grades. Need higher weather resistance? Choose a higher chlorine content grade. It’s that specific—and that important.
9. How Is CSM Processed in Manufacturing?
CSM isn’t a plug-and-play material. While it blends well with common rubber machinery, it has some quirks that set it apart from EPDM or NR. To get consistent results, manufacturers must understand its chemical behavior and treat it accordingly.
Here’s the real story. CSM mixes well on two-roll mills or internal mixers. It accepts standard fillers like carbon black, silica, and magnesium oxide. But it has low unsaturation—so it needs peroxide or special cure systems to cross-link effectively. The good news? Once cured, it becomes incredibly stable.
Let’s walk through the process:
- Mixing: CSM rubber base is combined with fillers, plasticizers, and stabilizers. Because of its polarity, it can absorb high filler loads while maintaining strength.
- Curing: Sulfur systems work, but peroxide systems are often preferred. They provide superior heat aging and chemical resistance.
- Forming: CSM can be extruded, molded, or calendered. Wall thickness, part geometry, and line speed must be optimized based on grade viscosity.
- Post-Cure: For critical parts, oven curing stabilizes the rubber and removes residual volatiles.
Let’s organize this:
Step | Equipment Used | Key Consideration |
---|---|---|
Mixing | Two-roll mill | Temperature control |
Compounding | Internal mixer | Avoid over-shear |
Forming | Extruder / Molding | Tooling needs matched flow |
Vulcanization | Hot press / Oven | Peroxide system preferred |
Post-curing | Hot air oven | Remove surface tackiness |
But here’s the kicker… Many buyers blame the material when the real issue is poor processing. CSM rewards those who handle it correctly—and punishes shortcuts.
10. What Makes a Good CSM Compound?
Behind every reliable CSM product is a solid compound formula. And no, it’s not just about throwing in some carbon black and cure agent. CSM compounding is part science, part art. A small tweak in filler ratio or accelerator type can dramatically change the final product’s durability, flexibility, or chemical resistance.
Here’s the deal. The base polymer provides the backbone, but it’s the additives that give CSM its application-specific edge. Whether you’re producing high-voltage cable jackets or rubberized fabric for inflatable boats, the compound formula must match both the end-use and the processing method.
Let’s break down the core components:
- Fillers: Carbon black is the go-to for reinforcement and UV resistance. Silica or calcium carbonate can be added to adjust hardness and cost.
- Plasticizers: Paraffinic or naphthenic oils improve flexibility, especially in cold climates. But using too much can weaken tear resistance.
- Cure Systems: CSM accepts both sulfur and peroxide systems. Peroxide offers better heat and chemical resistance but may need co-agents to ensure complete cross-linking.
- Stabilizers and Antioxidants: These additives prevent thermal degradation and extend the lifespan of rubber parts exposed to heat or oxidants.
- Process Aids: Stearic acid, zinc oxide, and processing oils help with flow, mixing, and mold release.
But what’s the secret? Balance. A good CSM compound doesn’t just meet specs on paper. It has to process well, cure reliably, and perform over time. That’s why formulation development often takes trial, testing, and customer feedback.
If you’re buying ready-made compounds, always ask your supplier for mechanical property sheets, thermal aging data, and chemical resistance charts. Don’t settle for general-purpose grades unless your application is truly non-critical.
11. How Can You Identify Quality in Imported CSM?
Let’s face it—sourcing CSM from overseas comes with risks. Not all suppliers play by the same rules, and a poor batch can damage your production, ruin your product, or even harm your brand. So how do you tell the difference between a reliable supplier and a risky one?
This is where it gets interesting… Quality isn’t just about the polymer. It’s about traceability, consistency, and accountability. When you source CSM—especially from low-cost regions—you need tools to verify the material’s true quality.
Here’s what you should always check:
- COA & Batch Numbers: Ask for a Certificate of Analysis with every order. Look for Mooney viscosity, tensile strength, elongation, and ash content.
- Visual & Physical Inspection: Examine color consistency, packaging quality, and rubber flow behavior during mixing.
- Lab Testing: Use internal or third-party labs to verify thermal aging, ozone resistance, and chemical compatibility.
What’s the real story? A slightly cheaper price is no help if your cable jackets crack, your roofing sheets delaminate, or your hoses fail pressure tests. A good supplier will be transparent, technical, and responsive. If they’re evasive or slow, that’s your signal to move on.
12. What Are the Storage and Handling Best Practices for CSM?
CSM might be tough once installed, but in raw form, it still needs care. Storage errors can lead to premature aging, poor vulcanization, or contamination—and those issues don’t show up until after your product is in the field.
Let’s break it down. The golden rules of rubber storage apply, but CSM has specific needs due to its chemical composition. It resists oxygen and moisture better than natural rubber, but prolonged exposure to heat or UV light can degrade its processability.
Here’s how to keep it safe:
- Store in Cool, Dark Places: Ideal storage temperature is 15–25°C. Keep the rubber away from direct sunlight or fluorescent lights.
- Avoid High Humidity: Moisture doesn’t destroy CSM, but it can affect additives like peroxides or stearic acid if already blended.
- Use FIFO Inventory: CSM has a shelf life of 12–18 months in most forms. Use older lots first to avoid waste.
- Protect from Contaminants: Oils, solvents, and even plasticizers from other rubbers can contaminate raw CSM rolls. Use sealed bags or wrap the rolls in kraft paper.
Here’s a best-practices table:
Storage Factor | Best Practice |
---|---|
Temperature | 15–25°C (avoid heat) |
Light Exposure | Keep in dark or UV-blocking area |
Humidity | Store below 60% RH |
Shelf Life | Use within 12–18 months |
Physical Protection | Keep covered and elevated from floor |
Here’s what to remember. You could buy the best compound on earth, but if it sits in a hot warehouse for six months, it won’t cure right. Proper handling is part of the quality equation—don’t leave it to chance.
13. What Challenges Exist When Sourcing CSM from China?
Sourcing from China can offer great value, but let’s not sugarcoat it—it also brings challenges. Between language barriers, QC inconsistencies, and IP sensitivity, getting CSM from China isn’t something you want to do casually.
But here’s the kicker… These challenges are manageable. And many Chinese manufacturers have matured tremendously, offering international-grade materials and support—if you know what to look for.
Here are common issues:
- Spec Clarity: Make sure you’re using the same property definitions. Mooney viscosity and hardness values can be interpreted differently.
- Batch Consistency: Some small factories lack process controls, leading to lot-to-lot variation.
- MOQ & Lead Times: You may be forced into higher quantities or longer production cycles, especially during peak seasons.
- Communication Lag: Time zones and translation can delay feedback or technical discussions.
Strategies to minimize risk:
Risk Factor | Mitigation Strategy |
---|---|
Miscommunication | Use bilingual contracts + drawings |
QC Issues | Ask for samples + third-party audits |
Delivery Delays | Buffer lead times by 2–3 weeks |
Grade Confusion | Request full technical datasheets |
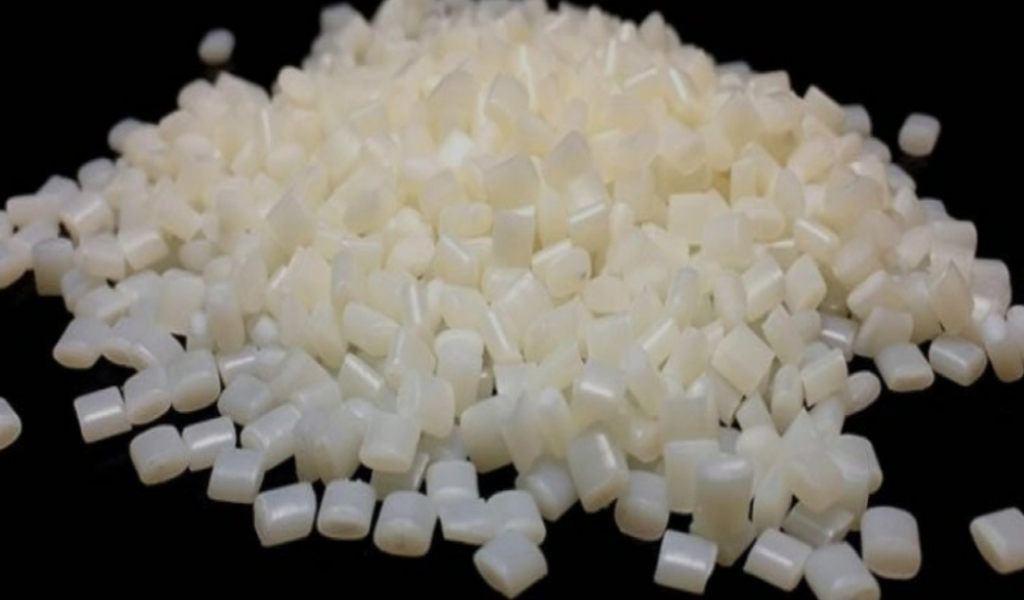
14. What Innovations Are Happening in CSM Development?
Even a classic material like CSM is evolving. With growing environmental pressures and performance demands, suppliers are experimenting with greener chemistries, faster cure systems, and more customizable grades.
What’s the real story? Most innovation today revolves around two key areas: sustainability and performance enhancement. As regulations tighten, companies are finding ways to reduce solvent usage, improve cross-link density, and extend thermal life.
Key innovation trends:
- Solvent-Free Chlorosulfonation: A new process that replaces hexane-based systems with water-phase methods to lower VOCs.
- Peroxide-Optimized Grades: Faster cure, better thermal resistance, and reduced compression set in cable and automotive uses.
- Recyclable Blends: Partial blends of CSM with TPEs or EVA to create materials that can be reshaped and reused in non-critical applications.
Innovation snapshot:
Innovation Area | Description |
---|---|
Green Processing | Lower VOC emissions, solvent-free options |
Performance Tuning | Better tear, aging, and oil resistance |
Blended Formulations | Cost-reduced with partial reusability |
Nano Fillers | Improve mechanical strength and longevity |
But here’s what matters. These upgrades don’t sacrifice legacy performance. They add value—whether through ease of processing, improved safety, or alignment with your ESG goals.
15. What Should You Ask Before Buying CSM?
Let’s say you’ve decided CSM fits your product line. Great. Now comes the deal-making. But what do you ask your supplier to make sure you’re not buying blind?
Here’s the deal. Asking the right questions saves time, money, and headaches. It also helps you filter out weak suppliers and identify long-term partners who understand your needs.
Checklist of questions:
- “Can you provide full technical data and COA for every lot?”
- “What are your standard grades and lead times?”
- “Can you provide technical support during testing and application??”
- “Do you offer custom formulation services tailored to our processing and performance needs?”
Key evaluation points:
Question Topic | Why It Matters |
---|---|
Technical Data | Ensures fit for your process |
Traceability | Helps with complaint resolution |
Compound Flexibility | Adapts to your equipment or mold |
Manufacturing Scale | Indicates stability and delivery ability |
Export Experience | Reduces paperwork and customs risks |
So here’s the takeaway. Your questions define your results. Go in prepared. Ask like a pro. Get answers that make sense—not just for today, but for your next 100 tons.
FAQ
Q1: What is CSM (Hypalon rubber)?
CSM is a type of synthetic rubber made from chlorosulfonated polyethylene. It’s known for excellent resistance to UV, ozone, chemicals, and weather aging.
Q2: How does CSM compare to EPDM?
CSM outperforms EPDM in chemical and flame resistance, though EPDM may offer better low-temperature flexibility and a lower cost.
Q3: Why did DuPont stop producing Hypalon?
DuPont stopped Hypalon production in 2010 due to internal restructuring and environmental regulation pressures—not material defects.
Q4: Where is CSM still available today?
CSM is produced in China, Japan, and Europe by various manufacturers under different trade names.
Q5: What industries use CSM rubber most?
CSM is widely used in cable insulation, roofing membranes, automotive hoses, marine sealing, and chemical-resistant linings.